Reactive sputtering is a specialized thin-film deposition technique used to create compound films with precise chemical compositions and properties. It involves introducing a reactive gas, such as oxygen or nitrogen, into a sputtering chamber where it reacts with the target material ejected by plasma. This process enables the formation of compounds like oxides, nitrides, or carbides directly on the substrate. The primary purpose of reactive sputtering is to produce high-quality, uniform thin films with controlled stoichiometry and enhanced properties, such as hardness, corrosion resistance, or optical characteristics, at a faster rate compared to traditional sputtering methods. This makes it ideal for applications in semiconductor manufacturing, optical coatings, and protective barrier layers.
Key Points Explained:
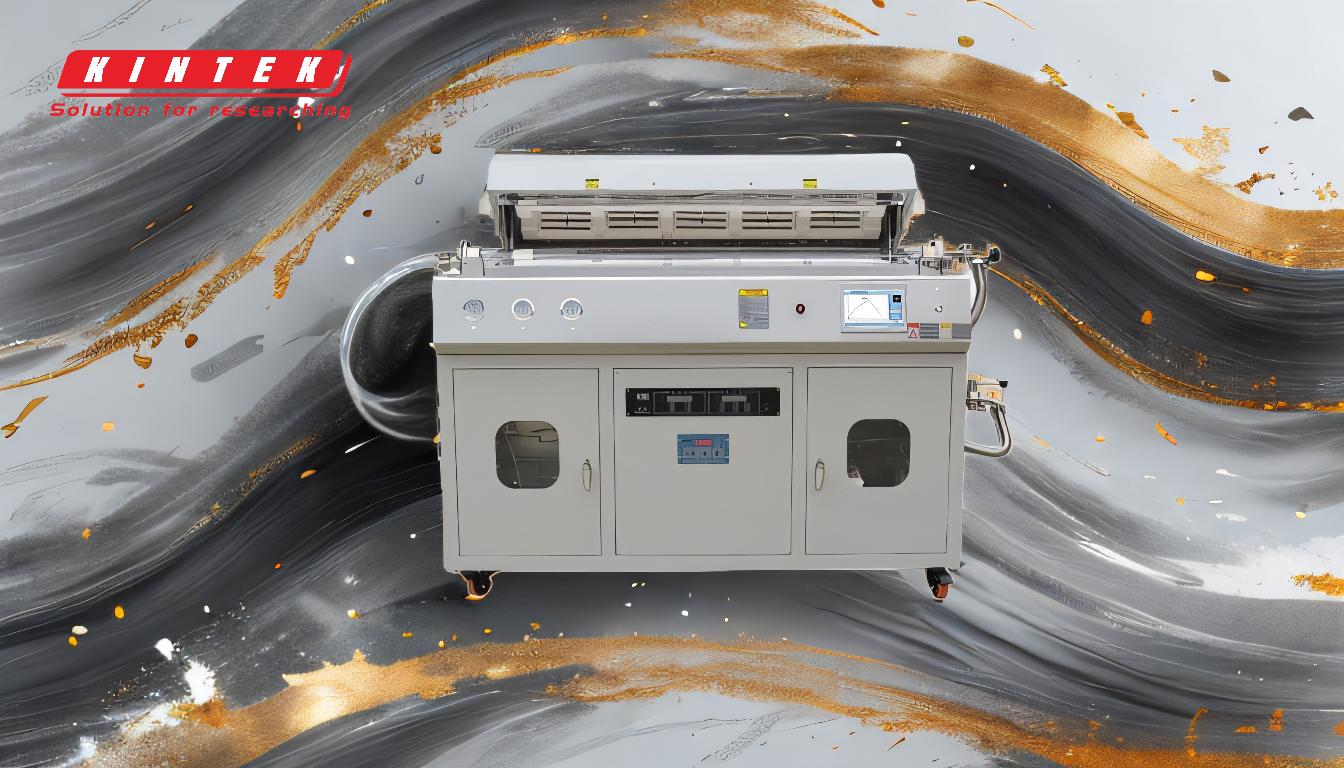
-
Formation of Compound Films:
- Reactive sputtering is used to create thin films of compounds, such as oxides, nitrides, or carbides, by introducing reactive gases like oxygen or nitrogen into the sputtering chamber.
- Example: Aluminum (Al) reacts with oxygen (O₂) to form aluminum oxide (Al₂O₃), which is deposited as a thin film on the substrate.
- This process allows for the precise control of film composition and properties, which is critical for applications like barrier layers or optical coatings.
-
Enhanced Deposition Rate:
- Reactive sputtering significantly increases the rate at which compound films are deposited compared to traditional sputtering methods.
- By forcing chemical reactions to occur during the deposition process, the materials bond more efficiently, leading to faster film formation.
- This is particularly advantageous for industrial applications where high throughput is required.
-
Precision in Film Composition and Structure:
- The introduction of reactive gases enables the creation of films with precisely regulated stoichiometry and structure.
- This is essential for applications in Physical Vapor Deposition (PVD), where specific material properties, such as hardness, corrosion resistance, or optical transparency, are required.
- Example: Titanium nitride (TiN) films, known for their hardness and wear resistance, are commonly produced using reactive sputtering.
-
Versatility in Material Selection:
- Reactive sputtering can be used with a wide range of target materials and reactive gases, allowing for the deposition of various compound films.
- Common reactive gases include oxygen (for oxides), nitrogen (for nitrides), and acetylene (for carbides).
- This versatility makes the technique suitable for diverse industries, including electronics, optics, and coatings.
-
Applications in Advanced Technologies:
- Reactive sputtering is widely used in semiconductor manufacturing to create barrier layers, such as titanium nitride (TiN), which prevent diffusion between layers.
- It is also employed in optical coatings to produce films with specific refractive indices or anti-reflective properties.
- Additionally, it is used to deposit protective coatings that enhance the durability and performance of tools and components.
-
Comparison to Traditional Sputtering:
- Unlike traditional sputtering, which primarily deposits pure metals or alloys, reactive sputtering enables the deposition of compound films directly.
- Traditional sputtering is slower for compound films because it requires additional steps to achieve the desired chemical composition.
- Reactive sputtering simplifies the process by integrating the chemical reaction into the deposition step.
-
Optimization of Process Parameters:
- The success of reactive sputtering depends on carefully controlling parameters such as gas flow rates, pressure, and power input.
- Proper optimization ensures uniform film deposition and prevents issues like target poisoning, where the reactive gas forms a compound layer on the target surface, reducing sputtering efficiency.
By leveraging these key points, reactive sputtering offers a highly efficient and versatile method for producing advanced thin films with tailored properties, making it indispensable in modern manufacturing and technology development.
Summary Table:
Key Aspect | Details |
---|---|
Formation of Compound Films | Creates oxides, nitrides, or carbides using reactive gases like O₂ or N₂. |
Enhanced Deposition Rate | Faster film formation compared to traditional sputtering methods. |
Precision in Composition | Enables controlled stoichiometry and tailored material properties. |
Versatility | Works with various target materials and gases for diverse applications. |
Applications | Used in semiconductors, optical coatings, and protective barrier layers. |
Comparison to Traditional | Directly deposits compound films, simplifying the process. |
Optimization | Requires control of gas flow, pressure, and power for uniform deposition. |
Interested in leveraging reactive sputtering for your projects? Contact our experts today to learn more!