Grinding media plays a critical role in the milling efficiency of ball mills and bead mills. Its size, composition, density, and quantity directly influence the energy transfer, particle size reduction, and overall grinding performance. Larger grinding media can deliver higher impact energy, while smaller media increase the frequency of collisions, both of which affect the breakage rate of particles. The composition of the media must be compatible with the material being ground to avoid contamination or unwanted reactions. Additionally, factors such as the filling ratio, rotation speed, and residence time of the material in the mill further determine the grinding efficiency. Optimizing these parameters ensures effective milling, reduced power consumption, and desired particle size distribution.
Key Points Explained:
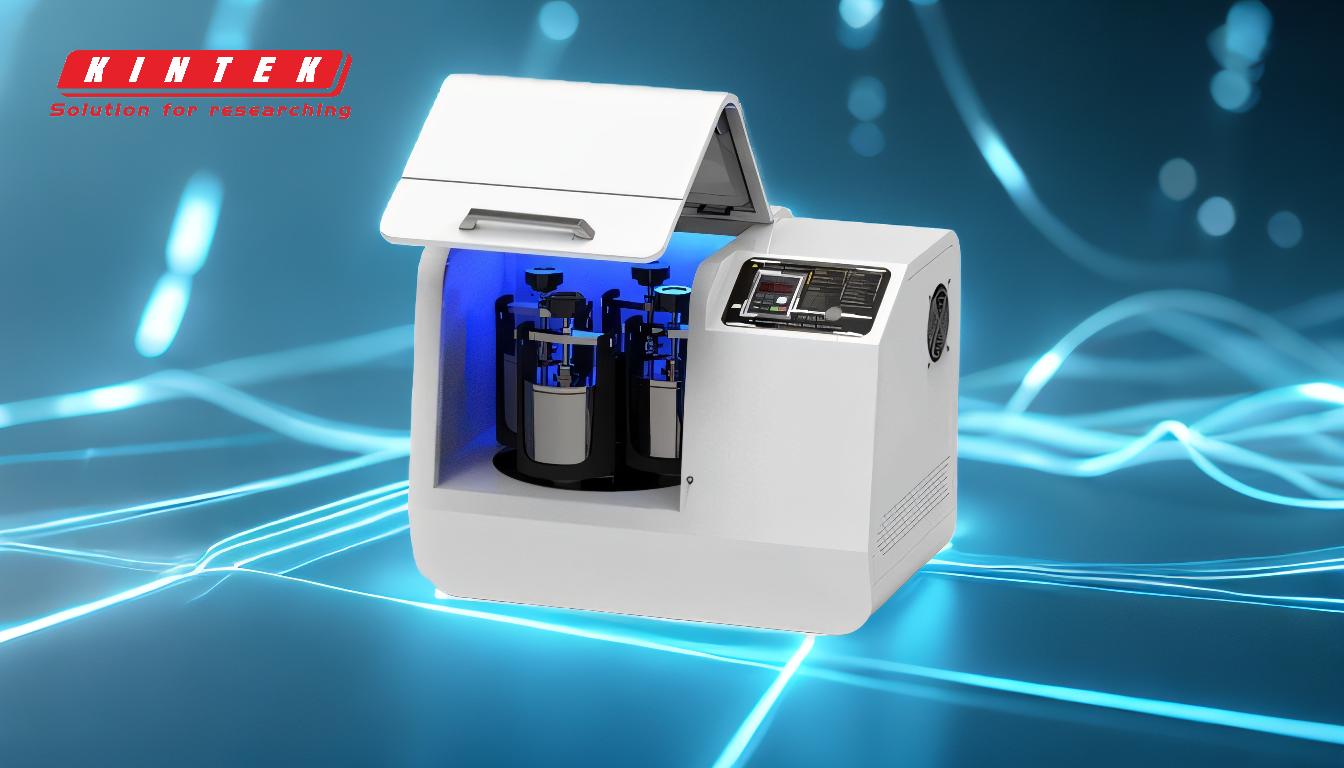
-
Size of Grinding Media:
- The size of grinding media is a primary factor affecting milling efficiency. Larger media provide higher impact energy, which is effective for breaking down coarse particles, while smaller media increase the frequency of collisions, enhancing the grinding of finer particles.
- The choice of media size depends on the target particle size and the material being ground. For example, smaller beads are preferred for achieving ultrafine particle sizes in bead mills.
-
Composition of Grinding Media:
- The composition of grinding media must align with the specific requirements of the grinding application. For instance, ceramic or stainless steel media are often used to avoid contamination in food or pharmaceutical applications.
- Reactive materials may require inert grinding media to prevent chemical interactions that could alter the properties of the final product.
-
Density and Mass of Grinding Media:
- Higher-density media (e.g., steel or zirconia) deliver greater impact energy, improving the grinding efficiency for hard materials.
- The mass of the beads charged in the mill also affects the grinding process. An optimal mass ensures sufficient energy transfer without overloading the mill, which could reduce efficiency.
-
Filling Ratio of the Mill:
- The filling ratio, or the percentage of the mill volume occupied by grinding media, influences the grinding efficiency. An optimal filling ratio ensures adequate media-to-material contact while avoiding excessive friction or energy loss.
- Overfilling can lead to reduced grinding efficiency and increased power consumption, while underfilling may result in insufficient particle breakage.
-
Rotation Speed and Rotor Design:
- The rotation speed of the mill determines the kinetic energy of the grinding media. Higher speeds increase the impact energy and frequency of collisions, enhancing grinding efficiency.
- The design of the rotor (in bead mills) also plays a role. Specialized rotors can improve the distribution of beads and optimize the grinding process.
-
Residence Time and Feed Rate:
- The residence time of the material in the mill chamber affects the degree of milling. Longer residence times allow for more thorough grinding but may reduce throughput.
- The feed rate and level in the vessel must be balanced to ensure consistent grinding without overloading the mill.
-
Impact Energy and Frequency of Collisions:
- The grinding efficiency is determined by the balance between impact energy and the frequency of collisions. Larger media provide higher energy but fewer collisions, while smaller media increase collision frequency but deliver less energy.
- Optimizing these factors ensures efficient particle size reduction and minimizes energy consumption.
-
Application-Specific Considerations:
- The choice of grinding media and milling parameters depends on the specific application. For example, fine grinding of pigments may require smaller beads and higher rotor speeds, while coarse grinding of minerals may benefit from larger media and lower speeds.
- Compatibility with the material being ground is crucial to avoid contamination or unwanted reactions.
By carefully selecting and optimizing these factors, milling efficiency can be significantly improved, leading to better product quality, reduced energy consumption, and lower operational costs.
Summary Table:
Factor | Impact on Milling Efficiency |
---|---|
Size of Grinding Media | Larger media = higher impact energy; smaller media = increased collision frequency. |
Composition | Must match material being ground to avoid contamination or reactions. |
Density and Mass | Higher density = greater impact energy; optimal mass = efficient energy transfer. |
Filling Ratio | Optimal ratio = adequate media-to-material contact; avoids friction or energy loss. |
Rotation Speed | Higher speeds = increased impact energy and collision frequency. |
Residence Time | Longer times = thorough grinding; shorter times = higher throughput. |
Application-Specific | Media and parameters vary based on material and desired particle size. |
Ready to optimize your milling process? Contact our experts today for tailored solutions!