The sputtering process is a widely used technique in nanotechnology and materials science for depositing thin films of materials onto substrates. It involves bombarding a target material with energetic ions, typically from an inert gas like argon, causing atoms to be ejected from the target's surface. These ejected atoms then travel through a vacuum or low-pressure environment and deposit onto a substrate, forming a thin film. The process is highly precise and is used in applications ranging from semiconductor manufacturing to creating reflective coatings. Key steps include creating a vacuum, introducing an inert gas, ionizing the gas, and using a magnetic field to direct the ions toward the target material. The ejected atoms condense on the substrate, resulting in a uniform and high-quality thin film.
Key Points Explained:
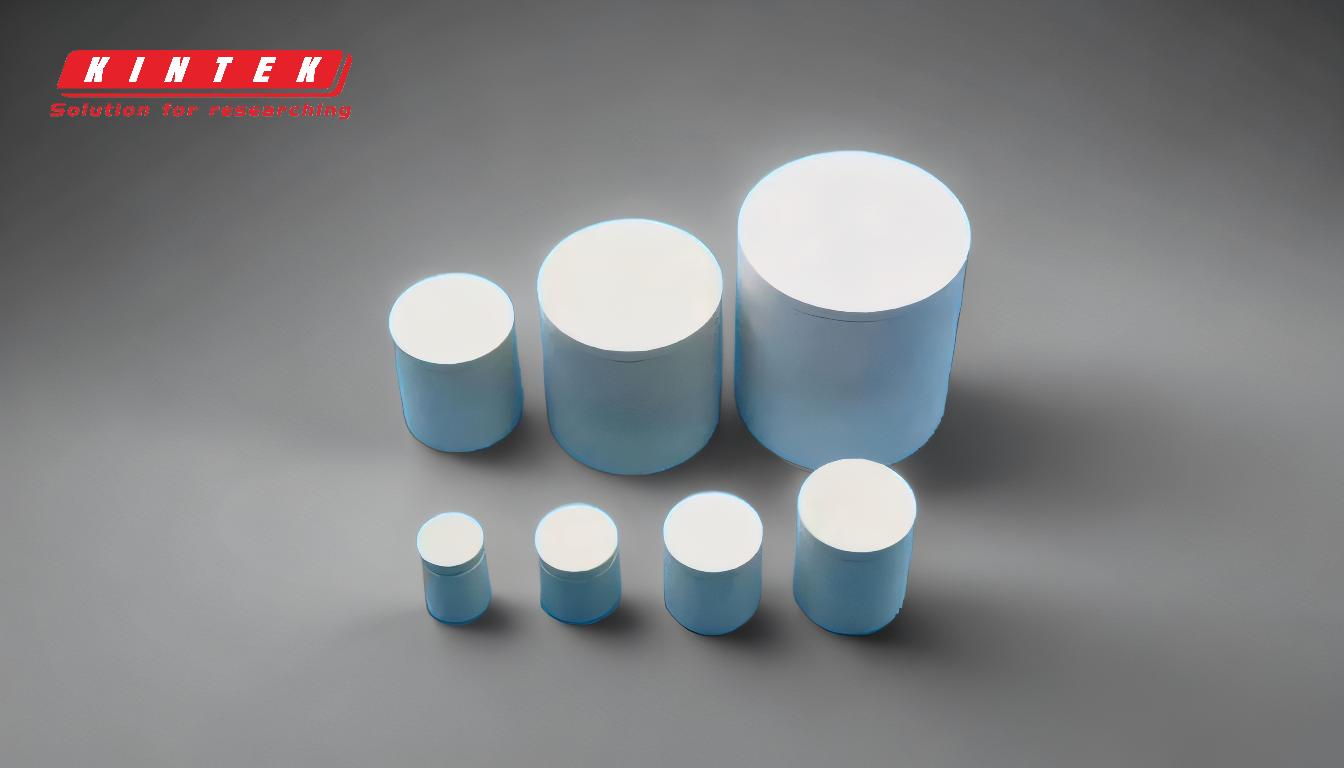
-
Definition of Sputtering
- Sputtering is a physical process where atoms are ejected from the surface of a target material due to bombardment by energetic ions.
- This process is driven by momentum transfer between the ions and the target atoms, causing the latter to be dislodged and ejected into the surrounding environment.
-
Key Steps in the Sputtering Process
- Vacuum Creation: The process begins by evacuating the reaction chamber to create a vacuum, typically around 1 Pa (0.0000145 psi), to remove moisture and impurities.
- Inert Gas Introduction: An inert gas, such as argon, is introduced into the chamber to create a low-pressure atmosphere.
- Ionization of Gas: A high voltage (3-5 kV) is applied to ionize the gas atoms, forming a plasma of positively charged ions.
- Target Bombardment: The positively charged ions are accelerated toward the negatively charged target material, causing atoms to be ejected from the target's surface.
- Deposition on Substrate: The ejected atoms travel through the chamber and deposit onto the substrate, forming a thin film.
-
Role of Magnetic Fields
- A magnetic field is often used to confine and direct the plasma, enhancing the efficiency of the sputtering process.
- This technique, known as magnetron sputtering, increases the density of ions and improves the uniformity of the deposited film.
-
Temperature Considerations
- The chamber is typically heated to temperatures ranging from 150°C to 750°C, depending on the material being deposited.
- Heating helps improve the adhesion and quality of the thin film.
-
Applications of Sputtering
- Semiconductor Manufacturing: Sputtering is used to deposit thin films of materials like silicon, aluminum, and copper in the production of integrated circuits.
- Optical Coatings: It is used to create reflective coatings for mirrors and lenses.
- Packaging Materials: Sputtered films are used in packaging materials, such as the metallic layers in potato chip bags.
- Advanced Materials: The process is also used to create nanomaterials and advanced coatings for various industrial applications.
-
Advantages of Sputtering
- Precision: The process allows for highly controlled deposition of materials, making it suitable for creating thin films with precise thicknesses and compositions.
- Versatility: It can be used with a wide range of materials, including metals, ceramics, and polymers.
- Uniformity: Sputtering produces films with excellent uniformity and adhesion to the substrate.
-
Historical Context
- Sputtering has been used since the early 1800s and has evolved into a mature and reliable technique for thin film deposition.
- Its applications have expanded significantly with advancements in materials science and nanotechnology.
-
Process Optimization
- Pressure Control: The process starts at lower pressures to minimize contamination from residual gases before introducing argon at higher pressures (10^-1 to 10^-3 mbar).
- Plasma Confinement: Magnetic fields and electromagnetic excitation are used to optimize the ionization and confinement of the plasma.
By following these steps and principles, the sputtering process enables the creation of high-quality thin films with applications across a wide range of industries. Its precision, versatility, and ability to produce uniform coatings make it a cornerstone of modern materials science and nanotechnology.
Summary Table:
Aspect | Details |
---|---|
Definition | Ejection of atoms from a target material due to bombardment by energetic ions. |
Key Steps | 1. Vacuum creation 2. Inert gas introduction 3. Ionization 4. Target bombardment 5. Deposition |
Role of Magnetic Fields | Enhances plasma confinement and improves film uniformity (magnetron sputtering). |
Temperature Range | 150°C to 750°C, depending on the material. |
Applications | Semiconductor manufacturing, optical coatings, packaging materials, nanomaterials. |
Advantages | Precision, versatility, and uniformity in thin film deposition. |
Discover how sputtering can enhance your projects—contact our experts today for more information!