Rapid Thermal Annealing (RTA) is a process used in semiconductor manufacturing to heat wafers to high temperatures for short durations. The typical temperature range for RTA is between 1000 K and 1500 K (approximately 727°C to 1227°C). The wafer is rapidly heated to this temperature range, held there for a few seconds, and then quickly cooled (quenched). This process is crucial for achieving desired material properties, such as dopant activation and defect repair, without causing excessive diffusion or damage to the wafer.
Key Points Explained:
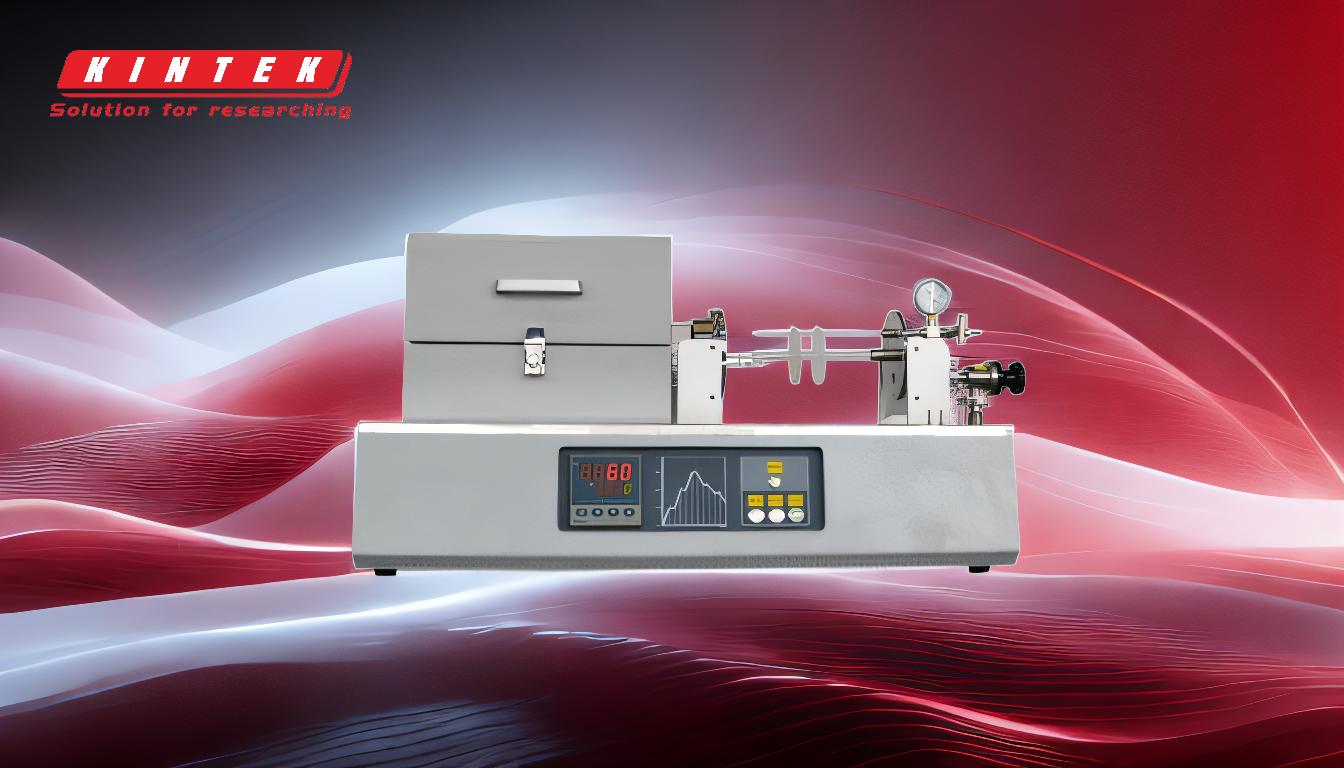
-
Temperature Range for RTA:
- The temperature range for Rapid Thermal Annealing is typically 1000 K to 1500 K.
- This range is chosen because it is high enough to facilitate processes like dopant activation and defect repair, but not so high as to cause excessive diffusion or damage to the wafer.
-
Rapid Heating:
- The wafer is heated rapidly from ambient temperature to the target range.
- Rapid heating is essential to minimize the time the wafer spends at intermediate temperatures, which can lead to unwanted diffusion or other thermal effects.
-
Short Duration at High Temperature:
- Once the wafer reaches the target temperature, it is held there for a few seconds.
- This short duration is critical to achieve the desired material modifications while minimizing the risk of thermal damage or excessive dopant diffusion.
-
Quenching:
- After the brief high-temperature hold, the wafer is quenched (rapidly cooled).
- Quenching helps to lock in the desired material properties by preventing further diffusion or changes that could occur during slower cooling.
-
Importance of Temperature Control:
- Precise control of the temperature is crucial in RTA.
- Too low a temperature may not achieve the desired material modifications, while too high a temperature can cause damage to the wafer or excessive diffusion of dopants.
-
Applications of RTA:
- RTA is widely used in semiconductor manufacturing for processes like dopant activation, defect repair, and crystallization.
- The ability to quickly heat and cool wafers makes RTA particularly useful for modern semiconductor devices, where precise control over material properties is essential.
-
Comparison with Conventional Annealing:
- Unlike conventional annealing, which involves slower heating and cooling cycles, RTA is characterized by its rapid thermal cycles.
- This rapidity allows for better control over the thermal budget, reducing the risk of unwanted diffusion and enabling the fabrication of smaller, more precise semiconductor devices.
-
Thermal Budget Considerations:
- The thermal budget refers to the total amount of thermal energy the wafer is exposed to during the annealing process.
- RTA's rapid heating and cooling cycles help to minimize the thermal budget, which is crucial for maintaining the integrity of modern semiconductor devices with increasingly smaller feature sizes.
In summary, the temperature of Rapid Thermal Annealing typically ranges from 1000 K to 1500 K, with the wafer being rapidly heated to this range, held for a few seconds, and then quenched. This process is essential for achieving precise material properties in semiconductor manufacturing while minimizing the risk of thermal damage or excessive diffusion.
Summary Table:
Aspect | Details |
---|---|
Temperature Range | 1000 K to 1500 K (727°C to 1227°C) |
Heating Process | Rapid heating from ambient to target temperature |
Duration at High Temp | A few seconds |
Cooling Process | Rapid quenching to lock in material properties |
Key Applications | Dopant activation, defect repair, crystallization |
Advantages | Minimizes thermal budget, prevents excessive diffusion, enhances precision |
Optimize your semiconductor manufacturing process with Rapid Thermal Annealing—contact our experts today to learn more!