Ball milling is a mechanical process used to grind, mix, and blend materials into fine powders or disperse particles in a medium. It involves the use of a rotating cylindrical chamber (ball mill) filled with grinding media (balls) and the material to be processed. The theory of ball milling revolves around the principles of impact, attrition, and shear forces generated by the collision of grinding media with the material. As the mill rotates, the balls cascade and tumble, creating kinetic energy that breaks down the material into smaller particles. The process is influenced by factors such as mill speed, ball size, material properties, and milling time, which determine the efficiency and outcome of the process.
Key Points Explained:
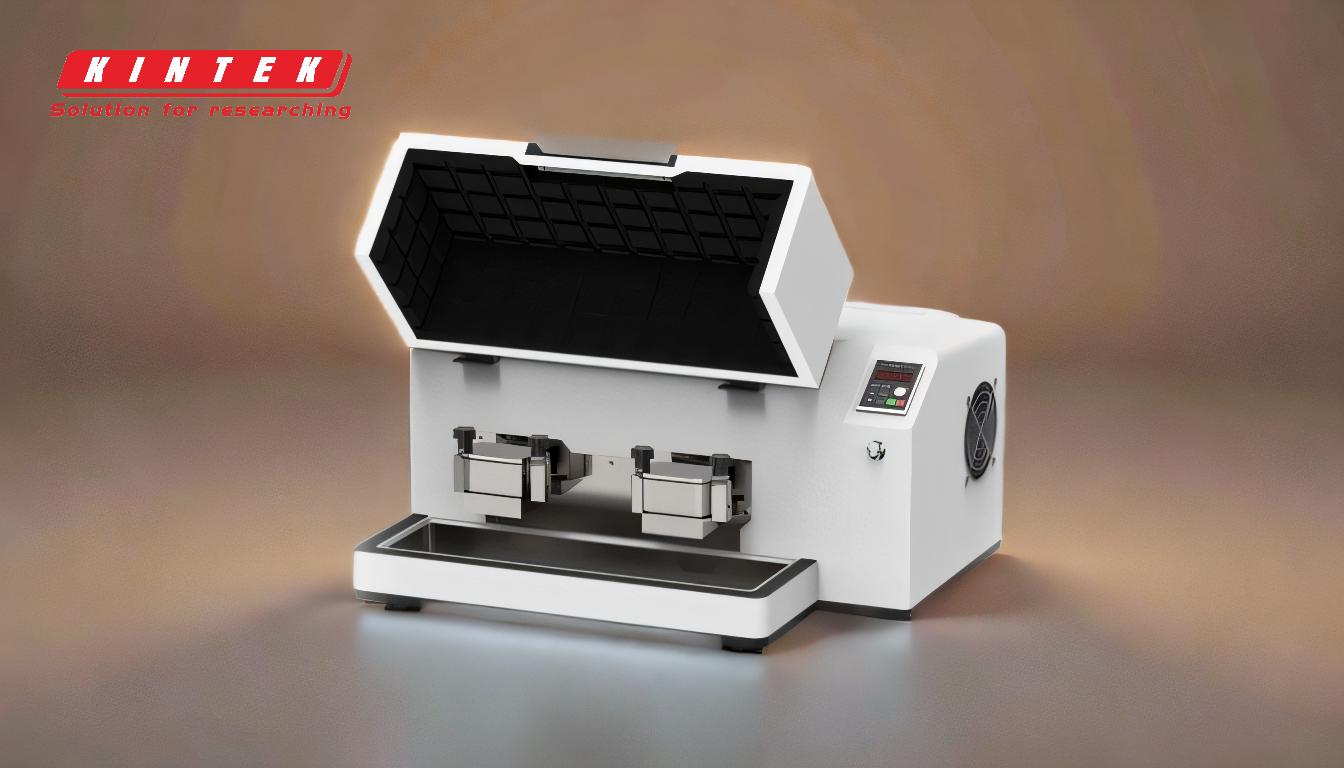
-
Mechanism of Ball Milling:
- Ball milling operates on the principles of impact, attrition, and shear forces.
- Impact occurs when the grinding media (balls) collide with the material, breaking it into smaller particles.
- Attrition involves the rubbing of particles against each other or the mill walls, leading to size reduction.
- Shear forces are generated during the cascading and tumbling motion of the balls, which further aids in particle size reduction and mixing.
-
Components of a Ball Mill:
- Cylindrical Chamber: A rotating container that holds the grinding media and material.
- Grinding Media: Typically spherical balls made of steel, ceramic, or other hard materials. The size and material of the balls affect the milling efficiency.
- Material to be Processed: The substance being ground, mixed, or blended.
- Drive System: A motor that rotates the mill at a controlled speed.
-
Kinetics of Ball Milling:
- The efficiency of ball milling depends on the kinetic energy transferred from the grinding media to the material.
- The kinetic energy is influenced by the rotational speed of the mill. Optimal speed ensures that the balls cascade and tumble effectively without being centrifugally pinned to the walls.
- The size and density of the grinding media also play a role in determining the energy transfer.
-
Factors Affecting Ball Milling:
- Mill Speed: Too low a speed results in insufficient energy transfer, while too high a speed can cause the balls to centrifuge, reducing grinding efficiency.
- Ball Size and Material: Larger balls deliver more impact energy, while smaller balls provide better surface contact for attrition. The material of the balls must be harder than the material being processed.
- Milling Time: Longer milling times generally lead to finer particles but may also cause overheating or contamination.
- Material Properties: The hardness, brittleness, and size of the material affect how easily it can be ground.
-
Applications of Ball Milling:
- Particle Size Reduction: Used in industries like pharmaceuticals, ceramics, and mining to produce fine powders.
- Mechanical Alloying: A process where different materials are blended at the atomic level to create alloys or composites.
- Dispersion and Mixing: Used to uniformly mix or disperse particles in a medium, such as in paint or ink production.
-
Advantages of Ball Milling:
- Versatile and capable of processing a wide range of materials.
- Can achieve fine particle sizes and uniform mixing.
- Suitable for both batch and continuous operations.
-
Limitations of Ball Milling:
- High energy consumption due to the mechanical process.
- Potential for contamination from wear of grinding media or mill walls.
- Risk of overheating, which can alter material properties.
-
Mathematical Modeling:
- The ball milling process can be modeled using equations that describe the energy transfer, particle size distribution, and milling kinetics.
- Common models include the Rittinger's Law, Kick's Law, and Bond's Law, which relate energy input to particle size reduction.
-
Types of Ball Mills:
- Planetary Ball Mills: High-energy mills with multiple grinding stations, suitable for fine grinding and mechanical alloying.
- Tumbling Ball Mills: Traditional mills where the cylinder rotates horizontally, commonly used in mining and ceramics.
- Vibratory Ball Mills: Use vibrations to enhance grinding efficiency, often used for small-scale operations.
-
Recent Advances:
- Development of nano-ball milling for producing nanoparticles.
- Use of computational simulations to optimize milling parameters and predict outcomes.
- Integration of in-situ monitoring systems to track particle size and temperature during milling.
By understanding the theory and mechanics of ball milling, users can optimize the process for specific applications, ensuring efficient and effective material processing.
Summary Table:
Aspect | Details |
---|---|
Mechanism | Impact, attrition, and shear forces for particle size reduction and mixing. |
Components | Cylindrical chamber, grinding media, material, and drive system. |
Kinetics | Kinetic energy transfer depends on mill speed, ball size, and density. |
Applications | Particle size reduction, mechanical alloying, and dispersion. |
Advantages | Versatile, fine particle sizes, and uniform mixing. |
Limitations | High energy consumption, contamination risk, and overheating. |
Types of Ball Mills | Planetary, tumbling, and vibratory ball mills. |
Optimize your material processing with ball milling—contact our experts today!