Twin screw extrusion is a versatile industrial process used extensively in industries such as food, plastics, and chemicals. It involves the plasticization and homogenization of raw materials under controlled heat and pressure, facilitated by the intermeshing rotation of two screws within a barrel. This process ensures thorough mixing, melting, and shaping of materials, making it ideal for producing consistent and high-quality products. Twin screw extrusion is valued for its flexibility, efficiency, and ability to handle a wide range of materials and formulations.
Key Points Explained:
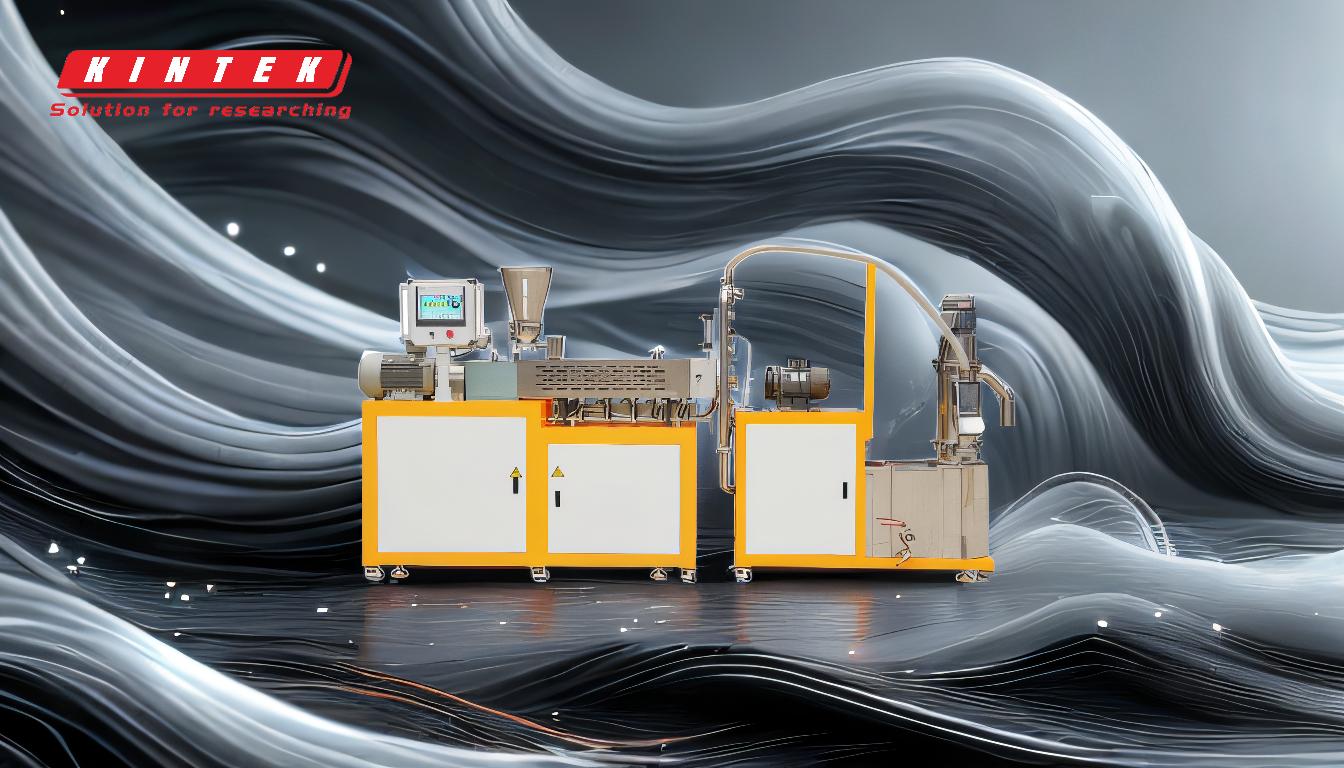
-
Definition and Principle of Twin Screw Extrusion:
- Twin screw extrusion is a process that uses two intermeshing screws rotating within a barrel to plasticize and homogenize raw materials.
- The screws work together to transport, mix, and compress materials, ensuring uniform melting and blending.
- Heat and pressure are applied to transform the raw material into a molten state, which is then shaped into the desired product.
-
Components of a Twin Screw Extruder:
- Barrel: Houses the screws and provides the necessary heat and pressure for material processing.
- Screws: Two intermeshing screws that rotate to transport, mix, and compress the material. Screw design can vary based on the application.
- Feed Hopper: Where raw materials are introduced into the extruder.
- Die: Shapes the molten material into the final product form (e.g., pellets, sheets, or profiles).
- Heating and Cooling Systems: Regulate the temperature to ensure proper material processing.
-
Types of Twin Screw Extruders:
- Co-Rotating: Both screws rotate in the same direction, providing excellent mixing and self-cleaning properties. Commonly used for compounding and blending.
- Counter-Rotating: Screws rotate in opposite directions, offering better conveying and degassing capabilities. Often used for high-viscosity materials.
-
Advantages of Twin Screw Extrusion:
- Flexibility: Can process a wide range of materials, including polymers, food products, and chemicals.
- Efficiency: High throughput and consistent product quality due to precise control over processing parameters.
- Mixing Capabilities: Excellent mixing and homogenization, making it suitable for complex formulations.
- Scalability: Easily scalable from laboratory to industrial production.
-
Applications of Twin Screw Extrusion:
- Food Industry: Production of snacks, cereals, and pet food.
- Plastics Industry: Compounding, blending, and pelletizing of polymers.
- Chemical Industry: Processing of adhesives, sealants, and coatings.
- Pharmaceuticals: Encapsulation and controlled-release formulations.
-
Process Parameters:
- Temperature: Controlled heating zones ensure proper melting and prevent degradation.
- Screw Speed: Affects the residence time and shear rate, influencing material properties.
- Feed Rate: Determines the throughput and consistency of the process.
- Pressure: Ensures proper material flow and shaping through the die.
-
Considerations for Equipment Purchasers:
- Material Compatibility: Ensure the extruder can handle the specific materials and formulations required.
- Throughput Requirements: Match the extruder’s capacity with production needs.
- Energy Efficiency: Look for energy-saving features to reduce operational costs.
- Maintenance and Durability: Choose equipment with easy maintenance and long-lasting components.
- Customization Options: Consider the availability of customizable screw designs and barrel configurations.
By understanding these key points, purchasers can make informed decisions when selecting twin screw extrusion equipment, ensuring it meets their specific production requirements and delivers optimal performance.
Summary Table:
Aspect | Details |
---|---|
Definition | Uses two intermeshing screws to plasticize and homogenize raw materials. |
Components | Barrel, screws, feed hopper, die, heating/cooling systems. |
Types | Co-rotating (same direction) and counter-rotating (opposite directions). |
Advantages | Flexibility, efficiency, excellent mixing, and scalability. |
Applications | Food, plastics, chemicals, and pharmaceuticals. |
Process Parameters | Temperature, screw speed, feed rate, and pressure. |
Purchasing Tips | Material compatibility, throughput, energy efficiency, and customization. |
Ready to optimize your material processing? Contact us today to find the perfect twin screw extruder for your needs!