Internal mixers are critical machines in the rubber and plastic manufacturing industries, designed for plasticating, mixing, and finalizing the blend of materials. They are particularly valued for their ability to handle viscous mixtures, ensuring consistent and high-quality outputs. The machine consists of key components like rotors, a mixing chamber, and cooling circulator systems, which work together to maintain precise temperature and pressure conditions. Internal mixers are chosen for their efficiency, reliability, and adaptability to various mixing processes, making them indispensable in industries where material consistency and quality are paramount.
Key Points Explained:
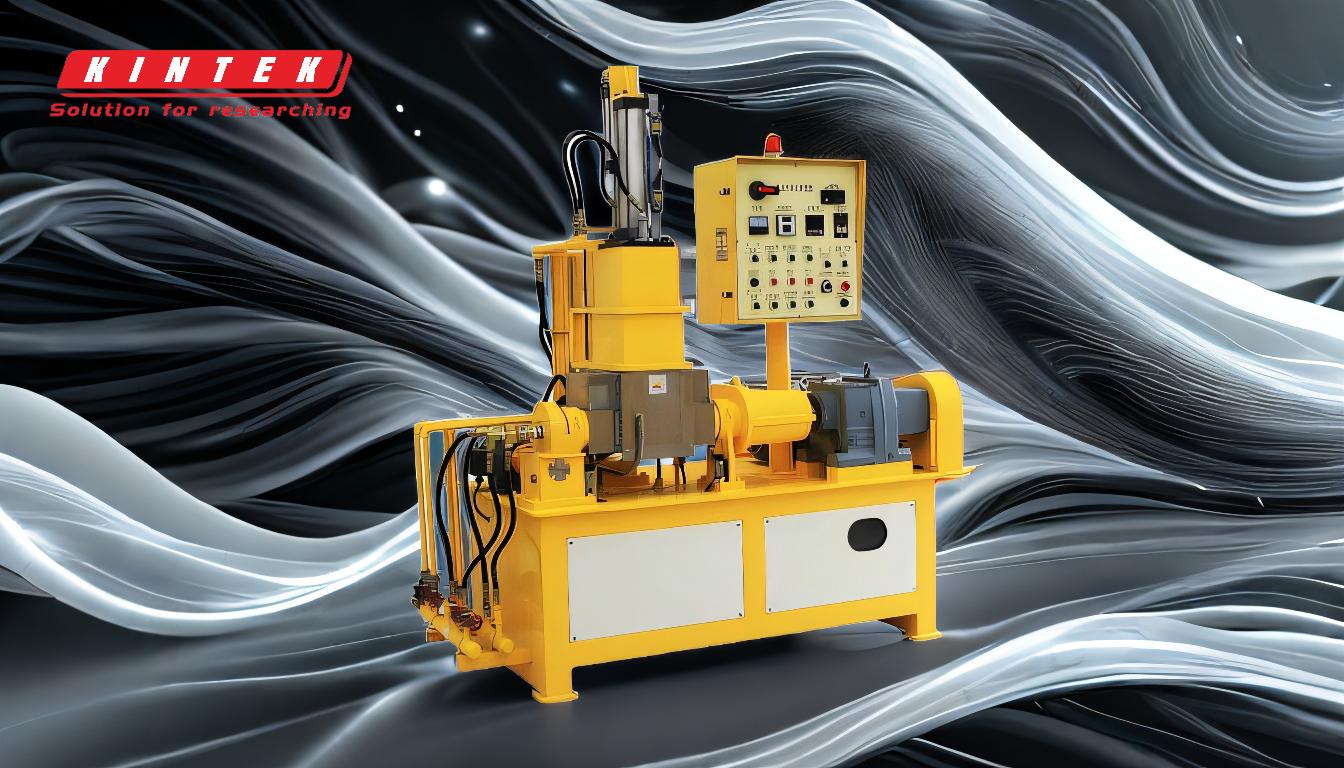
-
Primary Functions of Internal Mixers:
- Plasticating and Mixing: Internal mixers are primarily used to plasticate (soften) and mix rubber and plastic materials. This process ensures that the materials are uniformly blended, which is essential for achieving consistent product quality.
- Final Mixing: They are also used for the final mixing stage, where additives like carbon black, fillers, and liquid softeners are incorporated into the base material to achieve the desired properties.
-
Handling Viscous Materials:
- Internal mixers are specifically designed to handle viscous mixtures, which are common in rubber manufacturing. Their robust construction and powerful motor systems allow them to maintain a smooth and constant flow of materials, even under high viscosity conditions.
-
Key Components:
- Mixing Chamber: The core working part where the actual mixing occurs. It houses the rotors and is designed to withstand high temperatures and pressures.
- Rotors: These are the rotating elements that mix the materials. Different rotor designs are available to accommodate various mixing processes and material types.
- Cooling and Lubrication Systems: Essential for maintaining optimal operating temperatures and ensuring the longevity of the machine.
- Sealing and Transmission Devices: These components ensure that the mixer operates efficiently and safely, preventing leaks and maintaining consistent rotor speeds.
-
Operational Process:
- Preheating and Parameter Check: Before mixing, the machine is preheated, and system parameters are checked to ensure everything is within the required range.
- Material Addition: Raw rubber is added first, followed by small materials, fillers, and liquid softeners. The sequence and timing are critical for achieving a uniform mix.
- Temperature Monitoring: The temperature is closely monitored throughout the process to prevent overheating and ensure the material properties are not compromised.
- Post-Mixing Processing: After mixing, the material is processed on an open mill where sulfur is added, and the final product is cooled and labeled for later use.
-
Advantages in Manufacturing:
- Consistency and Quality: Internal mixers are known for producing consistent and high-quality mixes, which are crucial for industries like automotive, aerospace, and consumer goods.
- Efficiency: They are highly efficient, capable of handling large volumes of material in a relatively short time, which helps in reducing production downtime.
- Adaptability: With different rotor options and adjustable settings, internal mixers can be tailored to meet specific mixing requirements, making them versatile tools in various manufacturing processes.
-
Maintenance and Downtime Considerations:
- Preventive Maintenance: Regular maintenance of the cooling, lubrication, and sealing systems is essential to prevent failures that could lead to significant downtime.
- Blockage Clearance: In case of blockages, internal mixers can be challenging to clear, which underscores the importance of proper operation and maintenance practices.
In summary, internal mixers are indispensable in the rubber and plastic industries due to their ability to handle viscous materials, ensure consistent mix quality, and adapt to various processing needs. Their robust design and efficient operation make them a preferred choice for manufacturers aiming for high-quality outputs and minimized downtime.
Summary Table:
Key Aspect | Details |
---|---|
Primary Functions | Plasticating, mixing, and finalizing rubber and plastic materials. |
Handling Viscous Materials | Designed for smooth flow under high viscosity conditions. |
Key Components | Mixing chamber, rotors, cooling systems, sealing, and transmission devices. |
Operational Process | Preheating, material addition, temperature monitoring, and post-mixing. |
Advantages | Consistency, efficiency, and adaptability for various manufacturing needs. |
Maintenance | Regular preventive maintenance to minimize downtime and ensure longevity. |
Ready to enhance your manufacturing process? Contact us today to learn more about internal mixers!