The wet ball mill method is a grinding process used to reduce materials into fine particles, typically in the presence of a liquid medium such as water. This method is widely used in industries like mining, ceramics, and pharmaceuticals due to its ability to produce uniform particle sizes and handle both dry and wet materials. The process involves loading the ball mill with grinding media (usually steel or ceramic balls) and the material to be ground, along with a liquid. As the mill rotates, the grinding media crushes and grinds the material into a fine slurry. The wet ball mill method is particularly advantageous for producing ultra-fine powders, maintaining sterility, and handling toxic or abrasive materials.
Key Points Explained:
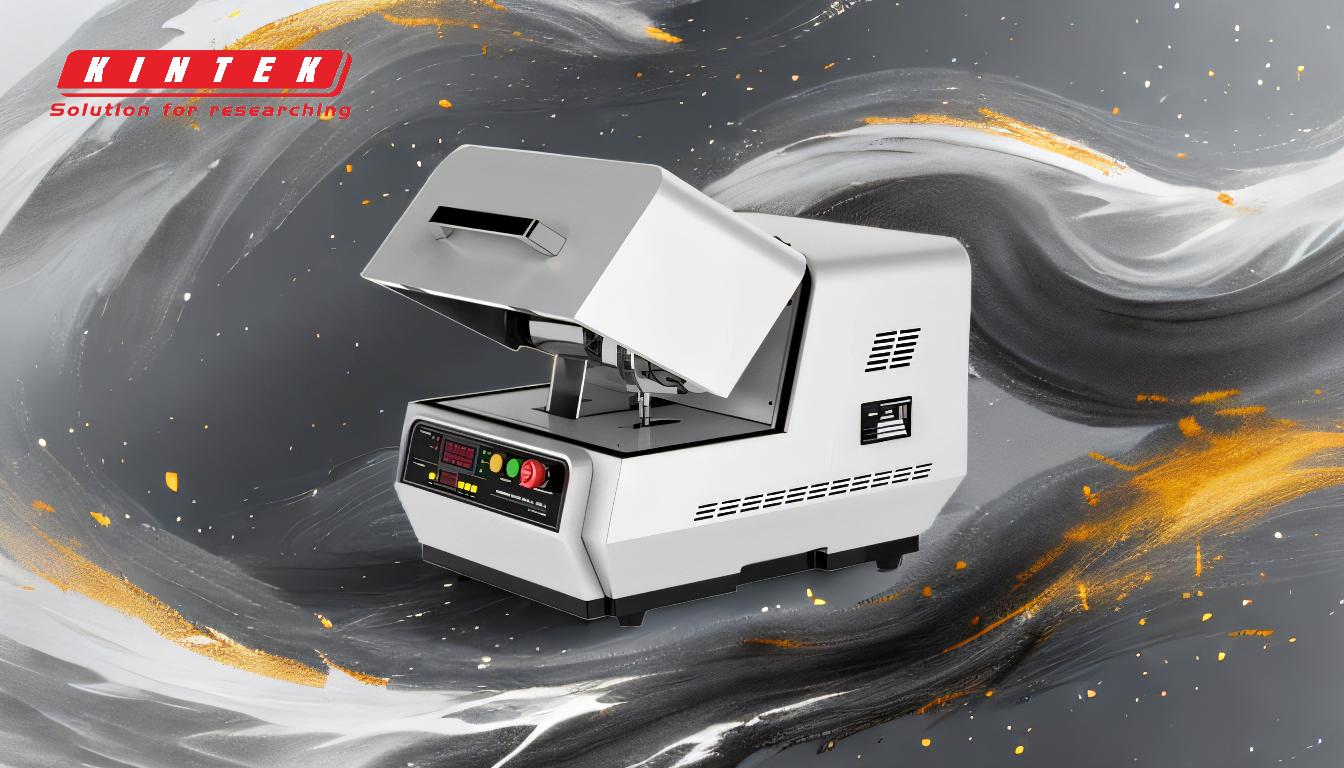
-
Definition of Wet Ball Mill Method:
- The wet ball mill method is a grinding technique that uses a ball mill to reduce materials into fine particles in the presence of a liquid medium, typically water.
- It is a versatile process suitable for both wet and dry grinding, but the wet method is preferred for producing finer particles and handling certain types of materials.
-
Components of a Wet Ball Mill:
- Grinding Media: Usually steel or ceramic balls that crush and grind the material.
- Material to be Ground: The substance that needs to be reduced in particle size.
- Liquid Medium: Typically water, which aids in the grinding process and helps in the formation of a slurry.
- Mill Chamber: The container where the grinding process takes place.
-
Process of Wet Ball Milling:
- Loading: The grinding media, material, and liquid are loaded into the mill chamber.
- Rotation: The mill is rotated, causing the grinding media to crush and grind the material.
- Grinding: The material is ground into fine particles, forming a slurry with the liquid medium.
- Discharge: The slurry is discharged from the mill for further processing or use.
-
Advantages of Wet Ball Mill Method:
- Fine Particle Size: Produces very fine powder with particle sizes less than or equal to 10 microns.
- Suitability for Toxic Materials: Enclosed system allows for safe milling of toxic materials.
- Wide Range of Applications: Can be used in various industries including mining, ceramics, and pharmaceuticals.
- Continuous Operation: Capable of running continuously, which is beneficial for large-scale production.
- Effective for Abrasive Materials: Can handle and grind abrasive materials effectively.
-
Comparison with Dry Ball Mill Method:
- Particle Size: Wet milling generally produces finer particles compared to dry milling.
- Handling of Materials: Wet milling is better suited for materials that are difficult to grind dry or are toxic.
- Energy Consumption: Wet milling can sometimes be more energy-efficient due to the lubricating effect of the liquid medium.
-
Types of Ball Mills:
- Planetary Ball Mills: High-energy mills suitable for fine grinding and mixing.
- Mixer Mills: Used for small-scale grinding and mixing.
- Vibration Mills: Use vibrations to grind materials, suitable for small to medium-sized batches.
- Horizontal Rolling Ball Mills: Suitable for large-scale production, with capacities up to several hundred liters.
-
Applications of Wet Ball Mill Method:
- Mining: Used to grind ores and minerals into fine particles for further processing.
- Ceramics: Used to grind ceramic materials into fine powders for manufacturing.
- Pharmaceuticals: Used to grind active pharmaceutical ingredients (APIs) into fine powders for drug formulation.
- Chemical Industry: Used for grinding and mixing chemicals to produce uniform particle sizes.
-
Maintenance and Cleaning:
- Easy Cleaning: The use of a liquid medium makes cleaning the mill easier compared to dry milling.
- Low Maintenance: Wet ball mills generally require less maintenance due to the lubricating effect of the liquid medium.
-
Energy Consumption and Efficiency:
- Low Energy Consumption: Wet milling can be more energy-efficient due to the reduced friction between particles and grinding media.
- Efficiency: The process is efficient in producing fine particles with minimal energy input.
-
Cost Considerations:
- Inexpensive Method: The wet ball mill method is relatively inexpensive and easy to perform.
- Crystal Defects: The process can produce crystal defects, which may be beneficial for certain applications, such as increasing the reactivity of materials.
In summary, the wet ball mill method is a highly effective and versatile grinding process that offers numerous advantages, including the ability to produce fine particles, handle toxic and abrasive materials, and operate continuously. Its applications span across various industries, making it an essential tool in material processing and manufacturing.
Summary Table:
Aspect | Details |
---|---|
Definition | Grinding process using a ball mill with a liquid medium (e.g., water). |
Key Components | Grinding media (steel/ceramic balls), material, liquid medium, mill chamber. |
Process Steps | Loading, rotation, grinding, discharge. |
Advantages | Fine particle size, handles toxic/abrasive materials, continuous operation. |
Applications | Mining, ceramics, pharmaceuticals, chemical industry. |
Maintenance | Easy cleaning, low maintenance due to liquid medium. |
Energy Efficiency | Low energy consumption, high efficiency. |
Cost | Inexpensive, produces crystal defects for enhanced reactivity. |
Discover how the wet ball mill method can revolutionize your grinding process—contact us today for expert advice!