Tool and mould design is a highly specialized field within manufacturing that involves the creation of precise tools and moulds used to produce plastic parts and other components. It requires a deep understanding of engineering principles, material properties, and manufacturing processes to ensure the final product meets exact specifications. The design process is complex, involving careful planning, technical expertise, and attention to detail to achieve accurate dimensions and desired design features. This field plays a critical role in industries such as automotive, aerospace, consumer goods, and electronics, where precision and consistency are paramount.
Key Points Explained:
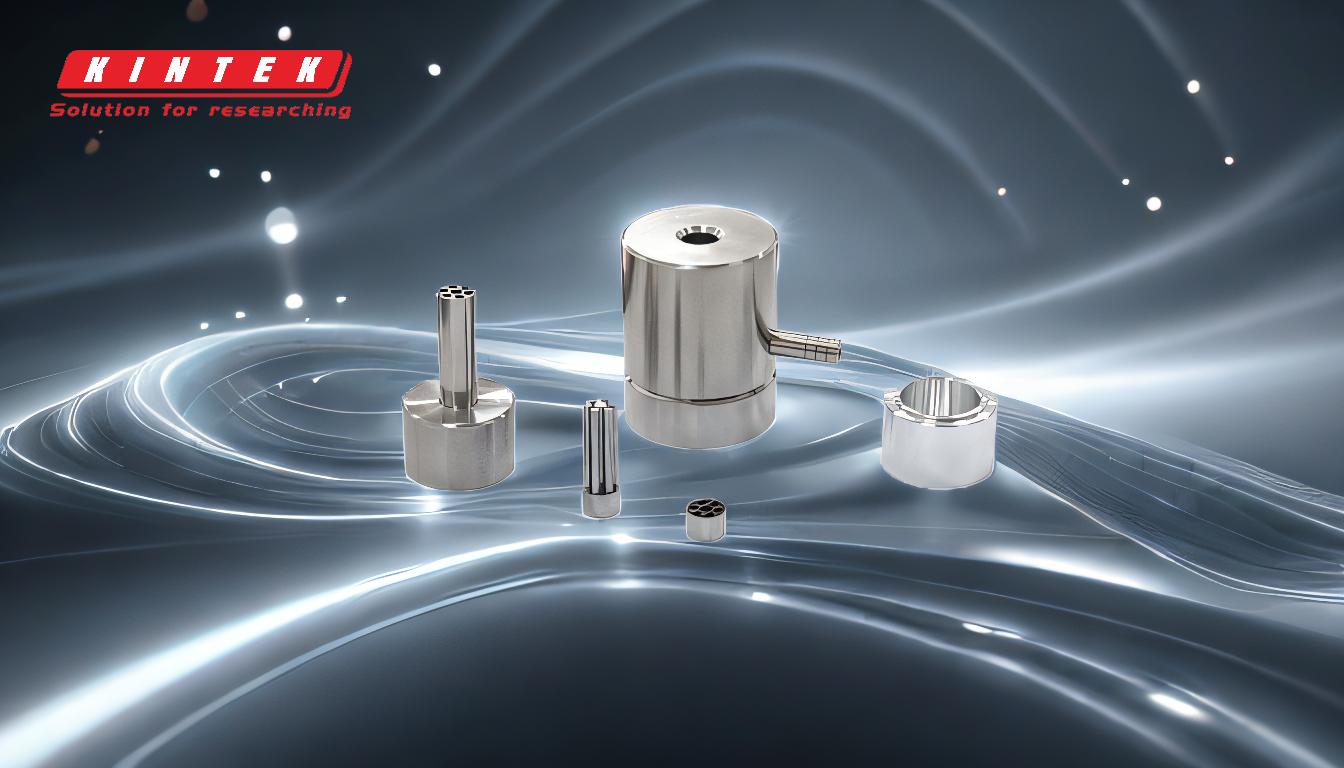
-
Definition of Tool and Mould Design
- Tool and mould design refers to the process of creating the tools and moulds used in manufacturing to produce parts, particularly plastic components.
- It involves designing the physical structures (moulds) that shape materials into the desired form during production.
- The process requires a combination of technical knowledge, engineering principles, and practical expertise.
-
Complexity of the Process
- The design process is intricate and demands high levels of precision to ensure the final product meets exact specifications.
- Factors such as material properties, part geometry, and production methods must be carefully considered.
- Engineers must account for potential challenges like shrinkage, warping, and cooling rates during the design phase.
-
Technical Expertise Required
- Tool and mould designers need a strong background in engineering, including knowledge of CAD (Computer-Aided Design) software.
- Understanding material science is crucial to select the right materials for both the mould and the final product.
- Familiarity with manufacturing processes, such as injection moulding, is essential to optimize the design for production efficiency.
-
Importance of Precision
- Accurate dimensions and design features are critical to ensure the final product functions as intended.
- Even minor errors in the design can lead to defects in the manufactured parts, resulting in increased costs and delays.
- Precision is especially important in industries like automotive and aerospace, where components must meet strict safety and performance standards.
-
Applications in Various Industries
- Tool and mould design is widely used in industries that require mass production of plastic parts, such as consumer electronics, medical devices, and packaging.
- It is also essential in the automotive and aerospace sectors, where lightweight and durable components are needed.
- The ability to produce consistent, high-quality parts makes this field indispensable in modern manufacturing.
-
Components of Tooling
- Tooling includes various components such as cavities, cores, ejector pins, and cooling channels, all of which must be meticulously designed.
- Each component plays a specific role in the moulding process, and their design must be optimized for functionality and durability.
- The interaction between these components determines the efficiency and quality of the production process.
-
Role of Engineering Know-How
- Engineers must apply principles of mechanics, thermodynamics, and fluid dynamics to design effective moulds.
- They must also consider factors like cycle time, material flow, and part ejection to ensure the mould operates smoothly.
- Continuous improvement and innovation are key to staying competitive in this field.
By understanding these key points, one can appreciate the critical role tool and mould design plays in modern manufacturing. It is a field that blends creativity, technical expertise, and precision to produce the tools that shape the products we use every day.
Summary Table:
Key Aspect | Details |
---|---|
Definition | Creation of tools and moulds for manufacturing, especially plastic parts. |
Complexity | High precision, material properties, and production methods are critical. |
Technical Expertise | Requires CAD knowledge, material science, and manufacturing process skills. |
Importance of Precision | Ensures accurate dimensions and functionality of final products. |
Applications | Automotive, aerospace, consumer goods, electronics, and medical devices. |
Components of Tooling | Includes cavities, cores, ejector pins, and cooling channels. |
Engineering Know-How | Involves mechanics, thermodynamics, and fluid dynamics for effective design. |
Need expert tool and mould design for your manufacturing process? Contact us today to get started!