Grinding in the laboratory is a critical process used to achieve high surface quality, accuracy in shape and dimension, and homogenization of samples for chemical and physical analysis. Common equipment includes ball mills, swing mills, jaw crushers, vibratory mills, and planetary mills, each suited for specific applications and desired particle sizes. These tools use high-speed rotating grinding media, such as ceramic balls, to efficiently reduce samples to fine powders, ensuring they meet the necessary analytical standards.
Key Points Explained:
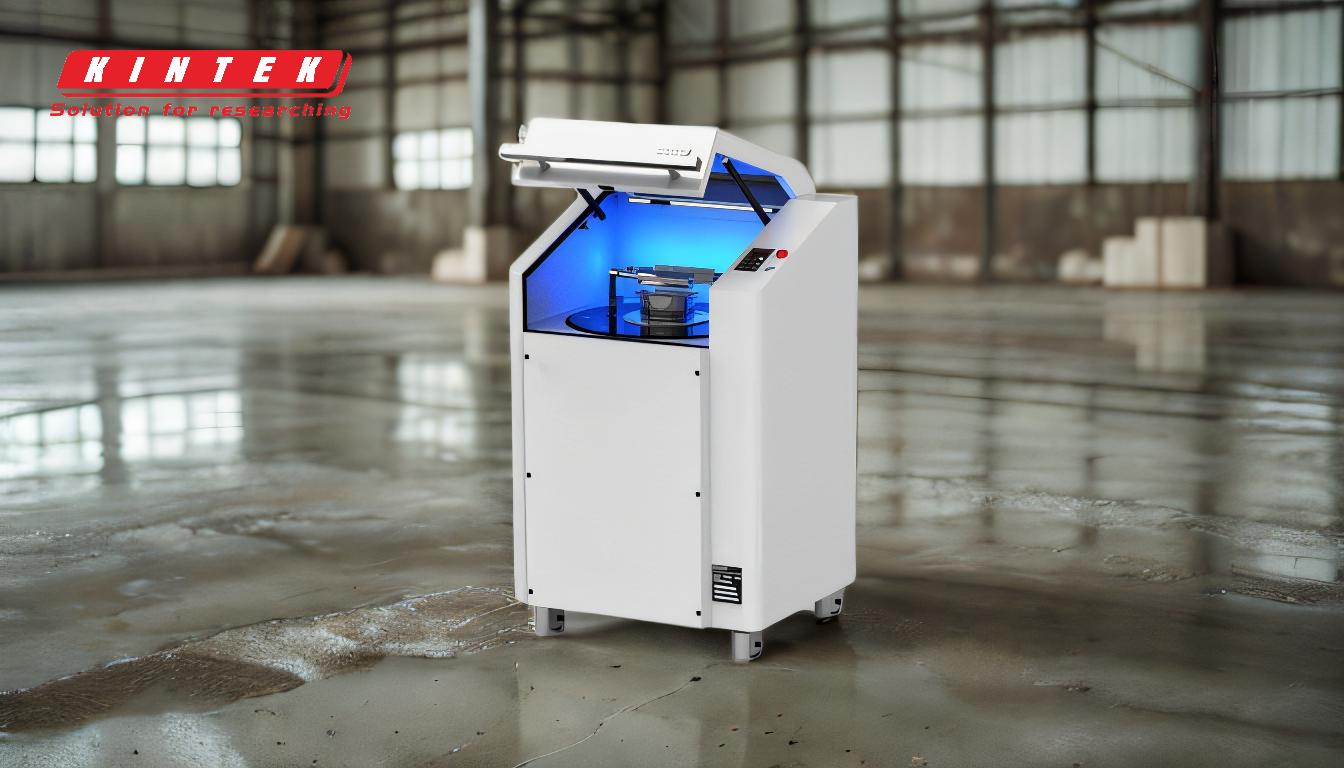
-
Purpose of Grinding in the Laboratory:
- Surface Quality and Accuracy: Grinding is essential for finishing workpieces that require high surface quality and precise dimensions. This is particularly important in materials science and engineering, where surface integrity and dimensional accuracy are critical.
- Homogenization for Analysis: In chemical and physical analytical methods, grinding ensures that specimens are perfectly homogenized. This is crucial for achieving consistent and accurate results, as the uniformity of the sample directly impacts the reliability of the analysis.
-
Types of Grinding Equipment:
- Ball Mills: These are commonly used for grinding materials into fine powders. They consist of a rotating cylinder filled with grinding media (e.g., ceramic balls) that impact and rub the sample, achieving efficient grinding. Ball mills are versatile and can handle a variety of materials.
- Swing Mills: These mills use a swinging motion to grind samples. They are particularly useful for grinding hard, brittle, and fibrous materials. Swing mills are often used in sample preparation for X-ray fluorescence (XRF) and other analytical techniques.
- Jaw Crushers: Primarily used for coarse grinding, jaw crushers are designed to reduce large samples into smaller, more manageable pieces. They are often the first step in the grinding process, especially for hard and brittle materials.
- Vibratory Mills: These mills use high-frequency vibrations to grind samples. They are suitable for fine grinding and are often used in industries where very fine particle sizes are required, such as in pharmaceuticals and ceramics.
- Planetary Mills: These mills use planetary motion to achieve high-energy grinding. They are capable of producing very fine powders and are suitable for a wide range of materials, including metals, ceramics, and polymers.
-
Grinding Media:
- Ceramic Balls: Commonly used in ball mills, ceramic balls are durable and resistant to wear. They are ideal for grinding hard and abrasive materials.
- Stainless Steel Balls: These are used when contamination from the grinding media must be minimized. They are suitable for grinding softer materials and are often used in food and pharmaceutical industries.
- Other Media: Depending on the application, other types of grinding media, such as zirconia or tungsten carbide, may be used. These materials offer specific advantages, such as high density or chemical resistance.
-
Applications of Grinding in the Laboratory:
- Material Science: Grinding is used to prepare samples for analysis in material science, including metallurgy, ceramics, and polymers. The quality of the ground sample can significantly affect the results of tests such as hardness, tensile strength, and microstructure analysis.
- Chemical Analysis: In chemistry, grinding is essential for preparing samples for techniques like spectroscopy, chromatography, and mass spectrometry. Homogenized samples ensure that the analytical results are representative of the entire sample.
- Pharmaceuticals: In the pharmaceutical industry, grinding is used to produce fine powders for drug formulation. The particle size distribution of the ground material can affect the drug's bioavailability and efficacy.
- Environmental Science: Grinding is used to prepare environmental samples, such as soil and sediment, for analysis. This is important for assessing contamination levels and studying environmental processes.
-
Considerations for Selecting Grinding Equipment:
- Sample Type: The choice of grinding equipment depends on the type of sample being processed. Hard, brittle materials may require different equipment than soft, fibrous materials.
- Desired Particle Size: The required fineness of the ground material will influence the selection of grinding equipment. Some mills are better suited for coarse grinding, while others can achieve very fine powders.
- Contamination Risk: The potential for contamination from the grinding media or equipment must be considered, especially in sensitive applications like pharmaceuticals or food analysis.
- Throughput and Efficiency: The volume of samples to be processed and the required grinding time are important factors. High-throughput applications may require more robust or automated grinding systems.
In summary, grinding in the laboratory is a fundamental process that supports a wide range of scientific and industrial applications. The choice of grinding equipment and media depends on the specific requirements of the sample and the desired outcome, ensuring that the ground material meets the necessary standards for further analysis or use.
Summary Table:
Aspect | Details |
---|---|
Purpose | Achieve high surface quality, dimensional accuracy, and sample homogenization. |
Equipment | Ball mills, swing mills, jaw crushers, vibratory mills, planetary mills. |
Grinding Media | Ceramic balls, stainless steel balls, zirconia, tungsten carbide. |
Applications | Material science, chemical analysis, pharmaceuticals, environmental science. |
Selection Factors | Sample type, desired particle size, contamination risk, throughput needs. |
Optimize your lab's grinding process with the right equipment—contact our experts today for personalized recommendations!