Sintering is a manufacturing process used to create solid objects from powdered materials by applying heat and pressure, often without reaching the material's melting point. It is widely used for materials with high melting points, such as ceramics, metals, and polymers, and is essential in industries like powder metallurgy, additive manufacturing, and rapid prototyping. Key materials used in sintering include iron, carbon steels, stainless steel, aluminum, nickel, copper, titanium alloys, molybdenum, tungsten, and ceramics. The process involves equipment like igniters, sintering machines, and systems for ingredient preparation, mixing, and ignition. Methods such as Conventional Sintering, Spark Plasma Sintering (SPS), and Microwave Sintering are employed to achieve desired material properties, including enhanced density, strength, and durability.
Key Points Explained:
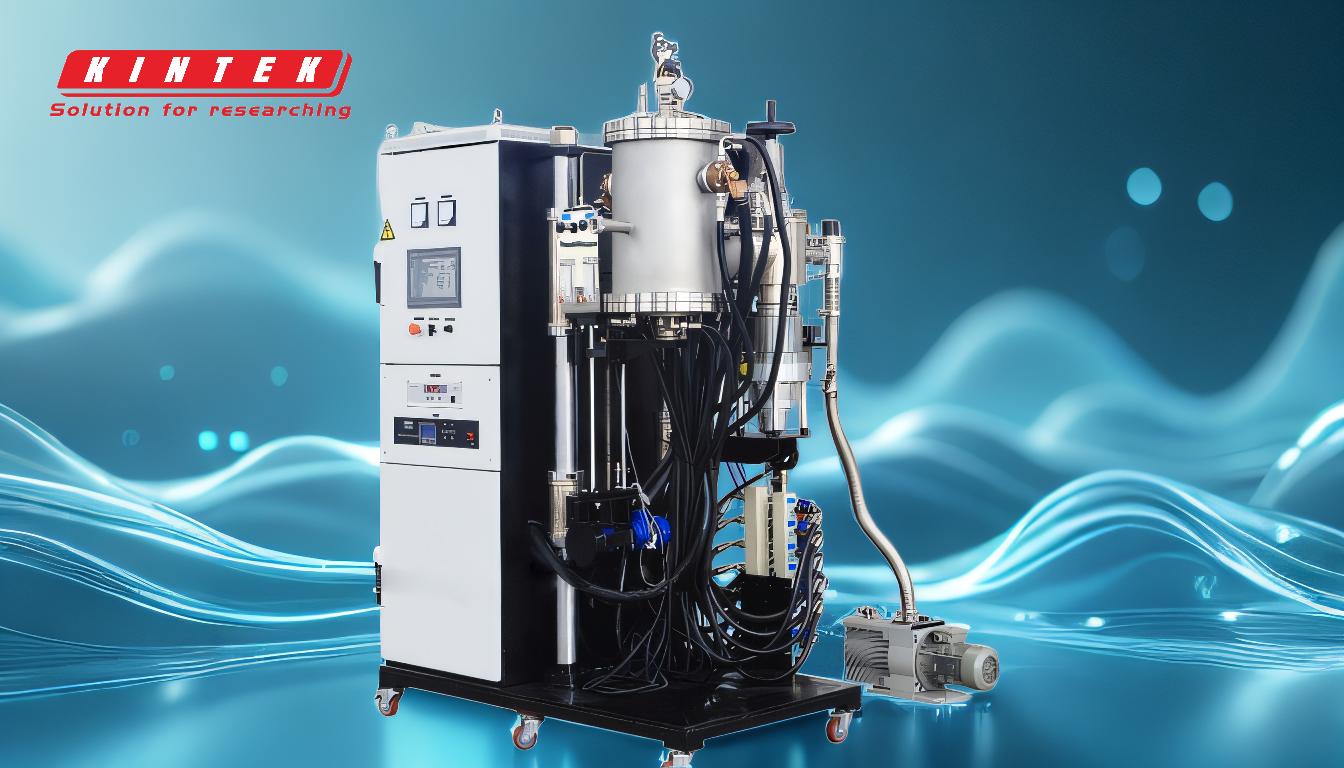
-
Materials Used in Sintering:
- Metals: Common metals include iron, carbon steels, stainless steel, aluminum, nickel, copper, titanium alloys, molybdenum, and tungsten. These materials are chosen for their high melting points and ability to form strong, durable components.
- Ceramics: Used for high-temperature applications, such as gears and bearings, due to their thermal and mechanical stability.
- Polymers: Utilized in rapid prototyping and filter manufacturing, offering versatility and ease of processing.
- Composite Materials: Combinations like iron-copper, copper steels, and iron-nickel alloys are processed to enhance specific properties such as conductivity, strength, or wear resistance.
-
Equipment Used in Sintering:
- Igniters: Essential for initiating the sintering process by burning the mixture in the sintering machine.
- Sintering Machines: These control temperature, pressure, and other parameters to transform powdered materials into solid objects.
- Ingredient Preparation Systems: Ensure proper mixing and preparation of raw materials before sintering.
- Mixing Systems: Combine materials uniformly to achieve consistent properties in the final product.
- Ignition Systems: Provide the necessary heat to start the sintering process.
-
Sintering Methods:
- Conventional Sintering: The most common method, involving heating powdered materials in a furnace under controlled conditions. It is widely used for metals and ceramics.
- Spark Plasma Sintering (SPS): A advanced technique that uses an electric field and pressure to enhance densification. It allows for lower sintering temperatures and shorter processing times, making it suitable for ceramics and metals.
- Microwave Sintering: Utilizes microwave energy to heat materials uniformly and rapidly, often resulting in improved material properties and reduced energy consumption.
-
Applications of Sintering:
- Powder Metallurgy: Used to produce small components like gears, pulleys, and bearings from metal powders. It is particularly useful for materials with high melting points.
- Additive Manufacturing: Sintering is a key process in 3D printing, where metal or polymer powders are fused layer by layer to create complex shapes.
- Rapid Prototyping: Polymers are sintered to quickly produce prototypes for testing and development.
- High-Temperature Components: Ceramics and metals are sintered to create components that can withstand extreme conditions, such as turbine blades or engine parts.
-
Advantages of Sintering:
- Enhanced Material Properties: Sintering improves the density, strength, and durability of materials, making them suitable for demanding applications.
- Cost-Effectiveness: The process minimizes material waste and reduces energy consumption compared to melting and casting.
- Versatility: Sintering can be applied to a wide range of materials, including metals, ceramics, and polymers, making it a versatile manufacturing technique.
- Precision: Sintering allows for the production of complex shapes with high dimensional accuracy, essential for industries like aerospace and automotive.
-
Challenges in Sintering:
- Control of Parameters: Achieving the desired properties requires precise control of temperature, pressure, and sintering time.
- Material Limitations: Not all materials are suitable for sintering, and some may require additional processing steps to achieve the desired properties.
- Equipment Costs: Advanced sintering methods like SPS and microwave sintering require specialized equipment, which can be expensive.
In summary, sintering is a critical process in modern manufacturing, enabling the production of high-performance materials and components. By understanding the materials, equipment, methods, and applications involved, manufacturers can optimize the sintering process to meet specific industrial needs.
Summary Table:
Aspect | Details |
---|---|
Materials Used | Metals (iron, steel, aluminum, etc.), ceramics, polymers, composites |
Equipment | Igniters, sintering machines, ingredient prep systems, mixing systems |
Methods | Conventional Sintering, Spark Plasma Sintering (SPS), Microwave Sintering |
Applications | Powder metallurgy, additive manufacturing, rapid prototyping, high-temp components |
Advantages | Enhanced properties, cost-effectiveness, versatility, precision |
Challenges | Parameter control, material limitations, equipment costs |
Discover how sintering can transform your manufacturing process—contact us today for expert guidance!