Vibratory sieving is a process used to separate, classify, and analyze particles based on their size using vibrating screens or sieves. It is a widely adopted method in industries such as food, pharmaceuticals, chemicals, mining, and construction, as well as in laboratory settings for quality control and research. Vibratory sieving works by applying mechanical vibrations to a sieve or screen, causing particles to move and separate according to their size. This method is efficient, precise, and versatile, making it suitable for both wet and dry materials. Below, we explore the key aspects of vibratory sieving, including its working principles, applications, and benefits.
Key Points Explained:
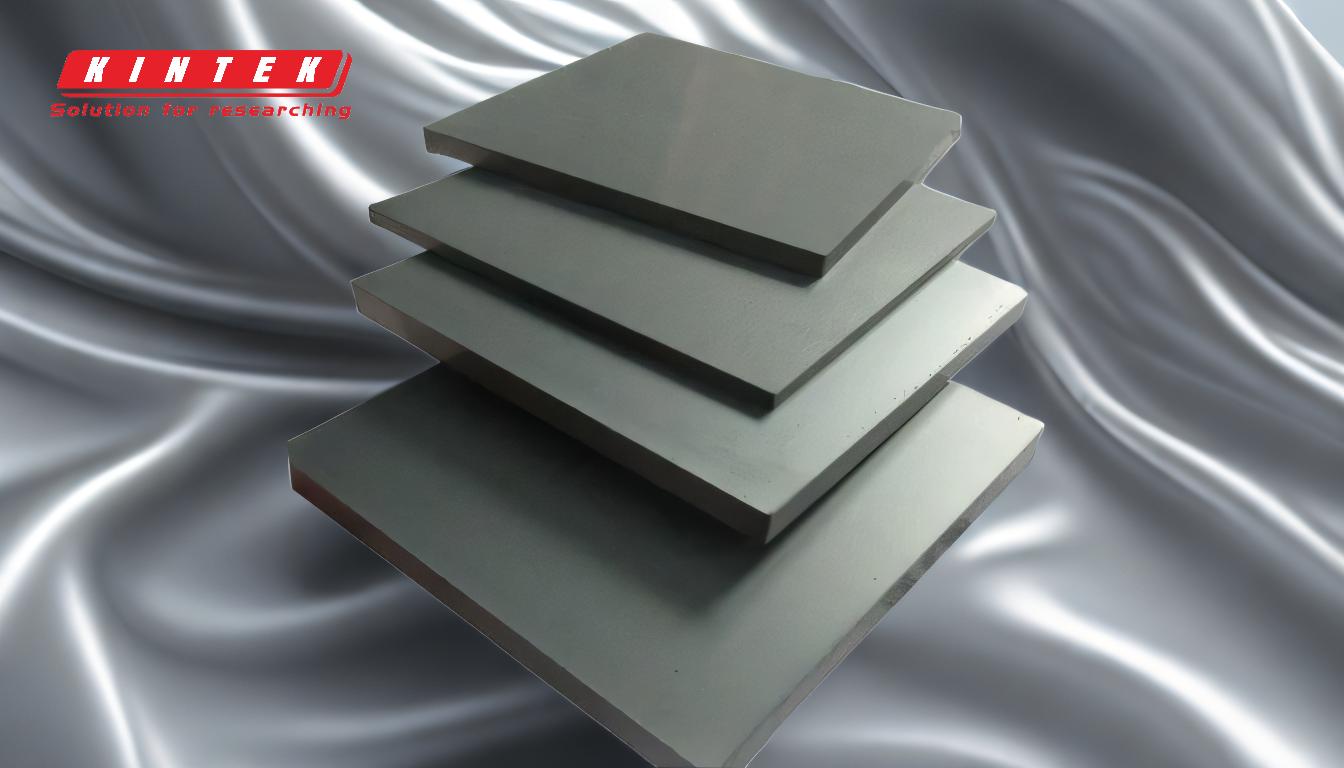
-
Definition and Purpose of Vibratory Sieving:
- Vibratory sieving is a mechanical process that uses vibrating screens or sieves to separate particles by size.
- It is primarily used for particle size analysis, grading, and separation of materials.
- Applications include quality control, research and development, and industrial processes such as food processing, mining, and pharmaceuticals.
-
Working Principle:
- Vibratory sieving works by tilting the sieve surface and applying vibrations, typically generated by a vibration motor.
- The combination of gravity and vibration causes particles to move across the screen in a specific direction.
- Smaller particles pass through the mesh openings, while larger particles are retained on the screen.
-
Types of Vibratory Sieving:
- Rotary Vibrating Sieves: Commonly used for separating large particles and foreign objects, as well as for solid-fluid separation. They are widely applied in industries like ceramics, food, and chemicals.
- Laboratory Test Sieves: Used in labs for precise particle size analysis, sample preparation, and fractioning. They are essential for quality control and research.
- Wet Sieving: Used when materials need to be dispersed in a liquid. It is suitable for materials that are not affected by the liquid.
-
Applications Across Industries:
- Food Processing: Screening food raw materials to ensure consistency and quality.
- Pharmaceuticals: Filtering powdered and granular materials for drug formulation.
- Mining and Metallurgy: Screening ores and minerals for beneficiation and processing.
- Construction: Separating sand, gravel, and cement for building materials.
- Ceramics: Processing materials like alumina and quartz sand.
- Agriculture: Grading seeds and analyzing soil.
-
Benefits of Vibratory Sieving:
- Efficiency: Quickly separates particles by size, saving time and labor.
- Precision: Ensures accurate particle size distribution, which is crucial for product quality.
- Versatility: Can handle both wet and dry materials, as well as a wide range of particle sizes.
- Scalability: Suitable for both small-scale laboratory use and large-scale industrial applications.
-
Key Considerations for Equipment Selection:
- Material Type: Choose sieves based on the material being processed (e.g., powders, aggregates, or liquids).
- Particle Size Range: Ensure the sieve mesh size matches the required particle size range.
- Wet vs. Dry Sieving: Select equipment designed for wet sieving if liquids are involved.
- Industry-Specific Requirements: Consider specialized sieves for industries like food, pharmaceuticals, or mining.
-
Common Challenges and Solutions:
- Clogging: Fine particles can clog sieve openings. Solutions include using anti-clogging mesh or wet sieving.
- Noise and Vibration: High vibration levels can cause noise and equipment wear. Proper maintenance and vibration dampening can mitigate these issues.
- Consistency: Ensuring consistent results requires regular calibration and cleaning of sieves.
-
Future Trends in Vibratory Sieving:
- Automation: Increasing use of automated systems for higher efficiency and reduced human error.
- Advanced Materials: Development of more durable and precise sieve materials for longer lifespan and better performance.
- Sustainability: Focus on energy-efficient equipment and processes to reduce environmental impact.
Vibratory sieving is a critical process in many industries, offering a reliable and efficient method for particle size analysis and material separation. By understanding its principles, applications, and benefits, equipment and consumable purchasers can make informed decisions to meet their specific needs. Whether for laboratory research or industrial production, vibratory sieving plays a vital role in ensuring product quality and consistency.
Summary Table:
Aspect | Details |
---|---|
Definition | Mechanical process using vibrating screens to separate particles by size. |
Applications | Food, pharmaceuticals, mining, construction, ceramics, agriculture, labs. |
Benefits | Efficiency, precision, versatility, scalability. |
Types | Rotary vibrating sieves, laboratory test sieves, wet sieving. |
Challenges | Clogging, noise, consistency. Solutions include anti-clogging mesh and maintenance. |
Future Trends | Automation, advanced materials, sustainability. |
Optimize your particle separation process with vibratory sieving—contact us today for expert advice!