Aluminum brazing is a specialized process used to join aluminum components by melting a filler metal without melting the base material. The most common methods include torch brazing, furnace brazing, and vacuum brazing. Torch brazing is suitable for small-scale or repair work, while furnace brazing is ideal for mass production due to its ability to uniformly heat large quantities of parts. Vacuum brazing is preferred for high-purity applications, as it eliminates the need for flux and produces clean, oxidation-free joints. The choice of brazing method depends on factors such as production volume, joint design, and the specific application requirements. Aluminum brazing typically uses aluminum-silicon alloys as filler metals, which have melting points close to the base material but lower than its solidus temperature.
Key Points Explained:
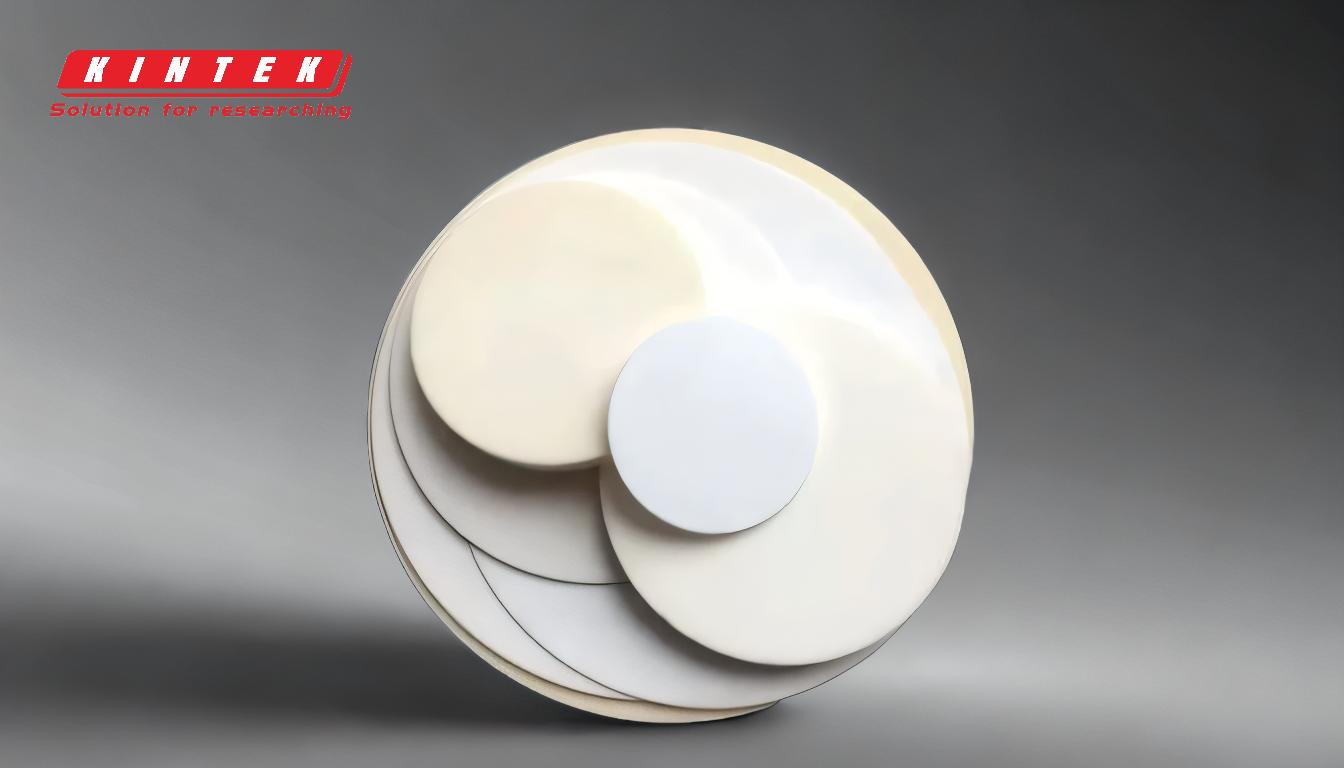
-
Torch Brazing:
- Torch brazing is a manual process where a gas torch is used to heat the joint and melt the filler metal. This method is versatile and suitable for small-scale production or repair work.
- It requires skilled operators to ensure proper heat application and avoid overheating the aluminum, which can lead to distortion or melting of the base material.
- Flux is often used to remove oxides and improve wetting of the filler metal.
-
Furnace Brazing:
- Furnace brazing is a controlled process where parts are heated in a furnace to a specific temperature, ensuring uniform heating across all components.
- This method is ideal for mass production, as it allows for the brazing of multiple parts simultaneously.
- Furnace brazing often uses a controlled atmosphere or flux to prevent oxidation and ensure strong, reliable joints.
-
Vacuum Brazing:
- Vacuum brazing is performed in a vacuum chamber, eliminating the need for flux and producing clean, oxidation-free joints.
- This method is preferred for high-purity applications, such as in the aerospace or medical industries, where contamination must be minimized.
- Vacuum brazing requires precise control of temperature and vacuum levels to achieve optimal results.
-
Filler Metals:
- Aluminum-silicon alloys are the most commonly used filler metals for aluminum brazing. These alloys have melting points close to the base material but lower than its solidus temperature, ensuring the base material remains solid during the process.
- The choice of filler metal depends on the specific application, joint design, and desired mechanical properties.
-
Flux and Atmosphere Control:
- Flux is often used in torch and furnace brazing to remove oxides and improve the wetting and flow of the filler metal.
- In furnace brazing, controlled atmospheres (e.g., nitrogen or argon) can be used to prevent oxidation and improve joint quality.
- Vacuum brazing eliminates the need for flux by performing the process in a vacuum, which prevents oxidation and contamination.
-
Application Considerations:
- The choice of brazing method depends on factors such as production volume, joint design, and the specific application requirements.
- For example, torch brazing is suitable for small-scale or repair work, while furnace brazing is ideal for mass production.
- Vacuum brazing is preferred for high-purity applications where contamination must be minimized.
By understanding these key points, equipment and consumable purchasers can make informed decisions about the appropriate brazing methods and materials for their specific needs.
Summary Table:
Brazing Method | Key Features | Best For |
---|---|---|
Torch Brazing | Manual process, versatile, uses flux | Small-scale production, repair work |
Furnace Brazing | Controlled heating, uniform, uses flux or controlled atmosphere | Mass production |
Vacuum Brazing | No flux required, clean, oxidation-free joints | High-purity applications (e.g., aerospace, medical) |
Need help choosing the right aluminum brazing method? Contact our experts today for personalized advice!