Ball milling is a versatile grinding and mixing process used across various industries to reduce materials to fine powders or to achieve uniform mixing. The materials processed in ball mills range widely, including metals, ceramics, glass, minerals, and organic compounds. The process is effective for both soft and hard materials, making it suitable for applications in fields like materials science, chemistry, and pharmaceuticals. The choice of material for ball milling depends on the desired outcome, such as particle size reduction, homogenization, or mechanical alloying.
Key Points Explained:
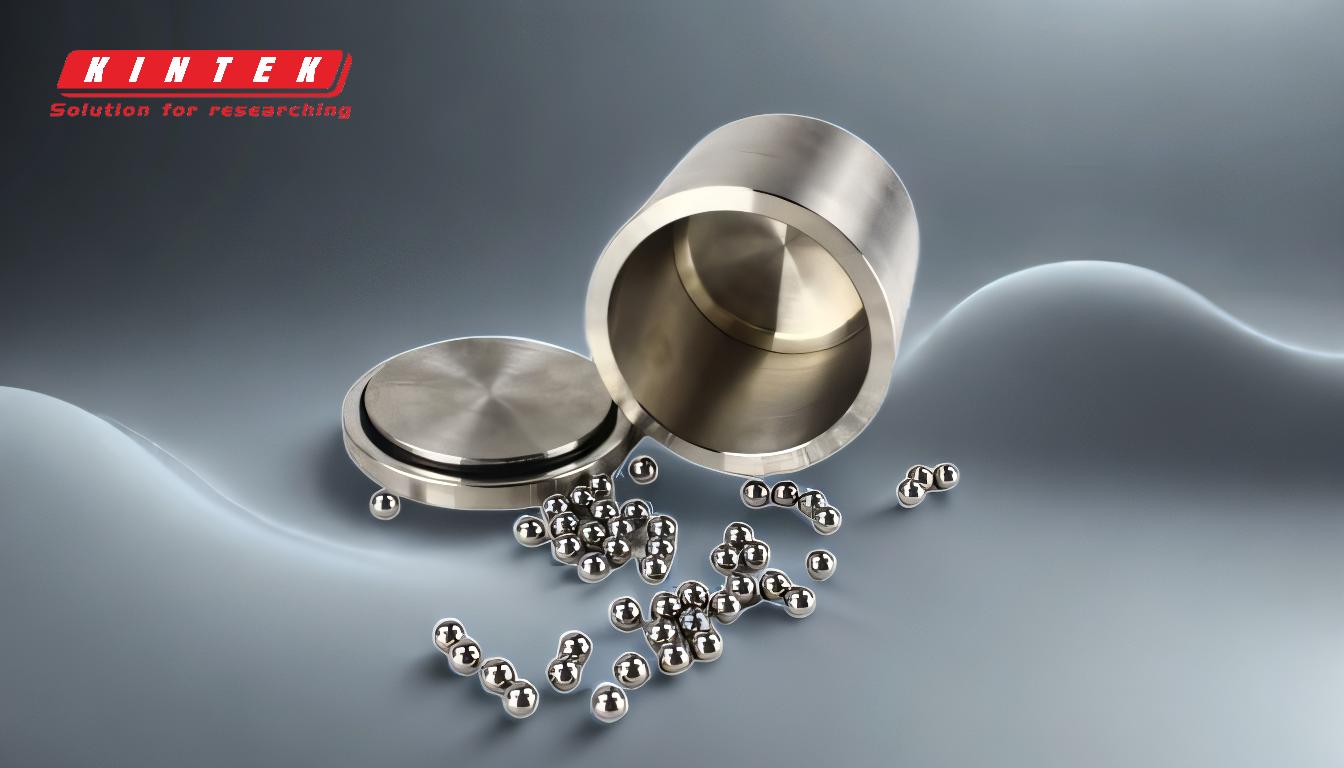
-
Types of Materials Processed in Ball Mills:
- Metals: Iron ore and other metallic materials are commonly ground in ball mills to achieve fine powders for further processing.
- Ceramics: Ball mills are ideal for grinding ceramics, which are often brittle and require fine particle sizes for applications in electronics, construction, and more.
- Glass: Glass can be ground into fine powders for use in various industrial applications, including optics and materials science.
- Minerals: Minerals are frequently processed in ball mills to reduce them to fine powders for use in industries like construction, metallurgy, and chemical processing.
- Organic and Biomedical Materials: Ball mills are used to grind organic chemical materials and biomedical substances, making them suitable for pharmaceutical and biotechnological applications.
-
Material Properties Suitable for Ball Milling:
- Soft Materials: Ball mills can effectively process soft materials, such as certain polymers and organic compounds, which require gentle grinding to avoid degradation.
- Medium-Hard Materials: Materials like ceramics and some metals fall into this category and are efficiently ground in ball mills.
- Hard and Brittle Materials: Extremely hard and brittle materials, such as certain minerals and ceramics, are well-suited for ball milling due to the high impact forces generated by the grinding balls.
- Fibrous Materials: Ball mills can also handle fibrous materials, which can be challenging to grind using other methods.
-
Applications of Ball Milling:
- Particle Size Reduction: One of the primary uses of ball mills is to reduce materials to fine powders, which are essential in industries like pharmaceuticals, cosmetics, and materials science.
- Mechanical Alloying: Ball mills are used to create alloys by grinding and mixing different metallic powders, leading to the formation of new materials with unique properties.
- Homogenization: Ball mills can achieve uniform mixing of materials, which is crucial in applications like chemical synthesis and the production of composite materials.
- Nanomaterial Synthesis: Nano ball mills are particularly useful for grinding materials to the nanoscale, which is essential for advanced applications in electronics, medicine, and energy storage.
-
Versatility of Ball Mills:
- Wide Range of Materials: Ball mills can process a diverse array of materials, from soft and elastic to hard and brittle, making them versatile tools in both research and industrial settings.
- Scalability: Ball mills are available in various sizes, from small laboratory-scale mills to large industrial mills, allowing for scalability depending on the application.
- Customization: The choice of grinding media (e.g., steel, ceramic, or zirconia balls) and the mill's operating parameters (e.g., speed, duration) can be tailored to suit specific materials and desired outcomes.
-
Considerations for Equipment and Consumable Purchasers:
- Material Compatibility: When selecting a ball mill, it is crucial to ensure that the mill is compatible with the materials to be processed, considering factors like hardness, brittleness, and chemical reactivity.
- Grinding Media Selection: The choice of grinding balls (e.g., steel, ceramic, or zirconia) should be based on the material being processed and the desired particle size.
- Mill Configuration: The configuration of the ball mill (e.g., horizontal or vertical axis) should be chosen based on the specific application and the material properties.
- Maintenance and Durability: Purchasers should consider the maintenance requirements and durability of the ball mill, especially when processing abrasive or hard materials that may cause wear on the mill components.
In summary, ball milling is a highly adaptable process capable of handling a wide range of materials, from soft and fibrous to hard and brittle. The choice of materials and equipment should be guided by the specific application, desired outcomes, and material properties, ensuring efficient and effective processing.
Summary Table:
Category | Materials | Applications |
---|---|---|
Metals | Iron ore, metallic powders | Fine powders for further processing |
Ceramics | Brittle ceramics | Electronics, construction |
Glass | Glass powders | Optics, materials science |
Minerals | Various minerals | Construction, metallurgy, chemical processing |
Organic/Biomedical | Organic compounds, biomedical substances | Pharmaceuticals, biotechnology |
Soft Materials | Polymers, organic compounds | Gentle grinding for particle size reduction |
Hard/Brittle Materials | Certain minerals, ceramics | High-impact grinding for fine powders |
Fibrous Materials | Fibrous substances | Efficient grinding for uniform mixing |
Ready to optimize your material processing? Contact our experts today to find the perfect ball mill for your needs!