PVD (Physical Vapor Deposition) coating is a versatile process used to enhance the properties of various materials, including metals, alloys, ceramics, and even some plastics. It is widely applied to improve wear resistance, corrosion resistance, and aesthetic appeal while being environmentally friendly. Materials suitable for PVD coating include steel families (especially high-alloy steels like stainless steel), non-ferrous metals (such as copper and aluminum), hard metals, and certain plastics. Common coatings include TiN, CrN, TiAlN, and diamond-like carbon (DLC). However, materials like brass without galvanization or galvanized materials are not suitable due to their incompatibility with vacuum conditions. PVD coatings are also used as a finishing layer on electroplated materials to provide additional durability and aesthetic benefits.
Key Points Explained:
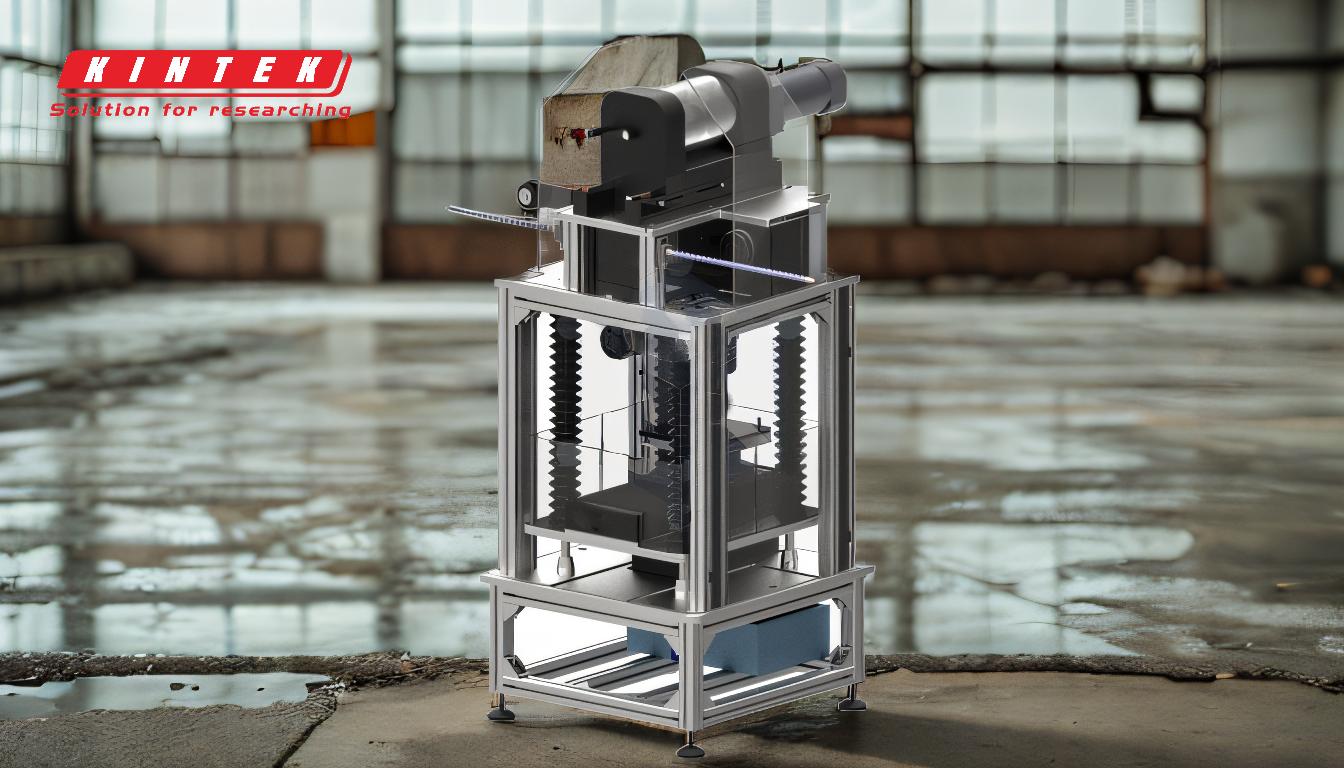
-
Materials Suitable for PVD Coating:
- Steel Families: High-alloy steels, such as high-speed steels and stainless steels, are commonly PVD-coated due to their strength and durability.
- Non-Ferrous Metals: Metals like copper, aluminum, and their alloys are also suitable for PVD coating.
- Hard Metals: These include materials like tungsten, which benefit from enhanced wear resistance and extended lifespan through PVD coatings.
- Plastics: Certain plastics, such as PVC, Nylon, ABS, and Polycarbonate, can be PVD-coated for decorative or functional purposes.
-
Common PVD Coatings:
- Metals and Alloys: Titanium nitride (TiN), chromium nitride (CrN), and titanium aluminum nitride (TiAlN) are widely used for their wear-resistant properties.
- Ceramics: Materials like Al2O3 and ZrO2 are deposited to improve hardness and thermal stability.
- Diamond-Like Carbon (DLC): DLC coatings are applied for their low friction and high wear resistance.
-
Unsuitable Materials:
- Brass without galvanization and galvanized materials are not vacuum-compatible, making them unsuitable for PVD coating.
-
Applications of PVD Coating:
- Durable-Decorative Coatings: PVD is used to enhance the appearance of products, such as watches and jewelry, while providing durability.
- Performance Coatings: These are applied to tools and components to improve wear resistance and extend service life.
- Corrosion Resistance: PVD coatings are often used as a finishing layer on electroplated materials to provide additional protection against corrosion.
-
Environmental Benefits:
- PVD coating is an eco-friendly process that produces minimal waste and has no ecological danger, making it a sustainable choice for surface enhancement.
-
Pre-Treatment Requirements:
- Substrates like glass, brass, zinc, and ABS plastic often require pre-treatment, such as organic coatings or electroplating with nickel and chromium, to ensure compatibility with the PVD process.
By understanding these key points, purchasers of equipment and consumables can make informed decisions about the suitability of PVD coatings for their specific applications.
Summary Table:
Category | Materials |
---|---|
Steel Families | High-alloy steels (e.g., stainless steel, high-speed steels) |
Non-Ferrous Metals | Copper, aluminum, and their alloys |
Hard Metals | Tungsten and similar materials |
Plastics | PVC, Nylon, ABS, Polycarbonate |
Common Coatings | TiN, CrN, TiAlN, DLC (Diamond-Like Carbon) |
Unsuitable Materials | Brass (without galvanization), galvanized materials |
Ready to enhance your materials with PVD coatings? Contact us today to learn more!