PVD (Physical Vapor Deposition) coating is a versatile technique used to enhance the properties of various materials, particularly metals. The process involves depositing a thin layer of material onto a substrate in a vacuum environment. Commonly coated metals include stainless steels (such as 303, 440C, and 17-4), titanium alloys, and tool steels. Other metals like brass, copper, and zinc can also be coated, while aluminum is typically avoided due to its low melting point. PVD coatings improve wear resistance, corrosion resistance, and overall durability, making them ideal for applications in medical devices, automotive parts, and industrial tools. The choice of substrate material significantly influences the performance of the coating.
Key Points Explained:
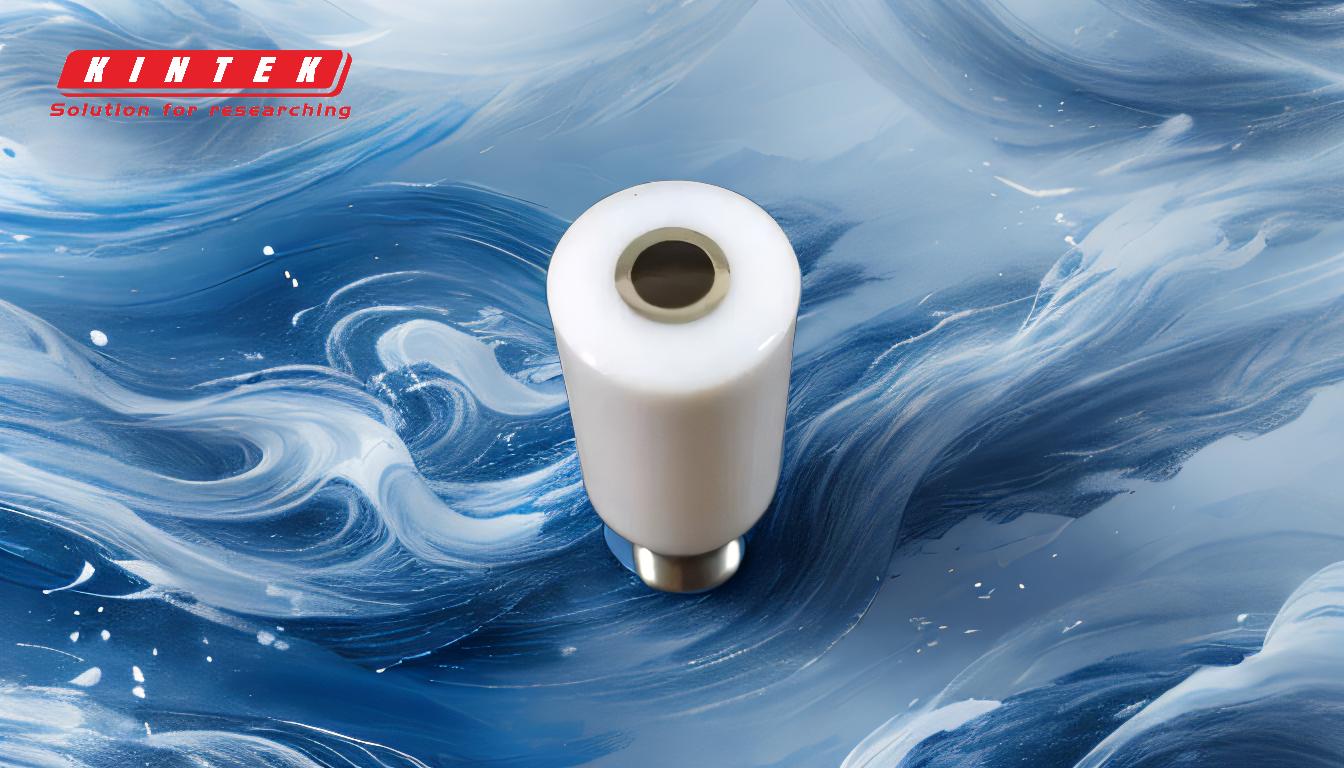
-
Vacuum-Compatible Substrates:
- PVD coating requires substrates that can withstand vacuum conditions and high temperatures (up to 800°F).
- Pre-treatment processes, such as organic coatings or electroplating with nickel and chromium, are often used to prepare substrates.
- Common materials include tool steels, stainless steels, glass, brass, zinc, and ABS plastic.
-
Common Metals for PVD Coating:
- Stainless Steels: 303, 440C, and 17-4 stainless steels are frequently used due to their strength and corrosion resistance.
- Titanium Alloys: Titanium and its alloys, such as Ti-6Al-4V, are popular for their lightweight and high strength.
- Tool Steels: These are used in high-stress applications where durability and wear resistance are critical.
- Other Metals: Brass, copper, and zinc can also be coated, though aluminum is generally avoided due to its low melting point.
-
Performance Enhancement:
- PVD coatings significantly improve the mechanical properties of the substrate. For example, a TiN coating on Ti-6Al-4V alloy increases the fatigue limit by 22% and endurance by 7%.
- The hardness of the coating is crucial for determining its durability and wear resistance.
-
Wide Range of Coatable Materials:
- Beyond metals, PVD can coat a variety of materials, including plastics (ABS, polyimide, polycarbonate), glass, and fluorocarbons (Teflon).
- This versatility makes PVD suitable for diverse industries, from medical devices to automotive components.
-
Benefits of PVD Coatings:
- Corrosion and Oxidation Resistance: PVD coatings are highly resistant to environmental degradation.
- Thin and Durable: Coatings range from 0.5 to 5 microns in thickness, making them difficult to remove and capable of replicating the original finish of materials.
- Extended Lifespan: PVD coatings can enhance a product's lifespan by up to ten times, with some applications lasting over 25 years.
-
Applications:
- Automotive: Used for coating car parts like wheels and pistons to improve durability and resistance to wear.
- Medical: Surgical tools and implants benefit from the biocompatibility and corrosion resistance of PVD coatings.
- Industrial: Drill bits and other cutting tools are coated to enhance performance and longevity.
-
Environmental Advantages:
- PVD is a greener alternative to traditional chrome plating, as it avoids the production of toxic substances.
- The process is more environmentally friendly and sustainable, aligning with modern manufacturing trends.
In summary, PVD coating is a highly effective method for enhancing the properties of various metals and other materials. Its ability to improve wear resistance, corrosion resistance, and overall durability makes it invaluable across multiple industries. The choice of substrate material and the specific application requirements play a crucial role in determining the effectiveness of the PVD coating.
Summary Table:
Key Aspect | Details |
---|---|
Common Coated Metals | Stainless steels (303, 440C, 17-4), titanium alloys, tool steels, brass, copper, zinc |
Performance Enhancements | Improves wear resistance, corrosion resistance, and mechanical properties |
Coating Thickness | 0.5 to 5 microns, thin yet durable |
Applications | Automotive, medical devices, industrial tools |
Environmental Benefits | Greener alternative to chrome plating, no toxic substances produced |
Transform your materials with PVD coating—contact us today to learn more!