The size of material that a ball mill can crush typically depends on the design and capacity of the mill. Generally, ball mills are designed to handle feed sizes of less than 20mm, which is ideal for efficient grinding. However, larger ball mills can accommodate feed sizes of up to 50mm, though this is less common. The choice of feed size is influenced by the mill's operational parameters, such as the diameter and length of the mill, the speed of rotation, and the type of grinding media used. Understanding these factors is crucial for optimizing the crushing and grinding process in a ball mill.
Key Points Explained:
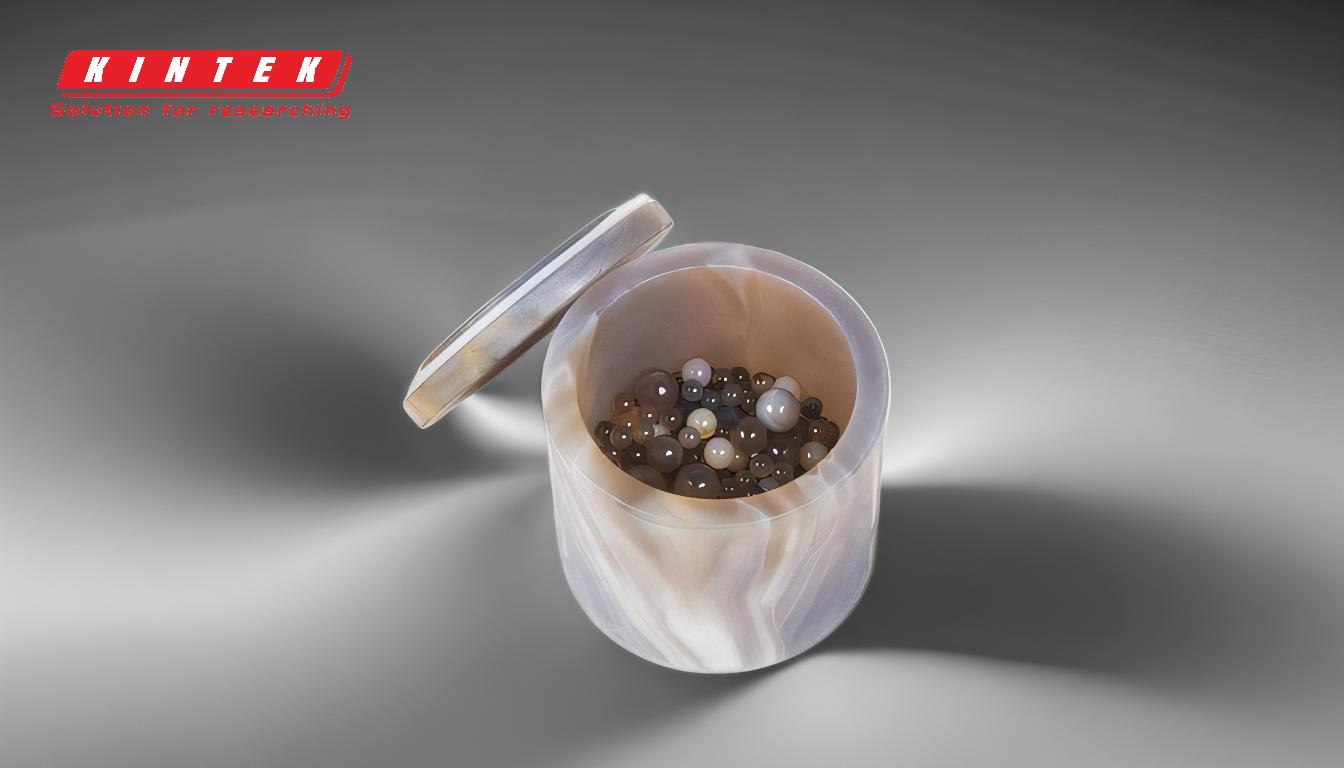
-
Typical Feed Size for Ball Mills:
- Less than 20mm: Most ball mills are designed to handle feed sizes of less than 20mm. This size is optimal for efficient grinding as it allows for better contact between the grinding media and the material, leading to more effective size reduction.
- Larger Feed Sizes (up to 50mm): Some larger ball mills can accommodate feed sizes of up to 50mm. However, this is less common and typically requires a mill with a larger diameter and length to handle the increased size of the feed material.
-
Factors Influencing Feed Size:
- Mill Design: The design of the ball mill, including its diameter and length, plays a significant role in determining the maximum feed size it can handle. Larger mills with greater dimensions can typically process larger feed sizes.
- Rotation Speed: The speed at which the mill rotates affects the grinding efficiency. Higher speeds can lead to more effective grinding, but they also require careful consideration of the feed size to avoid inefficiencies.
- Grinding Media: The type and size of the grinding media used in the mill also influence the feed size. Larger media can handle larger feed sizes, but they may also lead to coarser grinding if not properly matched to the feed material.
-
Operational Considerations:
- Efficiency: Smaller feed sizes generally lead to more efficient grinding, as the material is more uniformly ground and there is less chance of over-grinding or under-grinding.
- Energy Consumption: Larger feed sizes may require more energy to achieve the desired level of grinding, which can impact the overall energy efficiency of the milling process.
- Wear and Tear: Larger feed sizes can lead to increased wear and tear on the mill and grinding media, which may necessitate more frequent maintenance and replacement of parts.
-
Optimization of Crushing and Grinding:
- Feed Size Selection: Selecting the appropriate feed size is crucial for optimizing the crushing and grinding process. It involves balancing the need for efficient size reduction with the operational constraints of the mill.
- Process Control: Proper control of the milling process, including monitoring the feed size and adjusting operational parameters as needed, can help achieve the desired grinding outcomes while minimizing energy consumption and wear on the mill.
In summary, while ball mills typically handle feed sizes of less than 20mm, larger mills can accommodate feed sizes of up to 50mm. The choice of feed size is influenced by various factors, including mill design, rotation speed, and grinding media, and careful consideration of these factors is essential for optimizing the crushing and grinding process.
Summary Table:
Aspect | Details |
---|---|
Typical Feed Size | Less than 20mm for most ball mills, up to 50mm for larger mills. |
Factors Influencing | Mill design, rotation speed, and grinding media type and size. |
Operational Impact | Smaller sizes improve efficiency; larger sizes increase energy use and wear. |
Optimization | Balance feed size with mill parameters for effective grinding. |
Need help optimizing your ball mill's performance? Contact our experts today for tailored solutions!