Compression molding is a widely used manufacturing process for producing high-quality parts, especially in industries like automotive, aerospace, and consumer goods. The type of mold used plays a critical role in determining the quality of the final product. Flash molds are the most commonly used due to their simplicity and cost-effectiveness, but other types like positive, landed positive, and semi-positive molds are also employed depending on the specific requirements of the part being produced. Each mold type has its advantages and limitations, and the choice depends on factors such as material properties, part complexity, and desired tolerances. Understanding the nuances of each mold type and their suitability for different applications is essential for achieving consistent quality in compression-molded parts.
Key Points Explained:
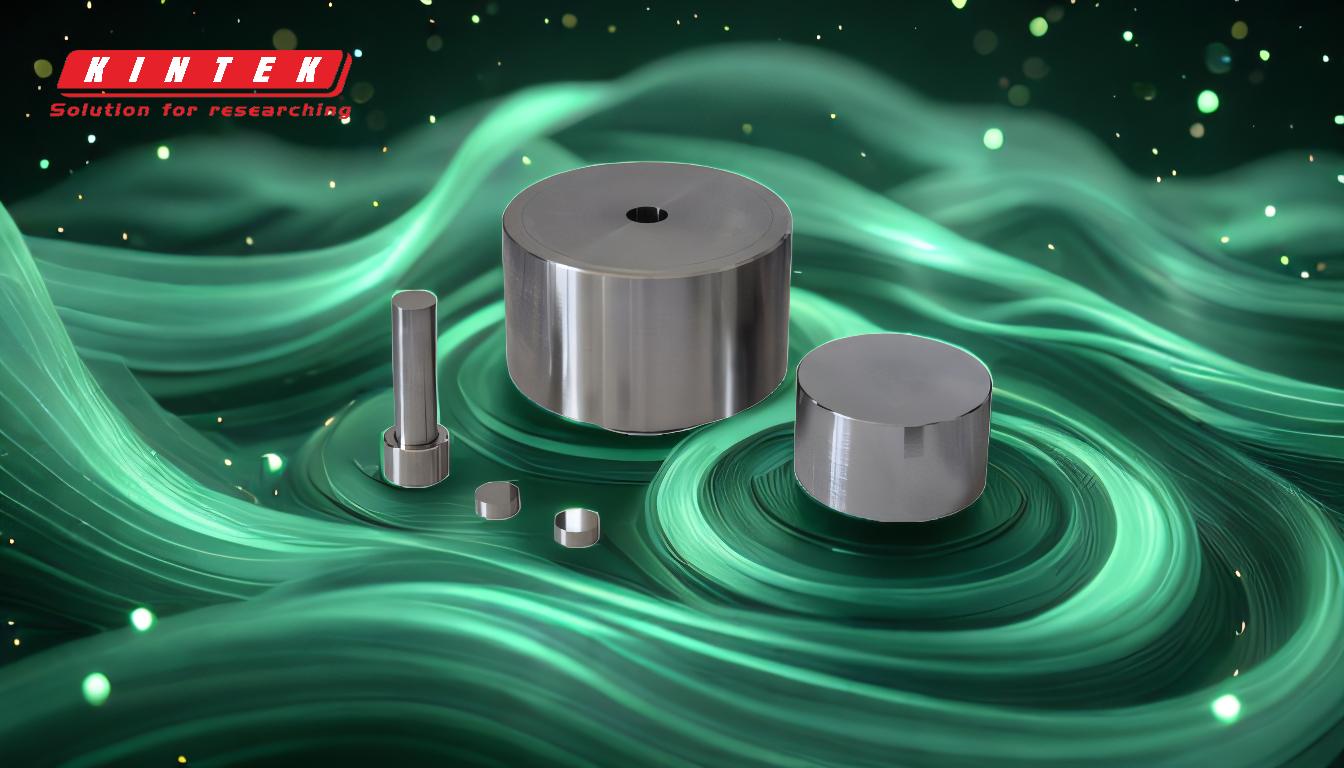
-
Types of Compression Molds:
-
Flash Mold:
- The most commonly used mold type due to its simplicity and cost-effectiveness.
- Features a small overflow area (flash) that allows excess material to escape, ensuring proper filling of the cavity.
- Suitable for parts with less stringent dimensional requirements.
-
Positive Mold:
- Designed to contain all the material within the cavity, with no overflow.
- Ideal for producing parts with tight tolerances and minimal flash.
- Requires precise material measurement to avoid defects.
-
Landed Positive Mold:
- A hybrid between flash and positive molds.
- Includes a small land area to control flash while maintaining tight tolerances.
- Suitable for parts requiring both precision and minimal waste.
-
Semi-Positive Mold:
- Combines features of flash and positive molds.
- Allows for some overflow while maintaining better control over material distribution.
- Used for parts with moderate tolerances and where material waste needs to be minimized.
-
Flash Mold:
-
Material Considerations:
-
Bulk Molding:
- Involves a mixture of fillers, catalysts, stabilizers, pigments, and fiber reinforcers.
- Suitable for producing parts with enhanced mechanical properties.
-
Sheet Molding:
- Uses pre-cut sheets of material, which are placed into the mold cavity.
- Ideal for parts requiring uniform thickness and consistent material distribution.
-
Bulk Molding:
-
Challenges in Compression Molding:
-
Material Measurement:
- Accurately cutting or weighing the rubber stock is crucial.
- Insufficient material can lead to defects like flow lines, blisters, or unfilled parts.
-
Material Placement:
- Incorrect placement can cause uneven material distribution, leading to defects.
-
Excessive Material:
- Too much material can result in heavy flash, which is difficult to remove and can affect the part's appearance and functionality.
-
Material Measurement:
-
Choosing the Right Mold Type:
-
Part Complexity:
- Complex parts with intricate details may require positive or landed positive molds to ensure precise material distribution.
-
Tolerance Requirements:
- Parts with tight tolerances are best produced using positive or landed positive molds.
-
Material Properties:
- The type of material used (bulk or sheet) can influence the choice of mold type.
-
Production Volume:
- High-volume production may favor flash molds due to their simplicity and lower cost.
-
Part Complexity:
-
Quality Control:
-
Defect Prevention:
- Proper material measurement and placement are critical to avoiding defects.
-
Flash Management:
- Managing flash is essential for maintaining part quality and reducing post-processing efforts.
-
Consistency:
- Consistent material distribution and mold design are key to producing high-quality parts.
-
Defect Prevention:
By understanding the different types of compression molds and their respective advantages and challenges, manufacturers can make informed decisions to produce high-quality parts efficiently. The choice of mold type should be based on the specific requirements of the part, including its complexity, tolerance requirements, and material properties. Proper material handling and mold design are essential to achieving consistent quality in compression-molded parts.
Summary Table:
Mold Type | Key Features | Best Use Cases |
---|---|---|
Flash Mold | Simple, cost-effective, small overflow area for excess material | Parts with less stringent dimensional requirements |
Positive Mold | No overflow, precise material measurement required | Parts with tight tolerances and minimal flash |
Landed Positive | Hybrid design, small land area to control flash | Parts requiring precision and minimal waste |
Semi-Positive | Combines flash and positive features, allows some overflow | Parts with moderate tolerances and minimized material waste |
Material Type | Bulk Molding: Enhanced mechanical properties; Sheet Molding: Uniform thickness | Choose based on part requirements and material properties |
Need help selecting the right mold for your compression molding process? Contact our experts today for tailored solutions!