Pyrolysis reactors are essential for the thermal decomposition of organic materials in the absence of oxygen, producing gases, liquids, and solids. The choice of reactor depends on factors like heat transfer efficiency, residence time, feedstock type, and desired products. Common types include fluidized bed reactors, fixed bed reactors, and ablative reactors, each with unique characteristics suited for specific pyrolysis processes such as fast, slow, or intermediate pyrolysis. Understanding the differences between these reactors helps in selecting the most appropriate one for a given application.
Key Points Explained:
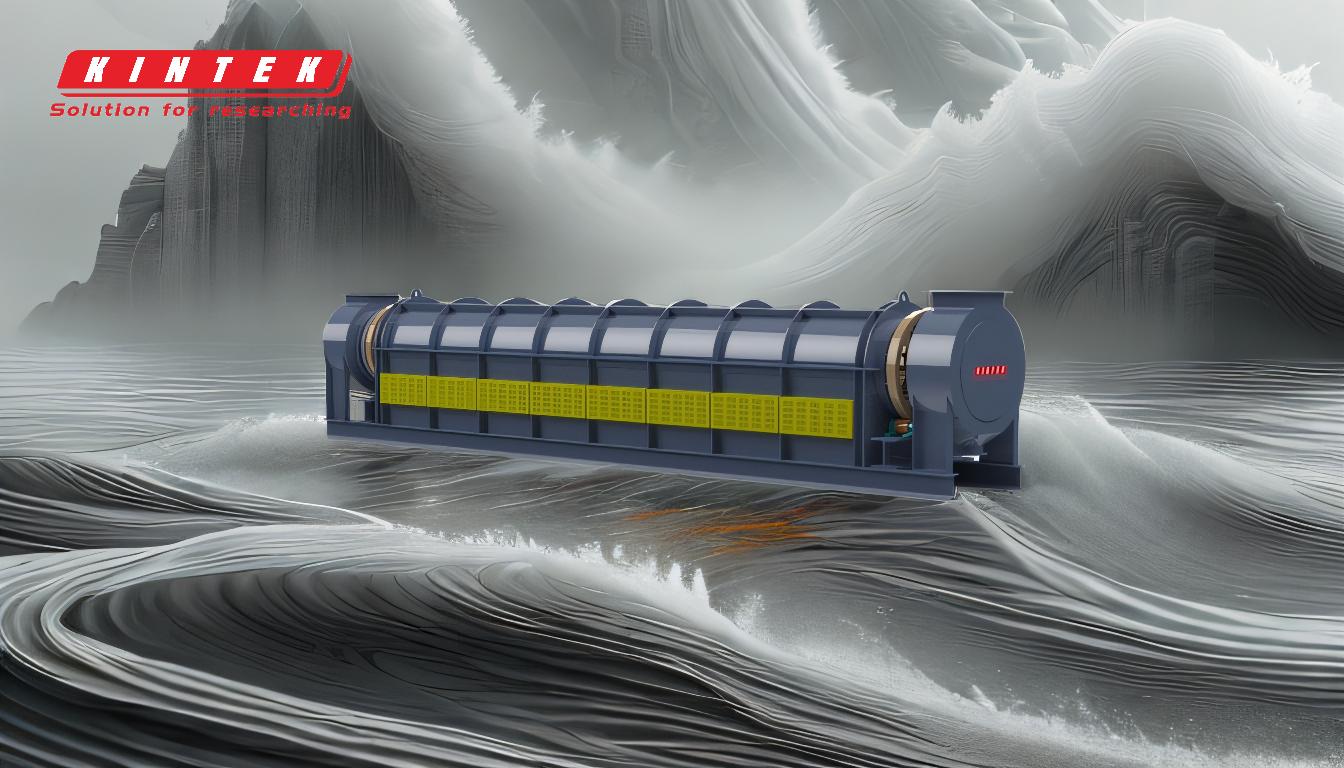
-
Types of Pyrolysis Reactors:
- Fluidized Bed Reactors: These reactors use a bed material like sand to enhance heat transfer and maintain an inert atmosphere. The fluidizing gas, often nitrogen, ensures efficient heat distribution and prevents unwanted reactions. They are ideal for fast pyrolysis due to their high heat transfer rates and short residence times.
- Fixed Bed Reactors: These reactors are simpler in design and are typically used for slow pyrolysis. They operate at lower temperatures and longer residence times, making them suitable for producing biochar.
- Ablative Reactors: In these reactors, the feedstock is pressed against a heated surface, causing rapid pyrolysis. They are efficient for handling large particles and are often used in fast pyrolysis processes.
- Cyclone Reactors: These reactors use centrifugal force to separate particles and gases, making them suitable for processes requiring rapid separation of pyrolysis products.
-
Heat Sources for Pyrolysis:
- Conventional Heat Sources: These include electric heaters, gas burners, or other external heat sources that provide the necessary energy for pyrolysis.
- Microwave Energy: Microwave pyrolysis is an emerging technology that offers uniform heating and can be more energy-efficient for certain feedstocks.
-
Pyrolysis Processes:
- Fast Pyrolysis: Involves rapid heating (400-700°C) to produce bio-oil. Fluidized bed reactors are commonly used due to their high heat transfer rates.
- Slow Pyrolysis: Operates at lower temperatures (300-400°C) with longer residence times, producing biochar. Fixed bed reactors are typically used for this process.
- Torrefaction: A mild form of pyrolysis (250-350°C) that improves the fuel characteristics of biomass. It is often carried out in fixed bed or fluidized bed reactors.
-
Advantages of Different Reactor Types:
- Fluidized Bed Reactors: High heat transfer efficiency, short residence times, and ability to handle a wide range of feedstocks.
- Fixed Bed Reactors: Simplicity, lower operational costs, and suitability for slow pyrolysis.
- Ablative Reactors: Efficient for large particles and rapid pyrolysis processes.
- Cyclone Reactors: Effective for rapid separation of gases and solids.
-
Considerations for Reactor Selection:
- Feedstock Type: The size, moisture content, and composition of the feedstock influence the choice of reactor.
- Desired Products: The type of pyrolysis (fast, slow, or intermediate) and the desired end products (bio-oil, biochar, or gases) determine the most suitable reactor.
- Operational Parameters: Temperature, residence time, and heat transfer efficiency are critical factors in reactor selection.
For more detailed information on pyrolysis reactors, you can refer to the pyrolysis reactor topic.
Summary Table:
Reactor Type | Key Features | Best For |
---|---|---|
Fluidized Bed | High heat transfer, short residence times, inert atmosphere | Fast pyrolysis, bio-oil production |
Fixed Bed | Simple design, lower operational costs, longer residence times | Slow pyrolysis, biochar production |
Ablative | Efficient for large particles, rapid pyrolysis | Fast pyrolysis, large feedstock |
Cyclone | Rapid separation of gases and solids | Processes requiring quick separation |
Need help selecting the right pyrolysis reactor? Contact our experts today for tailored solutions!