The most commonly used frequency for RF sputter deposition is 13.56 MHz. This frequency is widely adopted in industrial, scientific, and medical (ISM) applications due to its allocation by the International Telecommunication Union (ITU) for such purposes. It ensures minimal interference with telecommunication services while providing an optimal balance between effective sputtering of non-conductive materials and efficient momentum transfer of argon ions to the target. The frequency is high enough to enable electrical discharge of insulating targets, making it suitable for sputtering dielectric materials, yet low enough to allow effective ion bombardment and material deposition.
Key Points Explained:
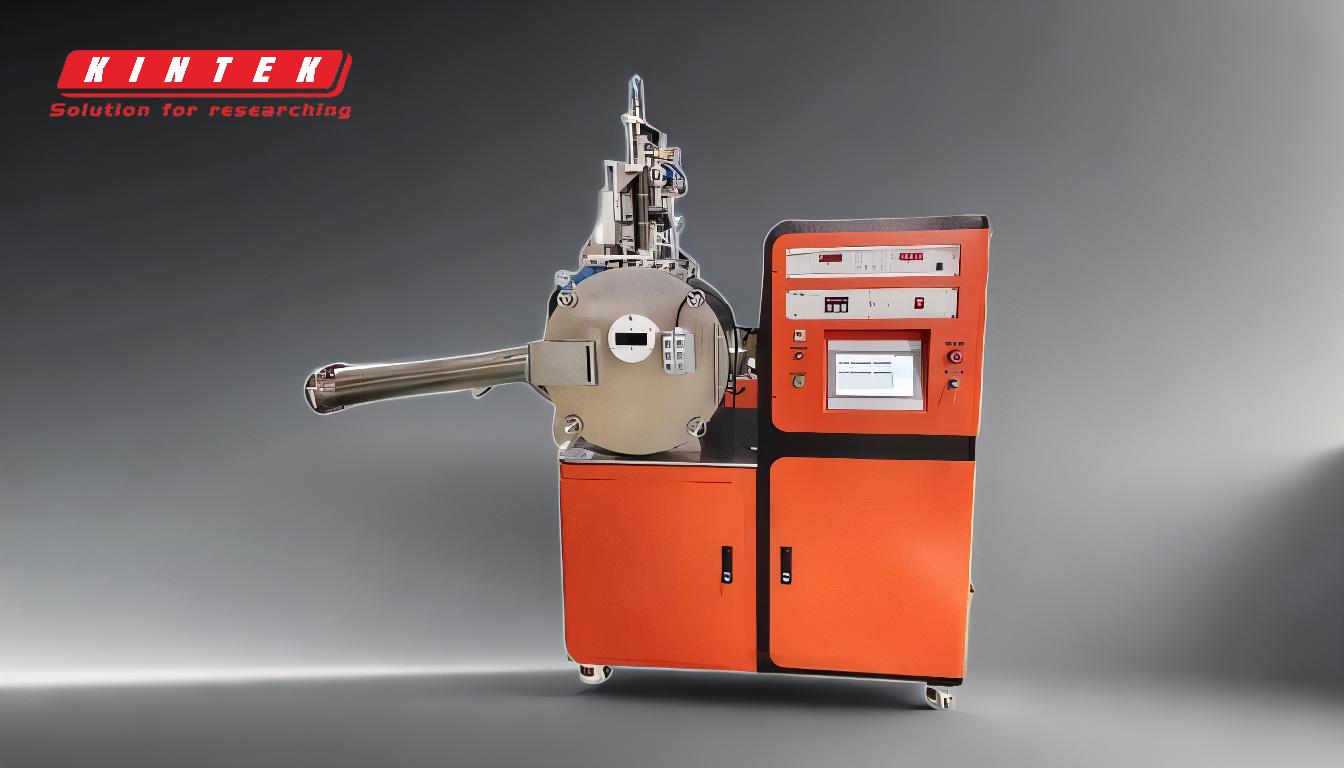
-
13.56 MHz as the Standard Frequency:
- Reason for Adoption: 13.56 MHz is the frequency allocated by the ITU Radio Regulations for industrial, scientific, and medical (ISM) applications. This allocation ensures that RF sputtering equipment does not interfere with telecommunication services.
- Widespread Use: Due to its standardization, 13.56 MHz has become the most common frequency used in RF sputtering systems globally.
-
Technical Suitability for RF Sputtering:
- High Enough for Electrical Discharge: A frequency of 1 MHz or higher is required to enable the electrical discharge of insulating targets. At 13.56 MHz, the alternating current applied to the target behaves as if it is passing through a series of capacitors, allowing the sputtering of non-conductive materials.
- Low Enough for Momentum Transfer: The frequency is low enough to provide sufficient time for argon ions to transfer momentum to the target material, ensuring effective sputtering and deposition.
-
Advantages of 13.56 MHz:
- Interference-Free Operation: Being an ISM frequency, 13.56 MHz avoids conflicts with other communication systems, making it ideal for industrial and scientific applications.
- Versatility: This frequency is suitable for sputtering both conductive and non-conductive materials, making it a versatile choice for various thin-film deposition processes.
- Efficiency: The balance between frequency and ion momentum transfer ensures high deposition rates and quality thin films.
-
Comparison with Other Frequencies:
- Lower Frequencies (<1 MHz): These are insufficient for sputtering insulating materials due to inadequate electrical discharge capabilities.
- Higher Frequencies (>13.56 MHz): While they may enable faster sputtering, they can reduce the efficiency of ion momentum transfer, leading to lower deposition rates and potentially compromising film quality.
-
Practical Implications for Equipment Purchasers:
- Compatibility: When purchasing RF sputtering equipment, ensuring it operates at 13.56 MHz guarantees compatibility with industry standards and other equipment.
- Process Optimization: Equipment operating at this frequency is optimized for both conductive and non-conductive materials, providing flexibility for diverse applications.
- Regulatory Compliance: Using 13.56 MHz ensures adherence to ITU regulations, avoiding legal or operational issues related to frequency interference.
In summary, 13.56 MHz is the optimal frequency for RF sputter deposition due to its technical suitability, regulatory compliance, and widespread adoption in the industry. It strikes a balance between enabling effective sputtering of insulating materials and ensuring efficient momentum transfer for high-quality thin-film deposition.
Summary Table:
Key Aspect | Details |
---|---|
Standard Frequency | 13.56 MHz, allocated by ITU for ISM applications. |
Technical Suitability | Enables electrical discharge of insulating targets and efficient sputtering. |
Advantages | Interference-free, versatile, and efficient for thin-film deposition. |
Comparison with Others | Lower frequencies (<1 MHz) insufficient; higher frequencies (>13.56 MHz) less efficient. |
Practical Implications | Ensures compatibility, process optimization, and regulatory compliance. |
Ready to optimize your RF sputter deposition process? Contact us today to learn more about 13.56 MHz equipment!