The choice between a roller mill and a hammer mill depends on the specific application, the material being processed, and the desired output. Roller mills are generally better for producing uniform particle sizes and are more energy-efficient for fine grinding, making them ideal for industries like flour milling and feed production. Hammer mills, on the other hand, are more versatile and better suited for coarse grinding, crushing, and pulverizing a wide range of materials, including fibrous and tough substances. They are commonly used in industries like agriculture, biomass processing, and recycling. The decision ultimately hinges on factors such as material characteristics, desired particle size, energy efficiency, and maintenance requirements.
Key Points Explained:
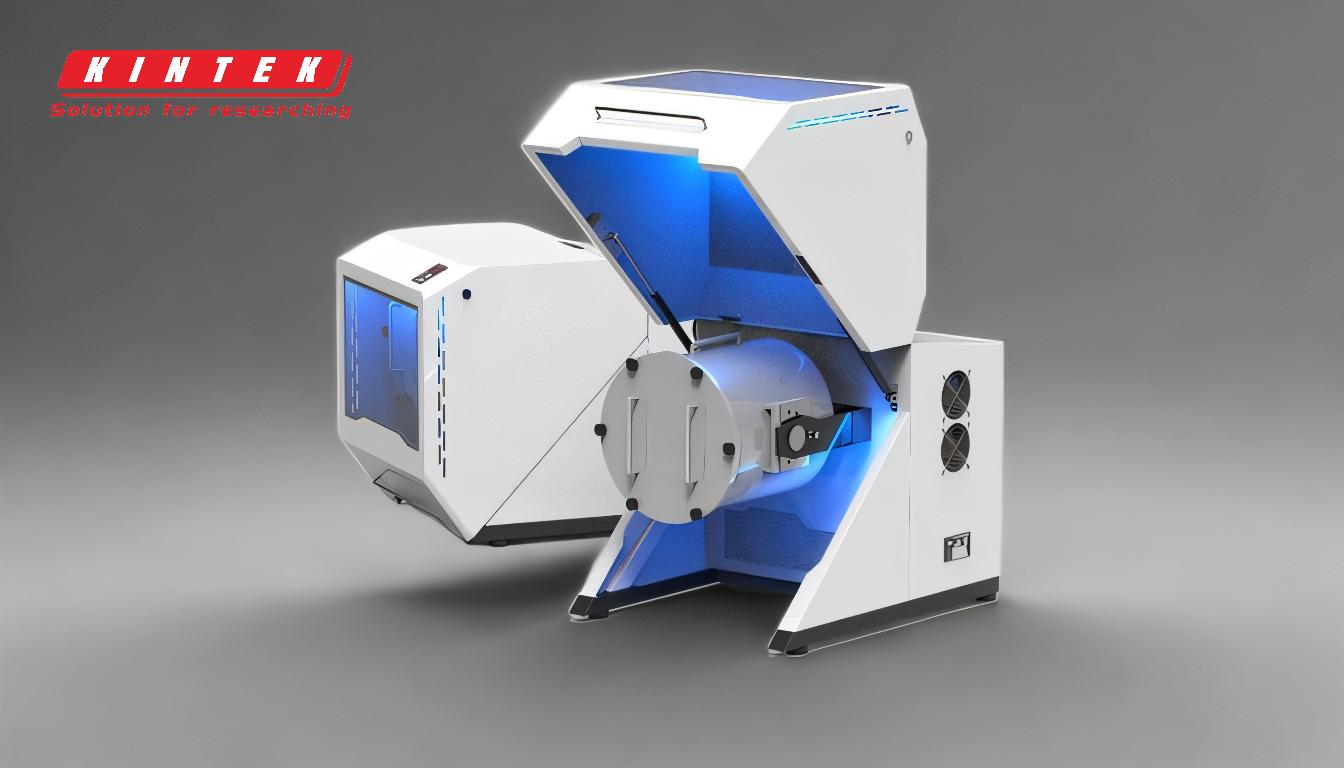
-
Mechanism of Operation:
- Roller Mill: Uses cylindrical rollers to crush and grind materials. The rollers rotate at different speeds, creating a shearing action that results in uniform particle size reduction. This method is gentle and minimizes heat generation, preserving the quality of heat-sensitive materials.
- Hammer Mill: Relies on high-speed rotating hammers to impact and shatter materials. The hammers strike the material repeatedly until it is reduced to the desired size. This method is more aggressive and can handle tougher and fibrous materials.
-
Particle Size and Uniformity:
- Roller Mill: Produces a more consistent and uniform particle size distribution, making it ideal for applications requiring precise control over particle size, such as flour milling or feed production.
- Hammer Mill: Tends to produce a wider range of particle sizes, including fines and larger particles. This can be advantageous for applications where a variety of particle sizes is acceptable or desired, such as in biomass processing or recycling.
-
Energy Efficiency:
- Roller Mill: Generally more energy-efficient, especially for fine grinding applications. The gradual reduction process requires less energy compared to the high-impact method of hammer mills.
- Hammer Mill: Can be less energy-efficient due to the high-speed impact forces required to break down materials. However, it is more efficient for coarse grinding and can handle a wider variety of materials.
-
Material Suitability:
- Roller Mill: Best suited for brittle, friable, and heat-sensitive materials. It is less effective for fibrous or tough materials, which can cause wear and tear on the rollers.
- Hammer Mill: Versatile and capable of processing a wide range of materials, including fibrous, tough, and wet substances. It is particularly effective for materials that are difficult to grind using other methods.
-
Maintenance and Wear:
- Roller Mill: Typically requires less maintenance due to the lower wear and tear on the rollers. However, the rollers may need to be replaced or reground periodically to maintain optimal performance.
- Hammer Mill: Requires more frequent maintenance due to the high-impact nature of the hammers, which can wear out quickly, especially when processing abrasive materials. Regular replacement of hammers and screens is necessary.
-
Applications:
- Roller Mill: Commonly used in the flour milling industry, feed production, and other applications requiring fine and uniform particle sizes. It is also used in the pharmaceutical and chemical industries for grinding heat-sensitive materials.
- Hammer Mill: Widely used in agriculture for grinding grains and other crops, in biomass processing for reducing the size of wood chips and other plant materials, and in recycling for crushing and pulverizing various waste materials.
-
Cost Considerations:
- Roller Mill: Generally has a higher initial cost but lower operating costs due to its energy efficiency and lower maintenance requirements.
- Hammer Mill: Typically has a lower initial cost but higher operating costs due to higher energy consumption and more frequent maintenance needs.
In conclusion, the choice between a roller mill and a hammer mill depends on the specific requirements of the application. If uniform particle size and energy efficiency are priorities, a roller mill may be the better choice. If versatility and the ability to handle a wide range of materials are more important, a hammer mill may be more suitable.
Summary Table:
Feature | Roller Mill | Hammer Mill |
---|---|---|
Mechanism | Uses cylindrical rollers for gentle, uniform grinding | Relies on high-speed hammers for aggressive impact grinding |
Particle Size | Produces uniform particle sizes, ideal for fine grinding | Produces a wider range of particle sizes, suitable for coarse grinding |
Energy Efficiency | More energy-efficient for fine grinding | Less energy-efficient but better for coarse grinding |
Material Suitability | Best for brittle, friable, and heat-sensitive materials | Versatile; handles fibrous, tough, and wet materials |
Maintenance | Lower maintenance; rollers may need periodic replacement or regrinding | Higher maintenance; hammers and screens require regular replacement |
Applications | Flour milling, feed production, pharmaceuticals, and chemicals | Agriculture, biomass processing, recycling |
Cost | Higher initial cost but lower operating costs | Lower initial cost but higher operating costs |
Still unsure which mill is right for your application? Contact our experts today for personalized advice!