The most preferred material for manufacturing semiconductors is silicon. Silicon is widely used due to its excellent semiconductor properties, abundance, and cost-effectiveness. It forms a stable oxide layer, which is crucial for creating insulating layers in semiconductor devices. Additionally, silicon's bandgap is ideal for electronic applications, making it the backbone of the semiconductor industry. While other materials like gallium arsenide and silicon carbide are used for specialized applications, silicon remains the dominant choice for most semiconductor manufacturing processes.
Key Points Explained:
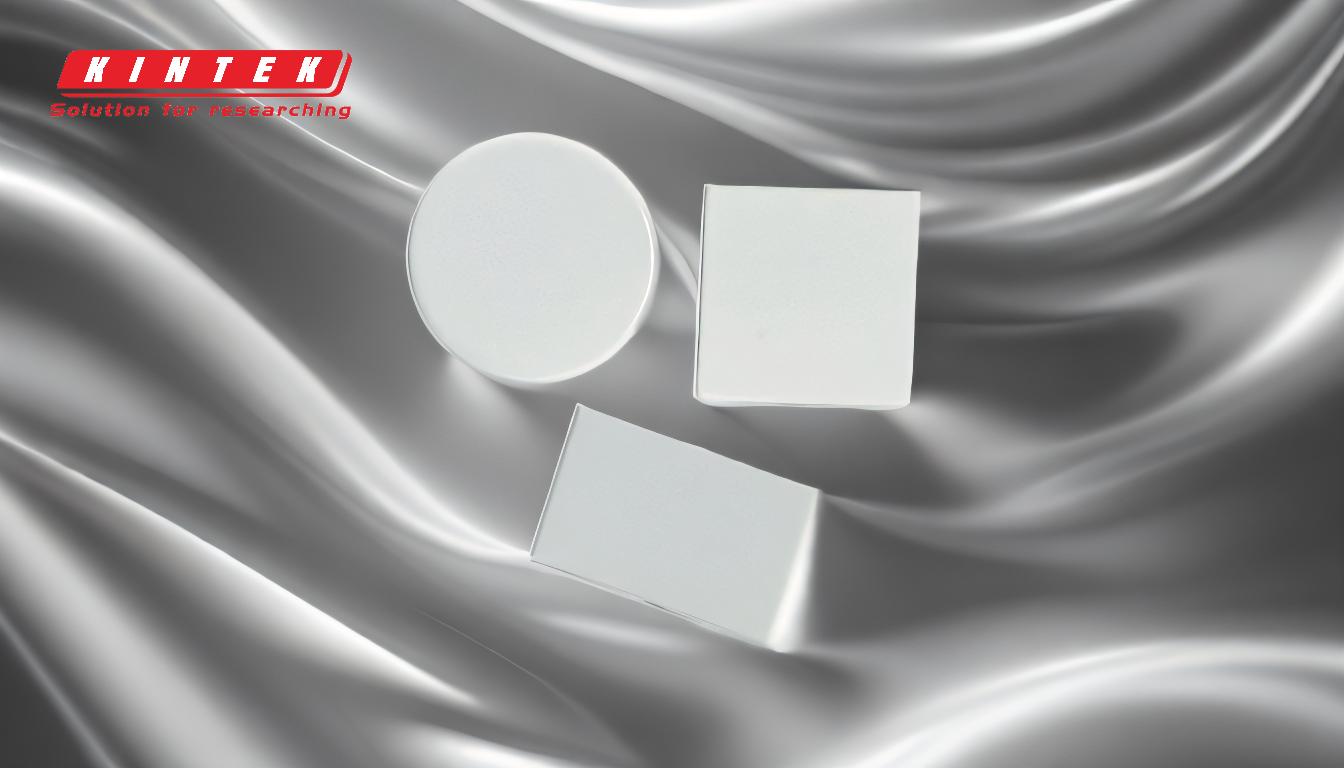
-
Silicon's Semiconductor Properties:
- Silicon has a bandgap of 1.1 eV, which is ideal for electronic devices. This bandgap allows silicon to efficiently conduct electricity under certain conditions while acting as an insulator under others.
- It forms a stable oxide layer (SiO₂), which is essential for creating insulating layers in transistors and other semiconductor devices. This oxide layer is crucial for the fabrication of MOSFETs (Metal-Oxide-Semiconductor Field-Effect Transistors), which are the building blocks of modern electronics.
-
Abundance and Cost-Effectiveness:
- Silicon is the second most abundant element in the Earth's crust, making it readily available and inexpensive compared to other semiconductor materials.
- The cost-effectiveness of silicon is a significant factor in its widespread use, as it allows for the mass production of affordable electronic devices.
-
Manufacturing Process:
- Silicon wafers are produced through a highly refined process that involves growing single-crystal silicon ingots using the Czochralski process. These ingots are then sliced into thin wafers, which serve as the substrate for semiconductor devices.
- The well-established manufacturing processes for silicon-based devices contribute to its dominance in the industry.
-
Comparison with Other Materials:
- Gallium Arsenide (GaAs): GaAs has a higher electron mobility than silicon, making it suitable for high-frequency applications such as RF (radio frequency) devices. However, it is more expensive and less abundant than silicon.
- Silicon Carbide (SiC): SiC is used in high-power and high-temperature applications due to its wide bandgap and thermal conductivity. However, it is more challenging to manufacture and more costly than silicon.
- Despite the advantages of these materials in specific applications, silicon remains the preferred choice for most semiconductor manufacturing due to its overall balance of properties, cost, and availability.
-
Future Trends:
- While silicon continues to dominate, research is ongoing into alternative materials like graphene and carbon nanotubes, which offer potential advantages in terms of speed and efficiency. However, these materials are still in the experimental stage and face significant challenges in terms of scalability and integration into existing manufacturing processes.
- The semiconductor industry is also exploring the use of silicon in combination with other materials (e.g., silicon-germanium alloys) to enhance performance in specific applications.
In summary, silicon is the most preferred material for semiconductor manufacturing due to its ideal semiconductor properties, abundance, cost-effectiveness, and well-established manufacturing processes. While other materials offer advantages in specialized applications, silicon's overall balance of properties ensures its continued dominance in the industry.
Summary Table:
Key Aspect | Details |
---|---|
Semiconductor Properties | Bandgap of 1.1 eV, stable oxide layer (SiO₂) for insulating layers. |
Abundance & Cost | Second most abundant element, cost-effective for mass production. |
Manufacturing Process | Czochralski process for single-crystal silicon ingots, sliced into wafers. |
Comparison with GaAs & SiC | GaAs for high-frequency, SiC for high-power; silicon remains dominant. |
Future Trends | Research on graphene, carbon nanotubes, and silicon-germanium alloys. |
Learn more about semiconductor materials and how silicon can meet your needs—contact us today!