PVD (Physical Vapor Deposition) coating is a versatile and widely used technique to enhance the properties of various materials, particularly metals. It involves depositing thin films of material onto a substrate in a vacuum environment. PVD coatings are known for improving durability, wear resistance, and aesthetic appeal. Commonly coated metals include stainless steel, titanium, copper, brass, and aluminum, among others. However, the suitability of a metal for PVD coating depends on its ability to withstand vacuum conditions and high temperatures. Pre-treatments like electroplating or organic coatings are often used to make substrates vacuum-compatible. PVD coatings are applied in industries ranging from automotive to medical, offering a greener alternative to traditional plating methods.
Key Points Explained:
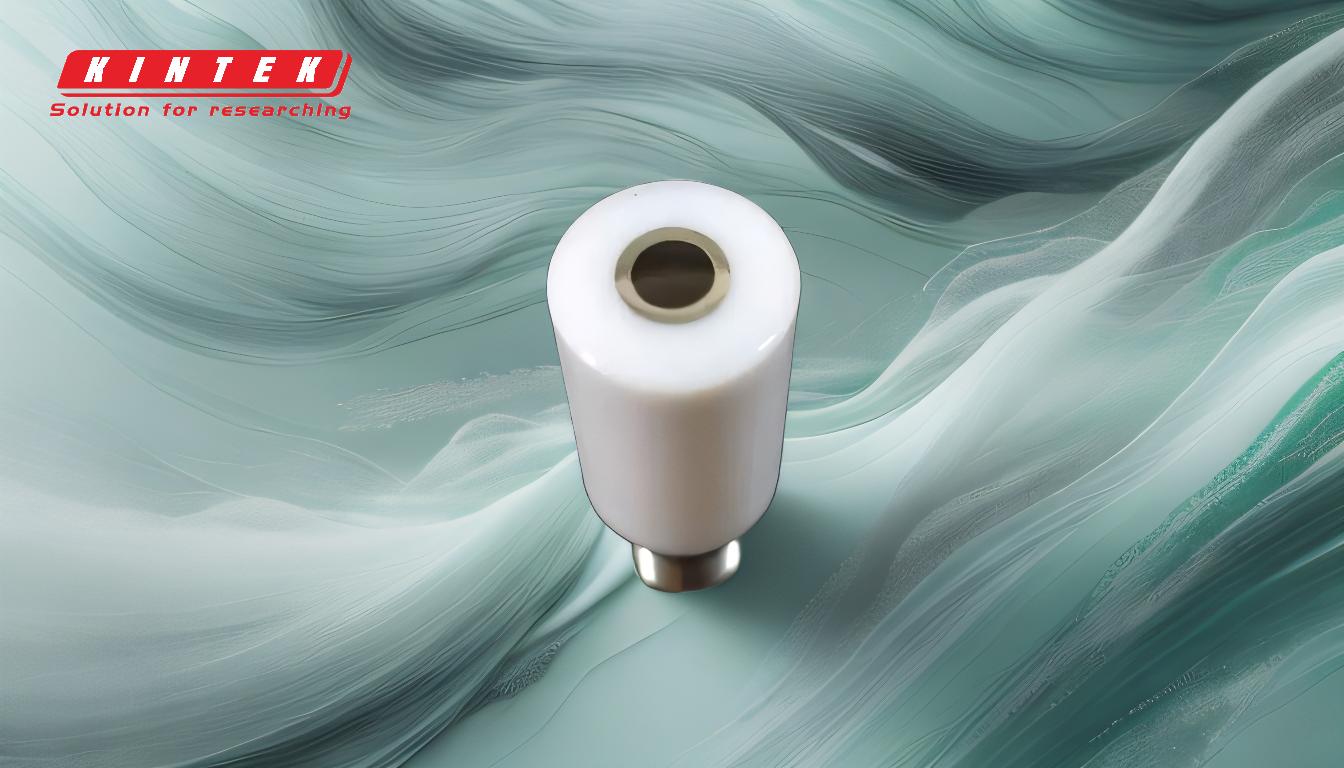
-
Common Metals Suitable for PVD Coating
- Stainless Steel: Widely used due to its strength and durability. Common grades include 303, 440C, and 17-4 stainless steels.
- Titanium: Known for its lightweight and corrosion resistance, titanium is a popular choice for medical and aerospace applications.
- Copper and Brass: Often coated for decorative purposes or to enhance conductivity.
- Aluminum: While less common due to its low melting point, aluminum can be coated with proper pre-treatment.
- Tungsten: Used in high-wear applications due to its hardness and durability.
- Zinc: Commonly coated for decorative or protective purposes, especially in automotive parts.
-
Pre-Treatment Requirements
- Vacuum Compatibility: The substrate must be able to withstand vacuum conditions. Materials like brass or galvanized metals may require pre-treatment (e.g., electroplating with nickel or chromium) to make them suitable.
- Temperature Tolerance: Metals must withstand temperatures up to 800°F (427°C) during the PVD process.
-
Exclusions and Limitations
- Brass Without Galvanization: Unsuitable due to its vacuum-unfriendly nature.
- Galvanized Materials: Typically not used unless pre-treated.
- Low-Melting-Point Metals: Aluminum and similar metals require careful handling to avoid deformation.
-
Applications of PVD-Coated Metals
- Automotive Industry: Used for coating wheels, pistons, and other parts to enhance durability and aesthetics.
- Medical Tools: Surgical instruments and implants benefit from PVD coatings for improved wear resistance and biocompatibility.
- Industrial Tools: Drill bits, cutting tools, and molds are coated to extend their lifespan.
- Decorative Uses: Jewelry, watches, and household items are coated for a metallic finish.
-
Advantages of PVD Coating
- Enhanced Durability: PVD coatings can extend the lifespan of products by up to ten times.
- Environmental Benefits: A greener alternative to chrome plating, as it avoids toxic byproducts.
- Versatility: Suitable for a wide range of metals and applications, from functional to decorative.
-
Materials Beyond Metals
- PVD is not limited to metals; it can also coat plastics (e.g., ABS, polycarbonate) and other materials like glass and ceramics. This versatility makes it a preferred choice for industries requiring both functional and aesthetic enhancements.
By understanding these key points, purchasers and manufacturers can make informed decisions about which metals and materials are best suited for PVD coating, ensuring optimal performance and longevity for their products.
Summary Table:
Category | Details |
---|---|
Common Metals | Stainless steel, titanium, copper, brass, aluminum, tungsten, zinc |
Pre-Treatment Needs | Vacuum compatibility, temperature tolerance (up to 800°F/427°C) |
Exclusions | Brass without galvanization, untreated galvanized materials, low-melting-point metals |
Applications | Automotive, medical tools, industrial tools, decorative uses |
Advantages | Enhanced durability, environmental benefits, versatility |
Materials Beyond Metals | Plastics (ABS, polycarbonate), glass, ceramics |
Ready to enhance your products with PVD coating? Contact our experts today to get started!