Compression molding utilizes a variety of resins, both thermoset and thermoplastic, to create durable and complex parts. Thermoset resins like SMC, BMC, TMC, epoxy, phenolic, melamine, and urea are commonly used due to their ability to harden permanently under heat and pressure. Thermoplastic resins such as polypropylene, nylon, UHMWPE, HDPE, and high-temperature materials like PEEK, PEKK, and PAEK are also employed for their recyclability and versatility. The process involves placing the resin in a mold, applying heat and pressure to shape it, and then cooling it to form the final product. This method is particularly effective for automotive components, offering efficiency and cost savings.
Key Points Explained:
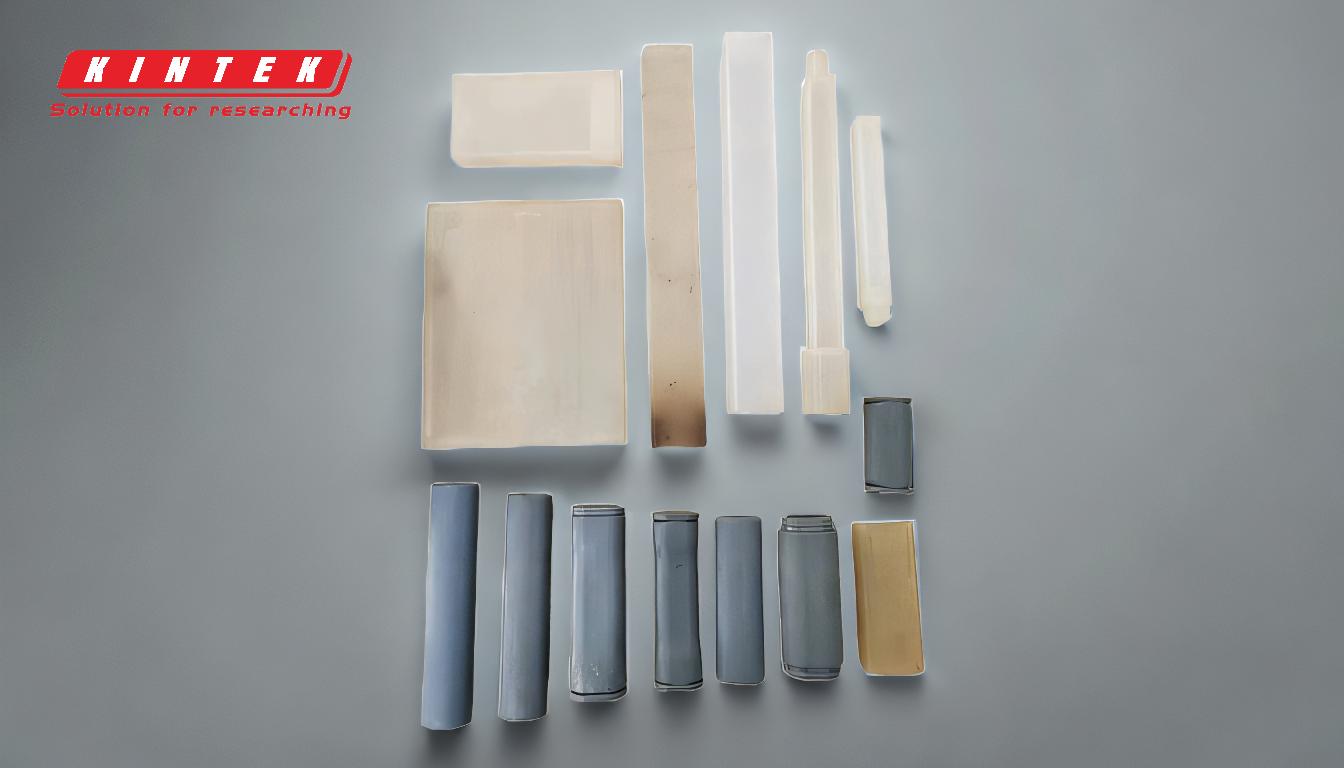
-
Types of Resins Used in Compression Molding:
-
Thermoset Resins:
- SMC (Sheet Molding Compound): A composite material consisting of polyester resin, fillers, and fiberglass reinforcement. It is used for high-strength applications.
- BMC (Bulk Molding Compound): Similar to SMC but with a dough-like consistency, used for intricate parts requiring high dimensional stability.
- TMC (Thick Molding Compound): A thicker version of SMC, offering better flow characteristics and used for larger parts.
- Epoxy: Known for its excellent mechanical properties and chemical resistance, used in high-performance applications.
- Phenolic: Offers high heat resistance and electrical insulation, commonly used in electrical components.
- Melamine and Urea: These resins are used for their excellent surface finish and resistance to heat and chemicals, often found in household items and laminates.
-
Thermoplastic Resins:
- Polypropylene: Lightweight and resistant to chemical corrosion, used in automotive and consumer goods.
- Nylon: Known for its toughness and wear resistance, used in gears and bearings.
- UHMWPE (Ultra-High Molecular Weight Polyethylene): Offers high impact strength and low friction, used in medical devices and liners.
- HDPE (High-Density Polyethylene): Known for its high strength-to-density ratio, used in containers and piping.
-
High-Temperature Materials:
- PEEK (Polyether Ether Ketone): Offers excellent mechanical and chemical resistance at high temperatures, used in aerospace and automotive industries.
- PEKK (Polyether Ketone Ketone): Similar to PEEK but with better thermal stability, used in demanding applications.
- PAEK (Polyaryletherketone): A family of high-performance thermoplastics used in extreme environments.
-
-
Process of Compression Molding:
- Material Placement: The resin, often in the form of a preform or sheet, is placed in the mold cavity.
- Application of Heat and Pressure: The mold is closed, and heat and pressure are applied, causing the resin to flow and fill the cavity.
- Cooling and Solidification: The material is cooled under pressure to solidify into the desired shape.
- Removal of Excess Material: Any excess material, known as mold flash, is trimmed away after the part is ejected from the mold.
-
Advantages of Compression Molding:
- Efficiency: The process is fast and reduces material waste, making it cost-effective.
- Versatility: Suitable for a wide range of materials and complex shapes.
- Strength and Durability: Produces parts with high strength and durability, ideal for automotive and industrial applications.
-
Applications in Automotive Manufacturing:
- Interior Components: Compression molding is used to create various interior parts such as sun visors, gear knobs, and trim covers.
- High-Performance Parts: The use of high-temperature resins like PEEK and PAEK allows for the production of components that can withstand extreme conditions.
By understanding the types of resins and the compression molding process, manufacturers can select the appropriate materials and methods to produce high-quality, durable parts efficiently.
Summary Table:
Resin Type | Examples | Key Properties | Applications |
---|---|---|---|
Thermoset Resins | SMC, BMC, TMC, Epoxy, Phenolic, Melamine, Urea | Permanent hardening, high strength, heat resistance, chemical resistance | Automotive, electrical components, household items |
Thermoplastic Resins | Polypropylene, Nylon, UHMWPE, HDPE, PEEK, PEKK, PAEK | Recyclable, versatile, high impact strength, low friction, high-temperature stability | Automotive, consumer goods, medical devices, aerospace |
Ready to optimize your manufacturing process with the right resins? Contact us today for expert guidance!