Argon is widely used in magnetron sputtering due to its inert nature, which ensures it does not react with the target material or the substrate. This makes it ideal for creating a stable and non-reactive environment during the sputtering process. Additionally, argon's relatively low cost compared to other inert gases and its ability to generate a high-density plasma make it a practical choice for industrial applications. Magnetron sputtering relies on the controlled deposition of atoms onto a substrate, and argon's properties facilitate precise control over the deposition process, ensuring uniform and high-quality thin films.
Key Points Explained:
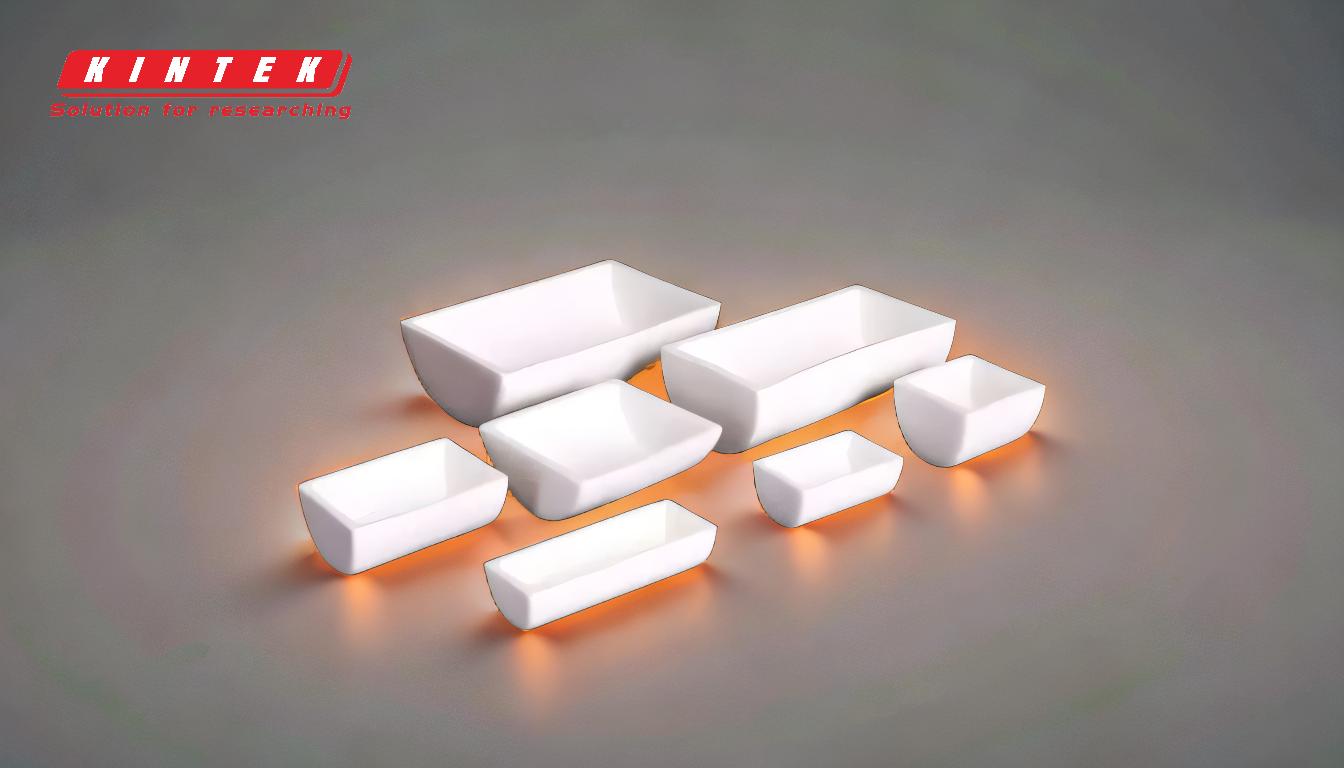
-
Inert Nature of Argon:
- Argon is an inert gas, meaning it does not chemically react with most materials, including metals. This property is crucial in magnetron sputtering, where the goal is to deposit a thin film of material onto a substrate without introducing impurities or unwanted chemical reactions.
- The inertness of argon ensures that the target material (the source of the sputtered atoms) remains unaltered, and the deposited film retains its desired properties.
-
Stable Plasma Generation:
- Argon is highly effective in generating a stable and dense plasma when ionized in a vacuum chamber. This plasma is essential for the sputtering process, as it provides the energy needed to dislodge atoms from the target material.
- The high-density plasma produced by argon allows for efficient sputtering rates, making the process faster and more cost-effective.
-
Cost-Effectiveness:
- While argon is not the cheapest gas available, it is relatively affordable compared to other inert gases like krypton or xenon. This makes it a practical choice for industrial applications where large volumes of gas are required.
- The balance between cost and performance makes argon the preferred choice for many sputtering applications.
-
Control Over Deposition Process:
- Magnetron sputtering relies on precise control over the deposition of atoms onto the substrate. Argon's properties, combined with the magnetic fields generated by the magnetron, allow for predictable and controlled paths of the ejected atoms.
- This control ensures uniform film thickness and high-quality coatings, which are critical for applications in industries such as aerospace, electronics, and optics.
-
Compatibility with Various Materials:
- Argon's inertness makes it compatible with a wide range of target materials, including metals, semiconductors, and insulators. This versatility is a significant advantage in magnetron sputtering, where different materials may be used depending on the application.
- The ability to use argon with various materials simplifies the sputtering process and reduces the need for specialized gases.
-
Minimal Contamination:
- Since argon does not react with the target material or the substrate, it minimizes the risk of contamination during the sputtering process. This is particularly important in applications where purity is critical, such as in the production of semiconductors or optical coatings.
- The use of argon helps maintain the integrity of the deposited film, ensuring that it meets the required specifications.
In summary, argon's inert nature, ability to generate stable plasma, cost-effectiveness, and compatibility with various materials make it an ideal choice for magnetron sputtering. These properties ensure precise control over the deposition process, resulting in high-quality thin films with minimal contamination.
Summary Table:
Key Benefit | Description |
---|---|
Inert Nature | Argon does not react with target materials, ensuring pure, unaltered thin films. |
Stable Plasma Generation | Produces high-density plasma for efficient and controlled sputtering. |
Cost-Effectiveness | Affordable compared to other inert gases like krypton or xenon. |
Control Over Deposition | Enables uniform film thickness and high-quality coatings. |
Material Compatibility | Works with metals, semiconductors, and insulators for versatile applications. |
Minimal Contamination | Reduces impurities, critical for industries like semiconductors and optics. |
Learn how argon can optimize your magnetron sputtering process—contact our experts today!