DC sputtering is not suitable for insulating materials due to their inherent electrical properties, which disrupt the sputtering process. Insulators have high DC impedance, making it difficult to ignite and sustain a plasma. Additionally, insulating materials accumulate charge over time, leading to issues like arcing, target poisoning, and the "disappearing anode effect." These problems halt the sputtering process and degrade the quality of the deposited film. Advanced techniques like RF or pulsed DC sputtering are better suited for insulating materials, as they prevent charge buildup and ensure stable plasma conditions.
Key Points Explained:
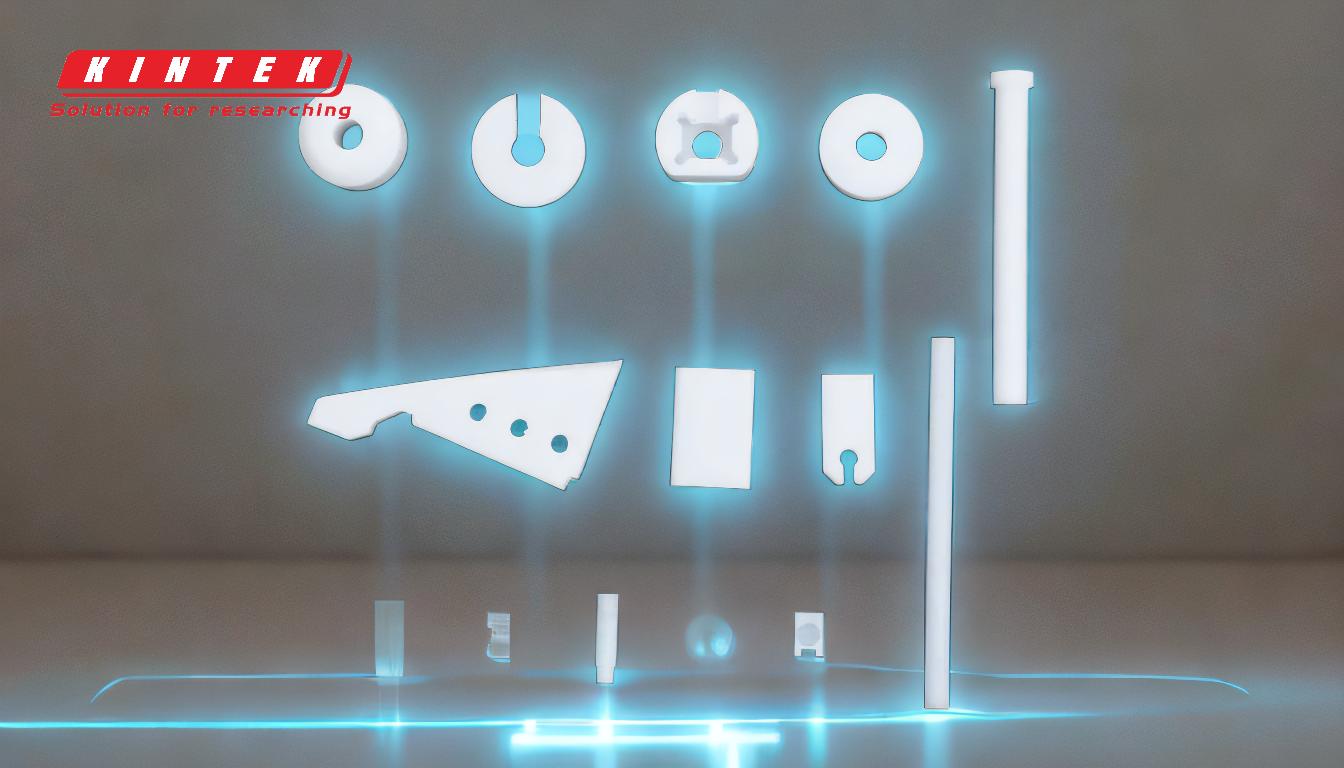
-
High DC Impedance of Insulating Materials:
- Insulating materials such as oxides, nitrides, and ceramics have very high electrical resistance, making it difficult for a DC current to pass through them.
- This high impedance requires prohibitively high voltages to ignite and maintain a plasma, which is impractical and inefficient.
- Without a stable plasma, the sputtering process cannot proceed effectively.
-
Charge Accumulation on Insulating Materials:
- Insulating materials do not conduct electricity, so they accumulate charge during the sputtering process.
- This charge buildup can lead to arcing, which disrupts the deposition process and damages the target or substrate.
- Over time, the accumulated charge can completely halt the sputtering process, making DC sputtering unsuitable for insulators.
-
Target Poisoning:
- In DC sputtering, insulating materials can cause target poisoning, where the target surface becomes coated with a non-conductive layer.
- This layer prevents further sputtering by blocking the DC current, effectively stopping the process.
- Target poisoning not only halts deposition but also requires frequent maintenance to clean or replace the target.
-
Disappearing Anode Effect:
- When insulating materials are deposited, the anode (typically a conductive surface) can become coated with the insulating film.
- This coating turns the anode into an insulator, disrupting the electrical circuit needed for sputtering.
- The "disappearing anode effect" leads to unstable plasma conditions and further complicates the process.
-
Lower Deposition Rates:
- DC sputtering generally has lower deposition rates compared to advanced techniques like High Power Impulse Magnetron Sputtering (HIPIMS).
- This is due to lower plasma densities and higher gas densities in DC sputtering systems.
- For insulating materials, these limitations are exacerbated, making DC sputtering even less efficient.
-
Alternative Techniques for Insulating Materials:
- Techniques like RF (Radio Frequency) sputtering or pulsed DC sputtering are better suited for insulating materials.
- These methods prevent charge buildup by alternating the polarity of the applied voltage, ensuring stable plasma conditions.
- RF and pulsed DC sputtering also offer higher deposition rates and better control over the process parameters.
-
Process Control Challenges:
- DC sputtering requires precise control of parameters such as gas pressure, target-substrate distance, and voltage.
- When working with insulating materials, maintaining these parameters becomes even more challenging due to the issues mentioned above.
- Advanced techniques provide better process control, making them more reliable for insulating materials.
In summary, DC sputtering is not used for insulators because of their high DC impedance, charge accumulation, and the resulting issues like arcing, target poisoning, and the disappearing anode effect. These problems make DC sputtering inefficient and unreliable for insulating materials, necessitating the use of alternative techniques like RF or pulsed DC sputtering.
Summary Table:
Issue | Description |
---|---|
High DC Impedance | Insulators require high voltages to ignite plasma, making DC sputtering inefficient. |
Charge Accumulation | Insulators accumulate charge, causing arcing and halting the sputtering process. |
Target Poisoning | Non-conductive layers form on the target, blocking DC current and stopping sputtering. |
Disappearing Anode Effect | Insulating films coat the anode, disrupting the electrical circuit and plasma stability. |
Lower Deposition Rates | DC sputtering has lower rates compared to advanced techniques like HIPIMS. |
Alternative Techniques | RF and pulsed DC sputtering prevent charge buildup and offer better process control. |
Struggling with insulating materials in sputtering? Contact our experts today to explore advanced solutions like RF and pulsed DC sputtering!