Ball milling is a widely used technique in material science and engineering due to its cost-effectiveness, simplicity, and ability to produce nanomaterials and introduce crystal defects. These features make it particularly valuable for applications requiring enhanced material properties, such as improved reactivity or mechanical strength. The process involves the mechanical grinding of materials using balls, which can lead to particle size reduction, alloying, and the creation of defects that can be advantageous for specific applications. Below, we explore the key reasons why ball milling is used for materials, focusing on its benefits and applications.
Key Points Explained:
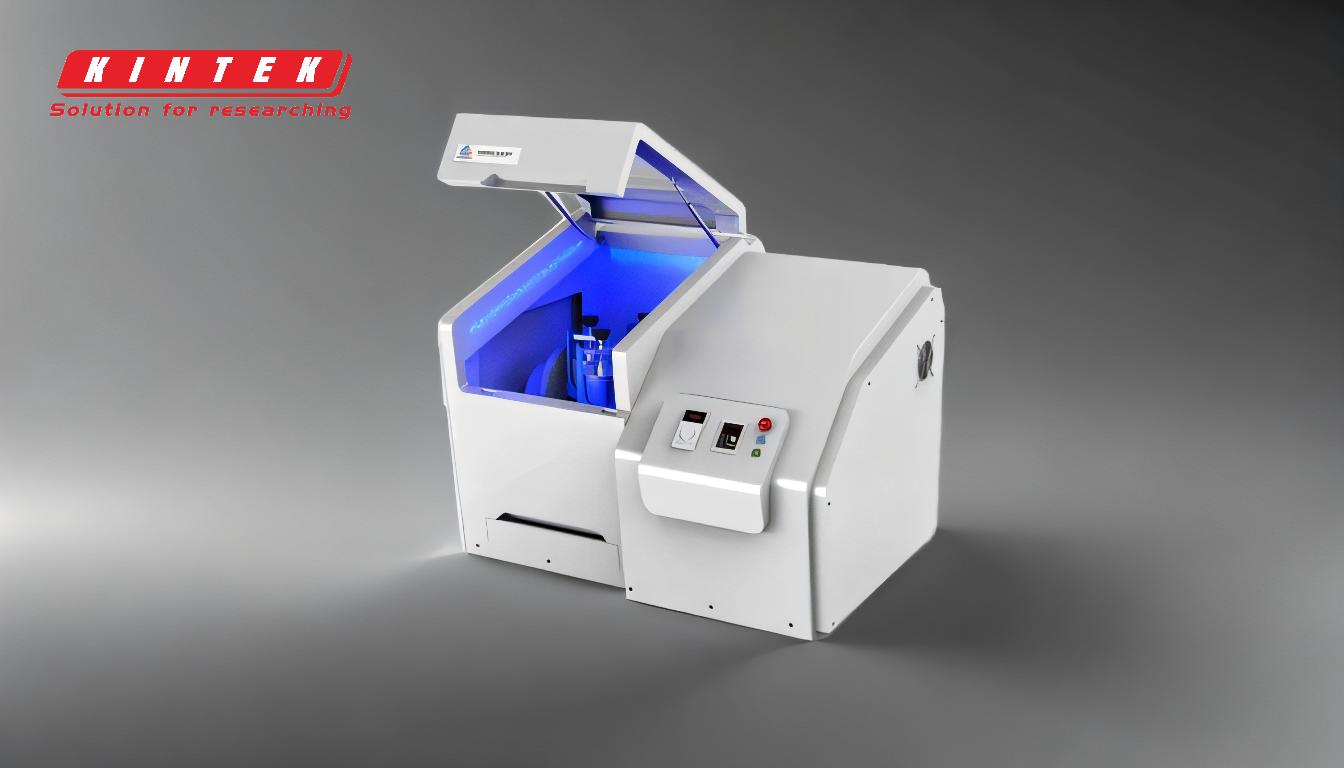
-
Cost-Effectiveness and Simplicity
- Ball milling is an inexpensive method compared to other material processing techniques. It requires relatively simple equipment and can be performed in standard laboratory or industrial settings.
- The process does not require complex setups or high-energy inputs, making it accessible for a wide range of applications.
- This affordability and ease of operation make ball milling a preferred choice for both research and industrial-scale material processing.
-
Production of Nanomaterials
- Ball milling is a classic method for preparing nanomaterials, which are materials with at least one dimension in the nanometer range (1–100 nm).
- The mechanical grinding action of the balls reduces the particle size of the material, leading to the formation of nanoparticles.
- Nanomaterials often exhibit unique properties, such as increased surface area, enhanced reactivity, and improved mechanical strength, which are desirable for applications in catalysis, energy storage, and advanced composites.
-
Creation of Crystal Defects
- The high-energy impact and friction during ball milling introduce crystal defects, such as dislocations, vacancies, and grain boundaries, into the material.
- These defects can enhance the material's properties, such as its mechanical strength, hardness, and electrical conductivity.
- For example, the presence of defects can improve the performance of materials in applications like hydrogen storage, where defects facilitate the diffusion of hydrogen atoms.
-
Versatility in Material Processing
- Ball milling can be used for a wide range of materials, including metals, ceramics, polymers, and composites.
- It is suitable for various processes, such as mechanical alloying, where different powders are mixed and milled to form homogeneous alloys.
- This versatility makes ball milling a valuable tool for developing new materials with tailored properties.
-
Scalability and Industrial Applications
- Ball milling can be easily scaled up from laboratory to industrial levels, making it suitable for large-scale production.
- It is widely used in industries such as pharmaceuticals, metallurgy, and electronics for tasks like powder blending, particle size reduction, and surface modification.
- The ability to produce consistent and high-quality materials on a large scale further underscores its importance in material science.
-
Environmental and Energy Efficiency
- Compared to some high-temperature or chemical-based processes, ball milling is relatively energy-efficient and environmentally friendly.
- It does not require the use of hazardous chemicals or produce significant waste, aligning with sustainable manufacturing practices.
- This aspect is increasingly important in modern material processing, where environmental impact is a key consideration.
In summary, ball milling is a versatile, cost-effective, and efficient method for material processing, offering unique advantages such as the production of nanomaterials and the introduction of beneficial crystal defects. Its simplicity, scalability, and environmental benefits make it a cornerstone technique in both research and industrial applications.
Summary Table:
Key Benefits of Ball Milling | Description |
---|---|
Cost-Effectiveness | Inexpensive, simple equipment, and low energy requirements. |
Nanomaterial Production | Produces nanoparticles with unique properties like enhanced reactivity. |
Crystal Defect Creation | Introduces defects to improve mechanical strength and conductivity. |
Versatility | Suitable for metals, ceramics, polymers, and composites. |
Scalability | Easily scaled from lab to industrial levels for large-scale production. |
Environmental Efficiency | Energy-efficient and eco-friendly, aligning with sustainable practices. |
Interested in leveraging ball milling for your material processing needs? Contact us today to learn more!