Chromium coating is renowned for its exceptional corrosion resistance, making it a preferred choice for protecting metal surfaces in various industries. This resistance stems from chromium's ability to form a thin, stable, and self-repairing oxide layer when exposed to oxygen. This passive layer acts as a barrier, preventing further oxidation and corrosion of the underlying metal. Additionally, chromium coatings are often applied through electroplating, which ensures a uniform and dense layer that enhances durability. The combination of chromium's inherent chemical properties and the application process makes it highly effective in resisting environmental factors such as moisture, chemicals, and salt, thereby prolonging the lifespan of coated materials.
Key Points Explained:
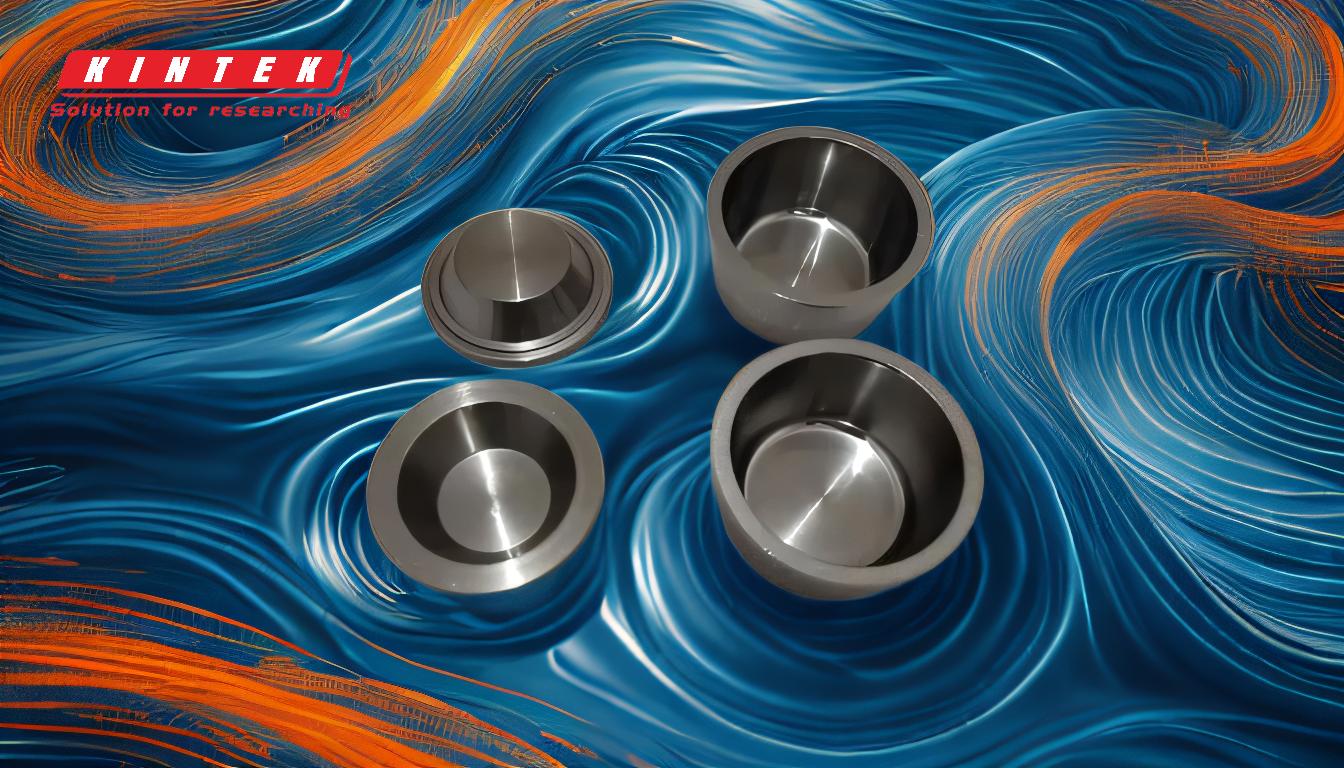
-
Formation of a Passive Oxide Layer:
- When chromium is exposed to oxygen, it reacts to form a thin, adherent, and chemically stable chromium oxide (Cr₂O₃) layer on its surface.
- This oxide layer is passive, meaning it does not react further with the environment, effectively shielding the underlying metal from corrosive agents.
- The layer is also self-repairing; if scratched or damaged, it quickly reforms in the presence of oxygen, maintaining continuous protection.
-
Chemical Stability of Chromium Oxide:
- Chromium oxide is highly resistant to a wide range of chemicals, including acids, alkalis, and salts, which are common causes of corrosion.
- This stability ensures that the coating remains intact even in harsh environments, such as industrial settings or marine applications.
-
Electroplating Process Enhances Protection:
- Chromium coatings are typically applied through electroplating, a process that deposits a uniform and dense layer of chromium onto the metal surface.
- The electroplated layer is free from pores and defects, which are potential weak points for corrosion to initiate.
- This uniformity ensures consistent protection across the entire surface, even in complex geometries.
-
Resistance to Environmental Factors:
- Chromium coatings are highly effective in resisting moisture, which is a primary driver of corrosion in metals.
- They also provide excellent protection against salt spray, making them ideal for marine and coastal applications.
- The coatings can withstand exposure to UV radiation and temperature fluctuations without degrading.
-
Applications in Corrosive Environments:
- Chromium coatings are widely used in industries such as automotive, aerospace, and manufacturing, where components are exposed to corrosive conditions.
- Examples include chrome-plated car parts, aircraft components, and industrial machinery, where durability and longevity are critical.
-
Economic and Functional Benefits:
- The long-lasting nature of chromium coatings reduces the need for frequent maintenance or replacement, offering cost savings over time.
- The aesthetic appeal of a shiny, reflective chromium finish also adds value to products, making it a dual-purpose solution for both protection and appearance.
In summary, the corrosion resistance of chromium coatings is a result of the formation of a passive oxide layer, the chemical stability of chromium oxide, the effectiveness of the electroplating process, and the ability to withstand environmental challenges. These properties make chromium coatings an ideal choice for protecting metal surfaces in demanding applications.
Summary Table:
Key Feature | Description |
---|---|
Passive Oxide Layer | Forms a thin, self-repairing chromium oxide layer that shields against corrosion. |
Chemical Stability | Resists acids, alkalis, and salts, maintaining protection in harsh environments. |
Electroplating Process | Ensures a uniform, dense, and defect-free coating for consistent protection. |
Environmental Resistance | Withstands moisture, salt spray, UV radiation, and temperature fluctuations. |
Applications | Widely used in automotive, aerospace, and manufacturing industries. |
Economic Benefits | Reduces maintenance costs and enhances product longevity and aesthetics. |
Learn how chromium coating can protect your metal surfaces—contact us today for expert advice!