Co-pyrolysis, the simultaneous thermal decomposition of biomass and synthetic polymers, is a critical process for optimizing the production of valuable chemical compounds like aromatic hydrocarbons. Biomass alone has limitations due to its low hydrogen and high oxygen content, which restricts its ability to produce high-quality fuels and chemicals. By co-pyrolyzing biomass with hydrogen-rich synthetic polymers, the hydrogen-to-carbon ratio is improved, leading to enhanced yields of aromatic hydrocarbons. This process not only maximizes resource utilization but also addresses waste management challenges by converting plastic waste into useful products. Co-pyrolysis is thus a sustainable and efficient method for producing high-value chemicals while reducing environmental impact.
Key Points Explained:
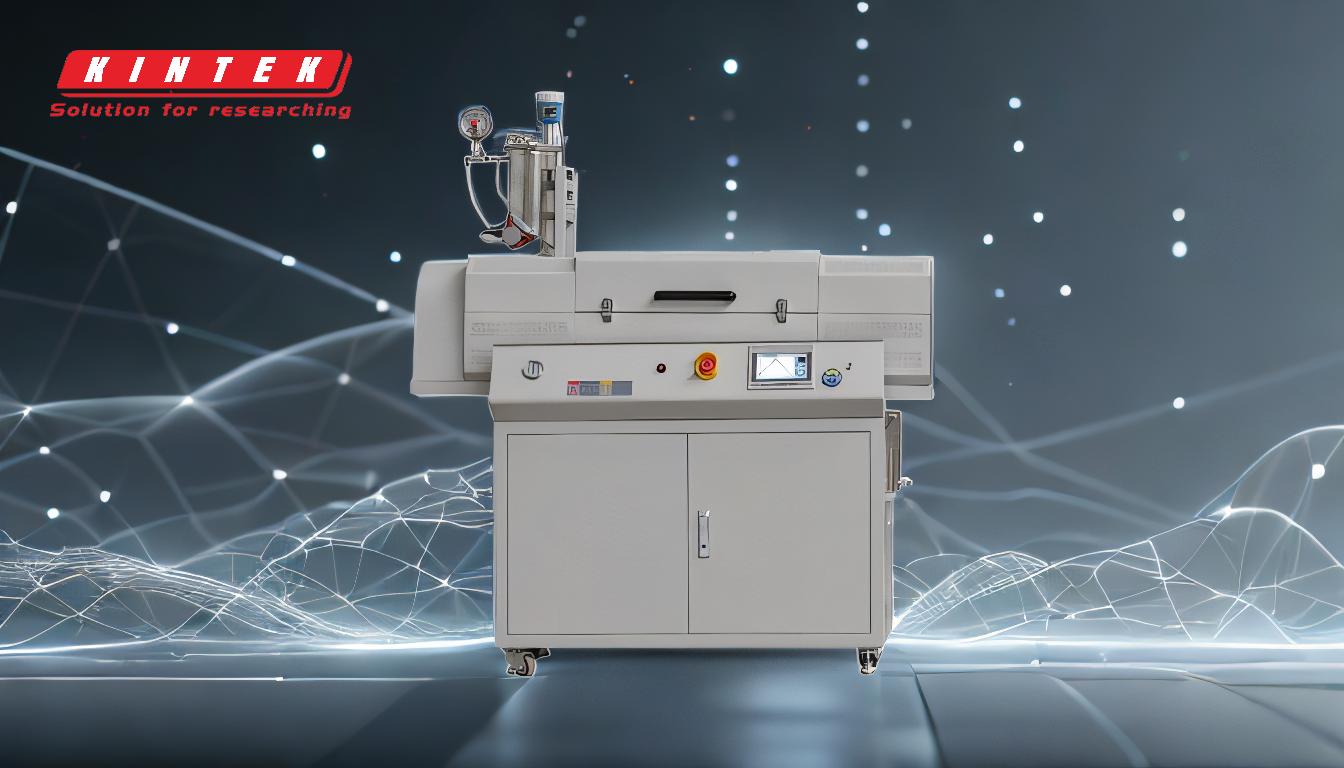
-
Enhancement of Aromatic Hydrocarbon Production:
- Biomass typically has a low hydrogen-to-carbon (H/C) ratio and a high oxygen-to-carbon (O/C) ratio, which limits its ability to produce aromatic hydrocarbons efficiently during pyrolysis.
- Synthetic polymers, on the other hand, are rich in hydrogen, which compensates for the hydrogen deficiency in biomass.
- During co-pyrolysis, the interaction between biomass and synthetic polymers leads to a more favorable H/C ratio, significantly increasing the yield of aromatic hydrocarbons.
-
Overcoming Biomass Limitations:
- Biomass pyrolysis alone often results in the formation of undesirable by-products like tar and char due to its high oxygen content.
- The addition of synthetic polymers reduces the formation of these by-products by providing additional hydrogen, which stabilizes the pyrolysis intermediates and promotes the formation of valuable aromatic compounds.
-
Waste Management and Resource Utilization:
- Co-pyrolysis provides a dual benefit by utilizing both biomass and synthetic polymer waste, such as plastics, which are otherwise challenging to dispose of sustainably.
- This process transforms waste materials into useful chemical feedstocks, contributing to a circular economy and reducing the environmental burden of plastic waste.
-
Synergistic Effects:
- Co-pyrolysis often exhibits synergistic effects, where the combined yield of aromatic hydrocarbons is higher than the sum of individual pyrolysis yields of biomass and synthetic polymers.
- This synergy is attributed to the interaction of free radicals and intermediates generated during the co-pyrolysis process, leading to more efficient chemical reactions.
-
Environmental and Economic Benefits:
- By converting waste materials into high-value chemicals, co-pyrolysis reduces reliance on fossil fuels and lowers greenhouse gas emissions.
- The process also offers economic advantages by producing marketable products like aromatic hydrocarbons, which are widely used in the chemical and fuel industries.
-
Applications in Industry:
- Aromatic hydrocarbons produced through co-pyrolysis are essential raw materials for manufacturing plastics, solvents, and fuels.
- The process can be integrated into existing pyrolysis facilities, making it a scalable and practical solution for industries seeking sustainable alternatives.
In summary, co-pyrolysis is a transformative process that leverages the complementary properties of biomass and synthetic polymers to produce high-value aromatic hydrocarbons. It addresses both the technical limitations of biomass pyrolysis and the environmental challenges of plastic waste, making it a vital technique for sustainable resource management and chemical production.
Summary Table:
Key Benefits of Co-Pyrolysis | Details |
---|---|
Enhanced Aromatic Hydrocarbon Yield | Improves H/C ratio, increasing production of valuable chemicals. |
Overcomes Biomass Limitations | Reduces tar and char formation by stabilizing pyrolysis intermediates. |
Waste Management | Converts plastic waste into useful chemical feedstocks. |
Synergistic Effects | Combined yields exceed individual pyrolysis results due to chemical synergy. |
Environmental Benefits | Reduces fossil fuel reliance and greenhouse gas emissions. |
Industrial Applications | Produces raw materials for plastics, solvents, and fuels. |
Ready to explore how co-pyrolysis can benefit your operations? Contact us today to learn more!