Tungsten is widely used in furnaces due to its exceptional properties, such as its high melting point, low vapor pressure, and resistance to corrosion in specific environments. These characteristics make it ideal for high-temperature applications, including heating elements, vacuum furnaces, and specialized processes like metal injection molding (MIM) and vapor deposition. Tungsten's ability to maintain structural integrity at extreme temperatures and its compatibility with non-oxidizing environments ensure that it performs reliably in demanding industrial settings. Additionally, advancements in furnace technology, such as Human-Machine Interfaces (HMIs), enhance the usability and efficiency of tungsten-based systems, further extending their lifespan and performance.
Key Points Explained:
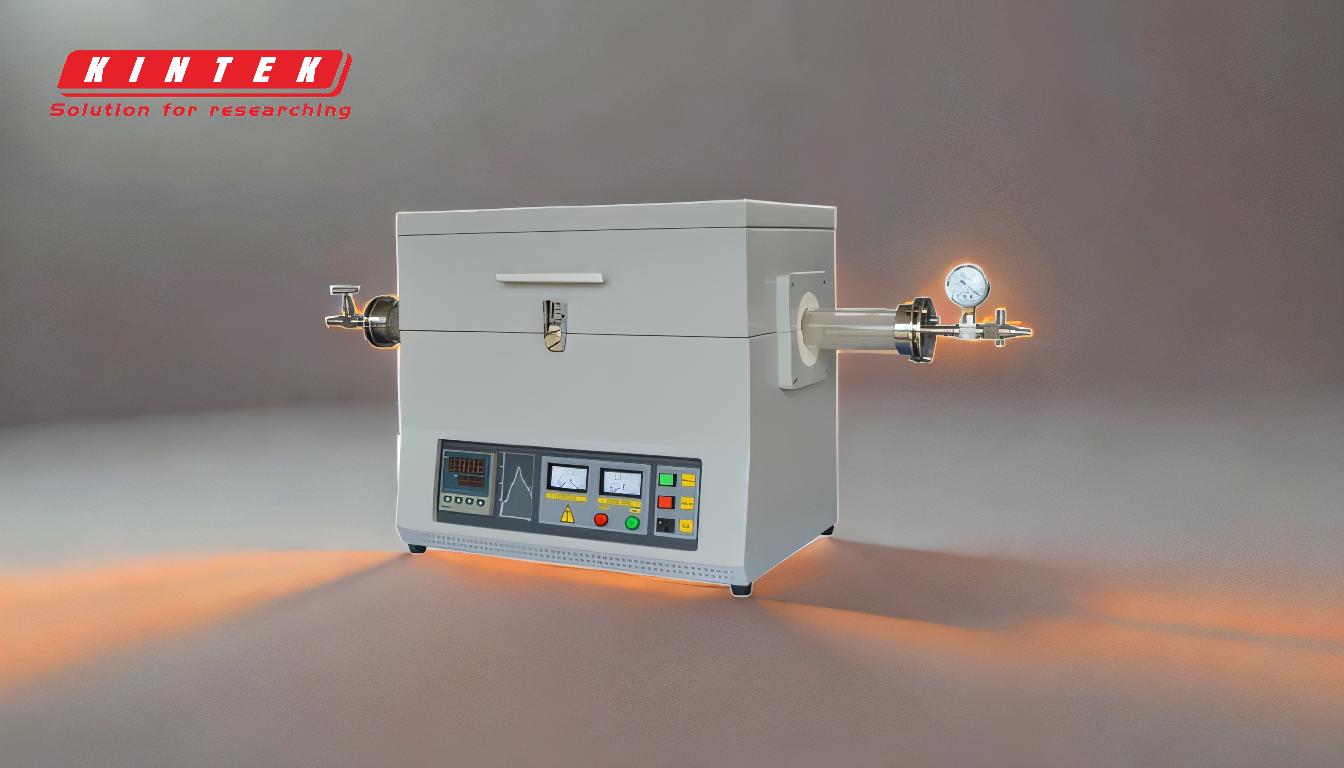
-
High Melting Point and Temperature Resistance
- Tungsten has one of the highest melting points of all metals, at approximately 3422°C (6192°F). This makes it suitable for use in furnaces that require extremely high operating temperatures, such as those used in metal injection molding (MIM) or vapor deposition processes. Its high duty temperature of 2800°C (5075°F) allows it to function effectively as a heating element in these environments.
- However, tungsten's practical temperature rating is often downgraded due to its brittleness when exposed to oxygen or water vapor. This sensitivity necessitates the use of controlled atmospheres, such as vacuum or inert gas environments, to prevent oxidation and maintain its structural integrity.
-
Low Vapor Pressure in High-Temperature Applications
- Tungsten's low vapor pressure is a critical advantage in high-temperature furnaces. In non-oxidizing environments, it does not release contaminants like oxygen, carbon, or moisture, which could compromise the quality of materials being processed. This property is particularly beneficial in MIM furnaces and other applications where material purity is essential.
- For example, in vapor deposition coating furnaces, tungsten wires are used to uniformly transmit extreme heat, enabling processes like ultra-high-temperature diamond coating. The absence of contamination ensures the integrity of the deposited materials.
-
Resistance to Corrosion and Oxidation
- Tungsten exhibits excellent resistance to corrosion below 60% relative humidity, making it suitable for use in controlled environments. However, it is highly sensitive to oxidation at elevated temperatures, which is why vacuum furnaces or inert gas atmospheres are often employed to protect tungsten components.
- Modern tungsten vacuum furnaces are equipped with advanced features like automatic gas extraction and cooling programs, which remove residual oxygen from the chamber. This extends the life of the hot zone and prevents oxidation, ensuring long-term reliability.
-
Applications in Specialized Furnace Components
- Tungsten is used in various furnace components, including heating elements, welding electrodes, and tungsten boats. Its ability to maintain its shape at high temperatures makes it ideal for these applications.
- In welding electrodes, tungsten's durability ensures consistent performance, while in vapor deposition furnaces, its uniform heat transmission enables precise coating processes.
-
Integration with Advanced Furnace Technology
- The incorporation of Human-Machine Interfaces (HMIs) in tungsten vacuum furnaces enhances their usability and efficiency. HMIs provide a user-friendly interface for controlling furnace functions, such as pumping, gas handling, and venting.
- Features like manual adjustment of gas flow rates and pumping speed, along with automatic gas extraction programs, optimize furnace performance and extend the lifespan of tungsten components.
In summary, tungsten's unique properties, including its high melting point, low vapor pressure, and resistance to corrosion, make it an indispensable material for high-temperature furnace applications. Its integration with advanced technologies like HMIs further enhances its functionality, ensuring reliable and efficient operation in demanding industrial processes.
Summary Table:
Property | Benefit |
---|---|
High Melting Point (3422°C) | Suitable for extreme temperatures in MIM and vapor deposition processes. |
Low Vapor Pressure | Prevents contamination in non-oxidizing environments, ensuring material purity. |
Corrosion Resistance | Performs reliably in controlled atmospheres like vacuum or inert gas. |
Advanced HMI Integration | Enhances usability, efficiency, and lifespan of tungsten-based systems. |
Discover how tungsten can optimize your furnace performance—contact our experts today!