Using a pre-press mold offers several advantages, particularly in the context of processing cannabis or similar materials. The primary benefit is the even distribution of material within the rosin filter bag, ensuring that the material is pressed flush against the sides of the bag and minimizing gaps. This leads to more efficient extraction and better-quality output. Additionally, pre-press molds are cost-effective, easy to manufacture, and durable, making the overall process more efficient and economical.
Key Points Explained:
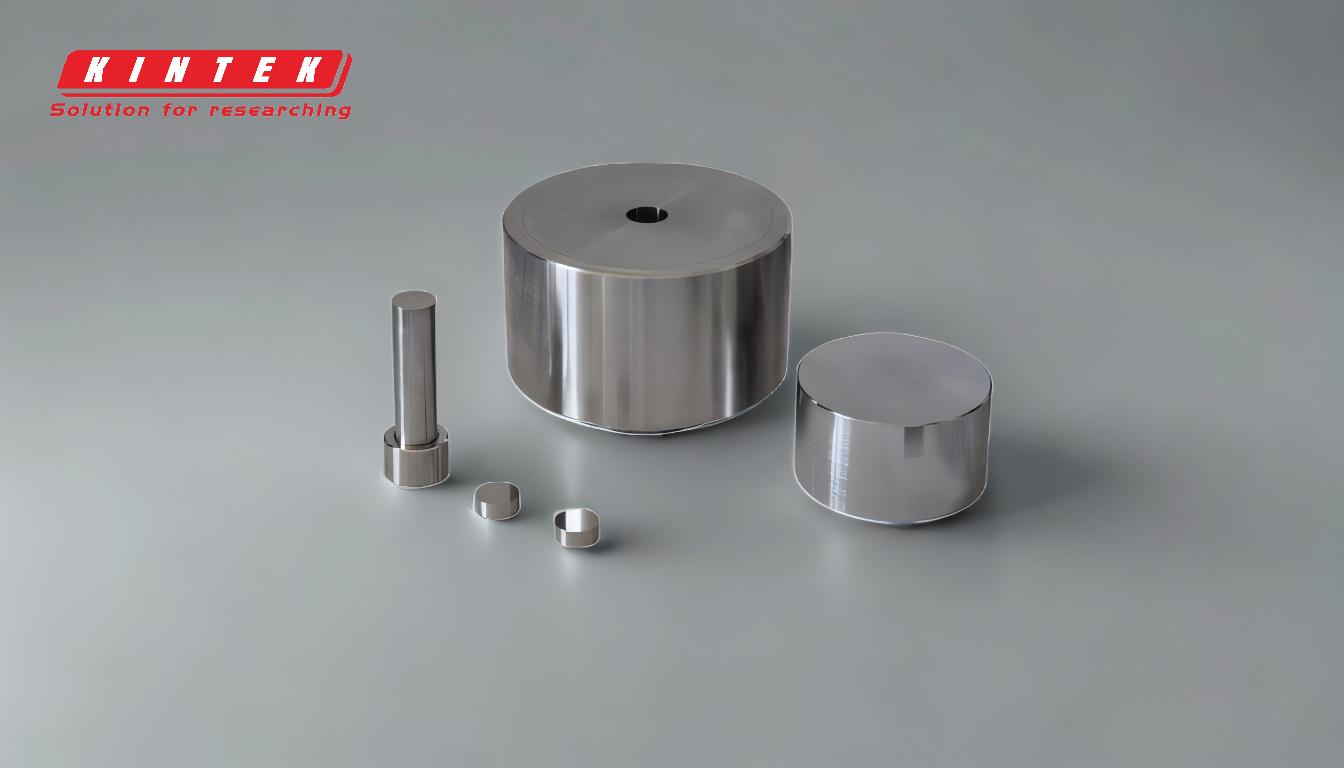
-
Even Distribution of Material:
- Pre-pressing ensures that the material is evenly distributed within the rosin filter bag.
- This uniform distribution helps in achieving consistent pressure during the pressing process, which is crucial for efficient extraction.
- Even distribution also prevents the formation of gaps, which can lead to uneven extraction and lower-quality output.
-
Flush Pressing Against Bag Sides:
- The pre-press mold helps in pressing the material flush against the sides of the filter bag.
- This ensures that the entire surface area of the material is in contact with the filter, maximizing the extraction efficiency.
- Flush pressing also helps in maintaining the structural integrity of the filter bag, preventing any potential leaks or blowouts during the pressing process.
-
Minimization of Gaps:
- By minimizing gaps within the mass of cannabis material, the pre-press mold ensures a more compact and dense material pack.
- This compactness leads to better heat transfer and pressure application during the extraction process, resulting in higher yields and better-quality rosin.
- Minimizing gaps also reduces the chances of channeling, where the solvent or pressure takes the path of least resistance, leading to uneven extraction.
-
Cost-Effectiveness and Durability:
- Pre-press molds are generally easy to manufacture and have a long service life, making them a cost-effective solution.
- The durability of these molds ensures that they can withstand repeated use without significant wear and tear, reducing the need for frequent replacements.
- This durability, combined with their ease of manufacture, makes pre-press molds an economical choice for both small-scale and large-scale operations.
-
Efficiency in the Isostatic Pressing Process:
- The use of pre-press molds in the isostatic pressing process enhances overall efficiency.
- By preparing the material in a pre-press mold, the subsequent pressing process becomes more streamlined and less prone to errors.
- This efficiency translates to time savings and higher throughput, which are critical factors in commercial operations.
In summary, the use of a pre-press mold is highly beneficial for ensuring even material distribution, flush pressing against bag sides, minimizing gaps, and enhancing the overall efficiency and cost-effectiveness of the extraction process. These advantages make pre-press molds an essential tool in the cannabis processing industry.
Summary Table:
Advantage | Description |
---|---|
Even Distribution of Material | Ensures uniform pressure, prevents gaps, and improves extraction efficiency. |
Flush Pressing Against Bag Sides | Maximizes surface contact, prevents leaks, and maintains bag integrity. |
Minimization of Gaps | Creates compact material packs for better heat transfer and higher yields. |
Cost-Effectiveness & Durability | Easy to manufacture, long-lasting, and reduces replacement costs. |
Efficiency in Isostatic Pressing | Streamlines the pressing process, saving time and increasing throughput. |
Ready to optimize your cannabis extraction process? Contact us today to learn more about pre-press molds!