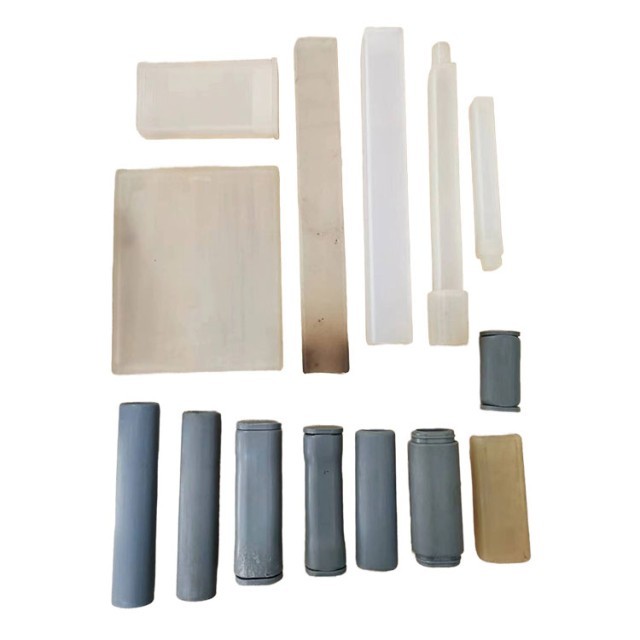
Molds & Accessories
Isostatic Molding Pressing Molds for Lab
Item Number : PIPM
Price varies based on specs and customizations
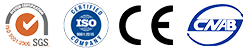
Shipping:
Contact us to get shipping details Enjoy On-time Dispatch Guarantee.
Why Choose Us
Reliable PartnerEasy ordering process, quality products, and dedicated support for your business success.
Introduction
Isostatic pressing molds are used in a process where powdered materials are enclosed in a flexible container and subjected to uniform pressure from all sides, typically via a liquid medium like water or oil. This method ensures the elimination of voids and air pockets, leading to products with enhanced density, strength, and dimensional accuracy. The process is crucial in manufacturing high-density, high-performance materials and is particularly effective for creating long, thin rod-like or tube-shaped bases that are challenging to produce through conventional methods.
Applications
Isostatic pressing molds find extensive use in various industries where the production of high-density, high-strength materials is crucial. This technology is particularly valued for its ability to create complex shapes with minimal internal defects, making it indispensable in several specialized sectors.
- Aerospace Industry: Used for manufacturing components that require high strength-to-weight ratios, such as turbine blades, engine parts, and structural components.
- Automotive Industry: Employed in the production of high-performance brake pads, seals, and gaskets that require uniform density and strength.
- Ceramics Manufacturing: Ideal for producing advanced ceramics with high density and improved mechanical properties, used in applications ranging from electronics to armor.
- Metal Powder Processing: Utilized to create dense metal parts from powdered materials, essential for applications in orthopedic implants, dental components, and precision engineering parts.
- Tool and Die Making: Used for producing high-precision molds and dies with complex geometries, ensuring uniform pressure distribution and minimal defects.
- Nuclear Industry: Applied in the fabrication of components that require high integrity and resistance to extreme conditions, such as fuel elements and structural components.
- Advanced Materials Research: Used in laboratories for developing new materials with tailored properties, leveraging the uniform pressure application to achieve desired densities and microstructures.
Detail & Parts
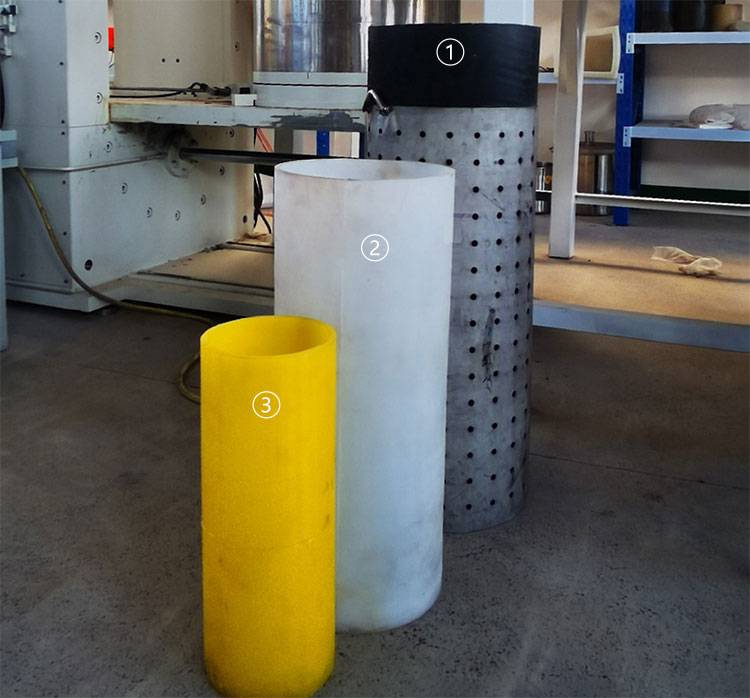
Features
Isostatic pressing molds are a critical component in the manufacturing of high-density, high-performance materials. These molds are designed to evenly distribute pressure on all sides of a powdered material, typically using a liquid medium like water or oil. This method ensures the elimination of voids and air pockets, leading to products with enhanced density, strength, and dimensional accuracy. Here are the main features of isostatic pressing molds, focusing on their benefits to the customer:
-
Uniform Pressure Distribution: By utilizing a liquid medium to apply pressure, isostatic pressing molds ensure that the force is evenly distributed across the material. This uniformity is crucial for achieving consistent product quality and performance.
-
Increased Material Density: The even pressure applied by the mold helps in compacting the powdered material more effectively, resulting in higher density products. This is particularly beneficial for industries requiring materials with high strength and durability.
-
Enhanced Dimensional Accuracy: The precision of pressure application in isostatic pressing molds leads to products with improved dimensional accuracy. This feature is essential for applications where exact specifications are critical.
-
Versatility in Material Use: Isostatic pressing molds can accommodate a variety of materials, including those with high melting points. This versatility allows for the production of a wide range of products across different industries.
-
Reduced Voids and Air Pockets: The process effectively eliminates voids and air pockets, which are common in traditional manufacturing methods. This results in a more reliable and consistent product.
-
Suitable for Small to Medium-Sized Parts: While there are challenges with larger and more complex shapes, isostatic pressing molds are particularly effective for smaller to medium-sized parts. This makes them a cost-effective solution for many manufacturing needs.
These features make isostatic pressing molds an invaluable tool in the production of advanced materials, offering significant benefits in terms of product quality and performance.
Principle
Isostatic pressing involves enclosing a powdered material in a flexible mold and applying uniform pressure using a liquid medium like water or oil. This method ensures even force distribution, eliminating voids and enhancing product density, strength, and dimensional accuracy. The process leverages fluid mechanics to achieve isotropic pressure, leading to uniform compaction and improved material performance.
Advantages
-
High Compact Densities: Isostatic pressing achieves high compact densities, which is crucial for producing materials with increased strength and durability. This is particularly beneficial in industries requiring advanced materials with high performance.
-
Complex Shape Engineering: The process allows for the engineering of somewhat complex shapes into elastomeric molds, providing flexibility in product design that is not achievable with uniaxial presses.
-
Reduced Friction: Wet bag isostatic pressing involves very little friction, allowing for somewhat higher densities compared to other methods. This results in products with minimal voids and air pockets, enhancing overall quality.
-
Dimensional Accuracy: The even pressure applied on all sides by a liquid medium ensures dimensional accuracy, making it ideal for products that require precise specifications.
-
Large Size Compactions: Isostatic pressing supports large size compactions, enabling the production of multiple compactions in each cylinder. This is particularly advantageous for manufacturing large parts, which are better suited to the wet bag process.
-
Long Service Life and Lower Cost: The molds used in isostatic pressing can be easily made and have a long service life, contributing to lower overall costs in the production process.
-
Excellent Machinability: Products produced through isostatic pressing exhibit high strength and excellent machinability, significantly reducing internal stress and improving the usability of the final product.
FAQ
What Is Isostatic Pressing?
How Does Isostatic Pressing Differ From Traditional Pressing Methods
What Are The Main Types Of Isostatic Pressing?
Can Isostatic Pressing Be Used For Complex Shapes?
How Does The Fluid Medium Affect The Isostatic Pressing Process?
What Is Isostatic Pressing?
What Are The Benefits Of Isostatic Pressing?
What Are The Types Of Isostatic Pressing?
There are two main types of isostatic pressing:
- Hot Isostatic Pressing (HIP): This type of isostatic pressing uses high temperature and high pressure to consolidate and strengthen the material. The material is heated in a sealed container and then subjected to equal pressure from all directions.
- Cold Isostatic Pressing (CIP): In this type of isostatic pressing, the material is compacted at room temperature using hydraulic pressure. This method is commonly used to form ceramic and metal powders into complex shapes and structures.
What Type Of Isostatic Pressing Equipment Do You Have?
What Are The Wet Bag Process And The Dry Bag Process?
The CIP molding process is divided into two methods: the wet bag process and the dry bag process.
Wet bag process:
In this method, the powder material is placed in a flexible mold bag and placed in a pressure vessel filled with high-pressure liquid. This process is ideal for producing multi-shaped products and is suitable for small to large quantities, including large-sized parts.
Dry bag process:
In the dry bag process, a flexible membrane is integrated into the pressure vessel and is used throughout the pressing process. This membrane separates the pressure fluid from the mold, creating a "dry bag." This method is more hygienic as the flexible mold does not get contaminated with wet powder and requires less cleaning of the vessel. It also features fast cycles, making it ideal for mass producing powder products in an automated process.
How Long Is Your Delivery Time? If I Want To Customize The Instrument, How Long Does It Take?
4.7
out of
5
Incredible value for money! These molds have significantly improved our product density and strength.
4.8
out of
5
Fast delivery and top-notch quality. These molds are a game-changer for our precision engineering parts.
4.9
out of
5
Exceptional durability and technological advancement. Perfect for our advanced ceramics production.
4.7
out of
5
These molds offer unparalleled dimensional accuracy. A must-have for our aerospace components.
4.8
out of
5
Outstanding service and product quality. Our automotive brake pads have never been better.
4.9
out of
5
These molds are a technological marvel. They've revolutionized our metal powder processing.
4.7
out of
5
Great investment for our tool and die making. Uniform pressure distribution is spot on.
4.8
out of
5
These molds are incredibly versatile. They handle a variety of materials with ease.
4.9
out of
5
Highly recommend for nuclear industry components. The dimensional accuracy is impeccable.
4.7
out of
5
These molds have exceeded our expectations in advanced materials research. Truly innovative.
4.8
out of
5
The speed of delivery was impressive. These molds have enhanced our product's machinability.
4.9
out of
5
These molds are a key asset for our small to medium-sized parts production. Excellent quality.
4.7
out of
5
The molds have a long service life and lower cost. A fantastic choice for our manufacturing needs.
Products
Isostatic Molding Pressing Molds for Lab
REQUEST A QUOTE
Our professional team will reply to you within one business day. Please feel free to contact us!
Related Products
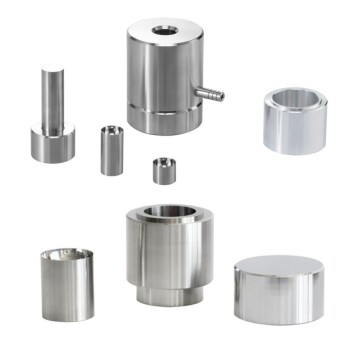
Explore versatile Hydraulic Hot Press molds for precise compression molding. Ideal for creating various shapes and sizes with uniform stability.
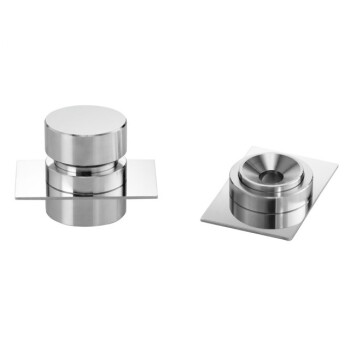
No Demolding Lab Infrared Press Mold for Laboratory Applications
Effortlessly test your samples with no demolding required using our lab infrared press mold. Enjoy high transmittance and customizable sizes for your convenience.
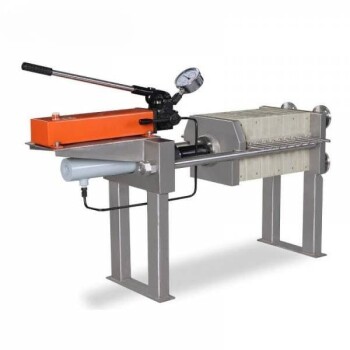
Hydraulic Diaphragm Lab Filter Press for Laboratory Filtration
Hydraulic diaphragm lab press filter is one type lab scale filter press, it takes small footprint, and higher pressing power.
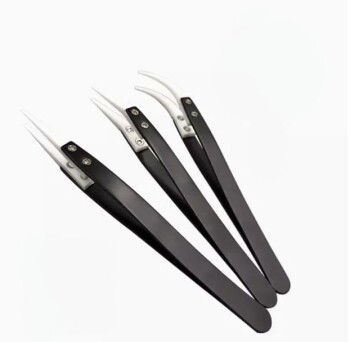
Engineering Advanced Fine Ceramics Head Tweezers with Pointed Elbow Zirconia Ceramic Tip
Zirconia ceramic tweezers are a high-precision tool made of advanced ceramic materials, especially suitable for operating environments that require high precision and corrosion resistance. This type of tweezers not only has excellent physical properties, but is also popular in the medical and laboratory fields because of its biocompatibility.
Related Articles
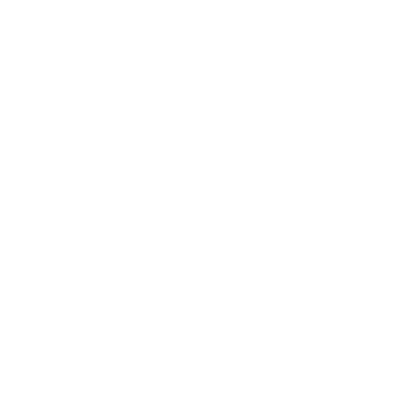
Isostatic Pressing Technology: Principles, Classification, and Applications
An in-depth look at isostatic pressing technology, its types, and diverse applications across various industries.
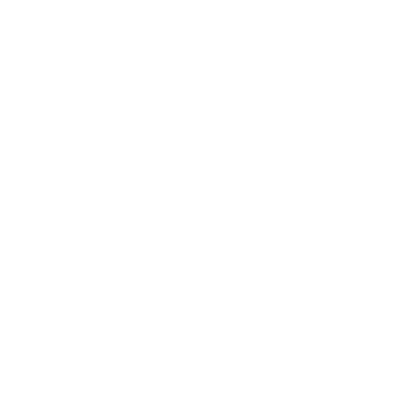
Zirconia Ceramic Rod Production Processes: Isostatic Pressing vs. Dry Pressing
A comparison of isostatic pressing and dry pressing in zirconia ceramic rod production, highlighting differences and advantages.
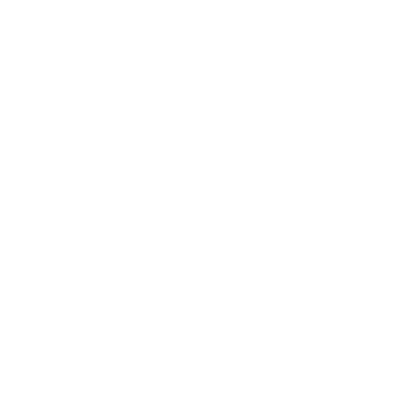
Comprehensive Guide to Isostatic Pressing:Processes, and Features
Isostatic pressing is a versatile manufacturing process that is widely used in various industries. It involves subjecting a material to equal pressure from all directions to achieve uniform density and shape. Isostatic pressing offers numerous advantages, such as the ability to produce complex shapes, uniformity in material properties, and high precision. This comprehensive guide will delve into the different types of isostatic pressing, including cold, warm, and hot pressing. We will explore the processes, features, and applications of each type, providing you with a thorough understanding of this essential manufacturing technique. So let's dive in!
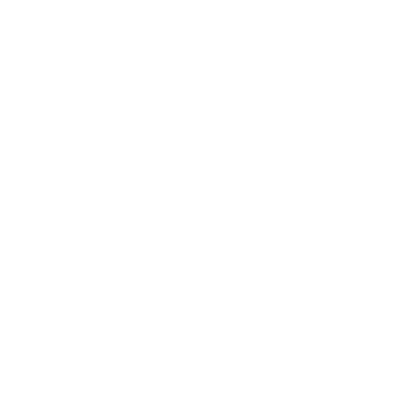
Understanding Isostatic Pressing: Process, Benefits, Limitations, and Applications
Isostatic pressing is a manufacturing process that offers numerous benefits and applications in various industries. It involves subjecting a material to equal pressure from all directions to achieve uniform density and shape. This method is particularly advantageous compared to other production techniques.
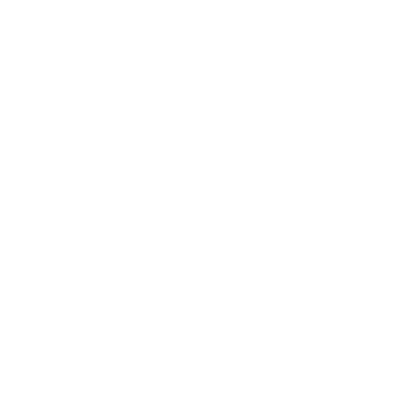
Isostatic Pressing Technology: Revolutionizing Ceramic Material Densification
Explore how isostatic pressing techniques enhance ceramic properties, achieving 100% theoretical density and eliminating porosity.
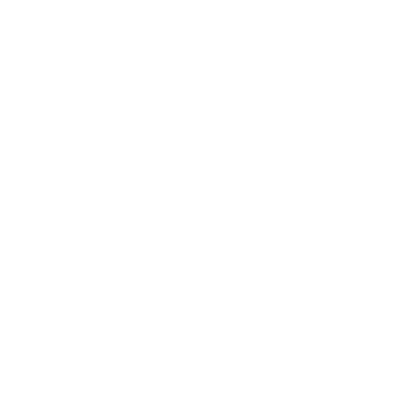
Selecting Isostatic Pressing Equipment for High-Density Molding
An in-depth look at isostatic pressing techniques and equipment selection for achieving high-density molding.
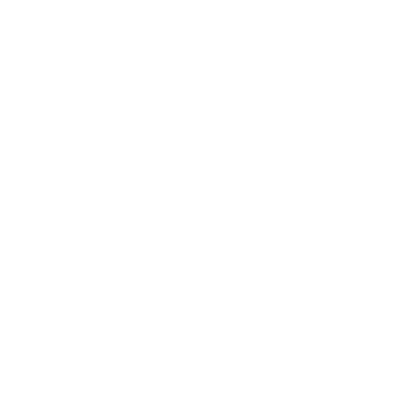
Comprehensive Guide to Isostatic Pressing: Types, Processes, and Features(3)
Isostatic pressing is a versatile manufacturing process that is widely used in various industries. It involves subjecting a material to equal pressure from all directions to achieve uniform density and shape. Isostatic pressing offers numerous advantages, such as the ability to produce complex shapes, uniformity in material properties, and high precision.
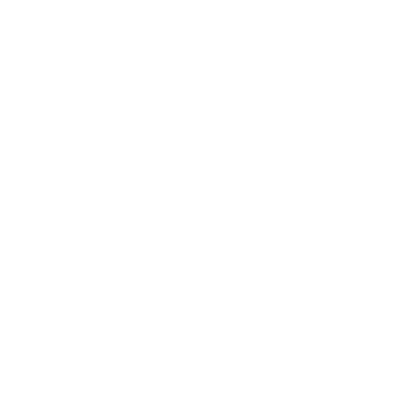
Understanding the Isostatic Pressing Process and its Types
Isostatic pressing, a technique that applies hydrostatic pressure to a material to improve its density and mechanical strength, has seen significant growth and development over the years. Isostatic pressing is commonly used for the consolidation of powders and defect healing of castings, making it a versatile process for a range of materials including ceramics, metals, composites, plastics, and carbon.
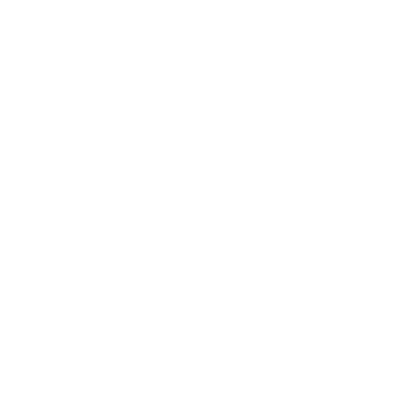
What is Isostatic Pressing Machine
Isostatic molding is a molding method that uses the incompressibility of a liquid medium and the uniform transfer of pressure. It is suitable for powder dense parts with equal pressure in all directions. The principle is to fill the mold with a liquid medium, such as water, and then subject the mold to uniform pressure. The pressure is applied by a piston or a flexible membrane.
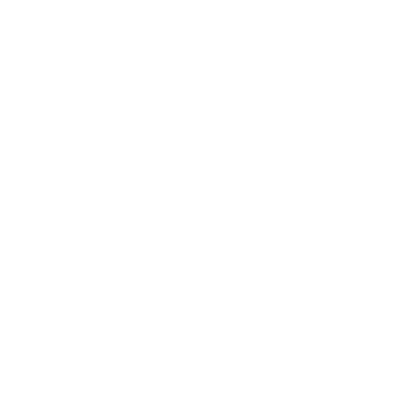
The Benefits of Using Isostatic Pressing in Manufacturing
sostatic pressing is a manufacturing process that involves applying uniform pressure to a material to achieve a specific shape or density. The process can be performed at room temperature (cold isostatic pressing or CIP) or at high temperatures (hot isostatic pressing or HIP).
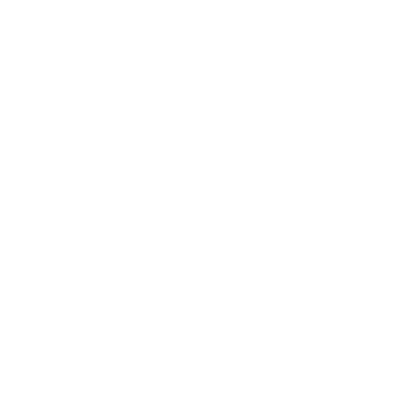
Understanding the Basics of Isostatic Pressing
Isostatic pressing is a manufacturing process used to shape and consolidate materials by applying equal pressure from all directions. The technique involves placing a material in a pressure vessel and applying hydrostatic pressure to the material.
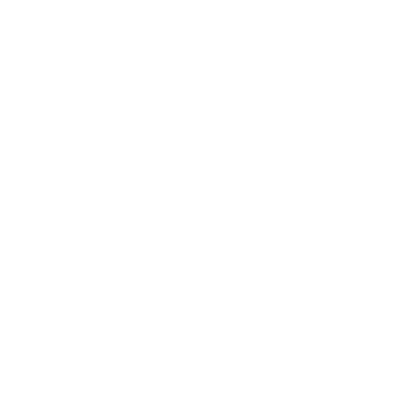
Comprehensive Guide to Isostatic Pressing Molds: Types, Processes, and Applications
Explore the detailed world of isostatic pressing molds, including types like wet bag and dry bag, their processes, and applications. Learn how these molds ensure uniform density and high-strength products.