High-Pressure Reactors
Applications
High-pressure reactors are indispensable tools in the realm of chemical research, particularly when dealing with extreme conditions. These specialized reactors are meticulously designed to withstand and facilitate high-temperature and high-pressure chemical reactions, making them ideal for handling materials that pose significant risks.
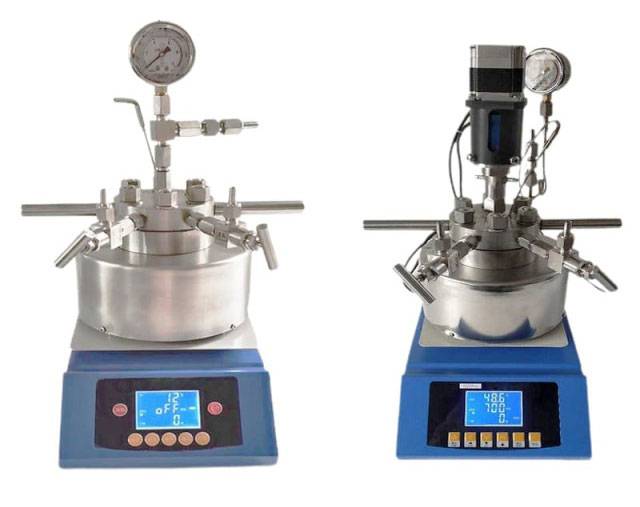
Specifically, high-pressure reactors are crucial for experiments involving flammable, explosive, and toxic media. Their robust construction ensures safety and efficiency, allowing researchers to manipulate these hazardous substances without compromising on experimental integrity. This capability is particularly valuable in industries such as petrochemicals, pharmaceuticals, and specialty chemicals, where the need for precise control over reaction conditions is paramount.
Moreover, the versatility of high-pressure reactors extends beyond safety. They are equipped to handle a wide range of chemical processes, from simple to complex, enabling a broad spectrum of applications. Whether it's synthesizing new compounds, optimizing reaction pathways, or studying reaction kinetics, high-pressure reactors provide the necessary environment to achieve desired outcomes.
In summary, high-pressure reactors are not just tools; they are essential components in advancing chemical research and industrial processes, offering both safety and functionality in the most challenging environments.
Glass Reactors
Functionality
Glass reactors are designed with a double-layer glass construction, which is crucial for handling a variety of reaction materials. This unique design allows for versatile operation, including stirring under both normal and negative pressure conditions. The double-layer glass not only provides transparency for monitoring reactions but also ensures a stable environment by facilitating constant temperature control. This is achieved through the integration of heating and cooling systems, which can maintain precise temperature regulation throughout the reaction process.
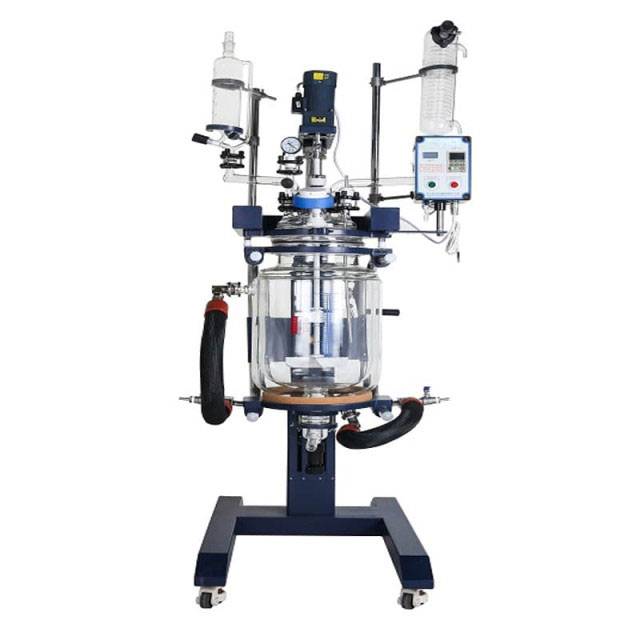
In addition to temperature control, the double-layer glass construction offers enhanced safety features. The outer layer of glass serves as a protective barrier, reducing the risk of accidental exposure to hazardous materials. This design is particularly advantageous when dealing with sensitive or volatile compounds, as it minimizes the potential for leaks and spills.
The functionality of glass reactors extends beyond basic stirring and temperature control. They are also equipped with advanced features such as automated pressure regulation and programmable control systems. These features enable researchers to conduct complex reactions with high precision and reproducibility, making glass reactors an indispensable tool in modern laboratories.
Magnetic Reactors
Sealing Mechanism
Magnetic reactors employ a sophisticated static sealing structure that integrates a magnetic coupler. This design is pivotal in mitigating leakage issues, thereby ensuring an entirely sealed working environment. The magnetic coupler acts as a non-contact transmission device, facilitating the transfer of torque and motion without direct physical contact. This feature is particularly advantageous in handling hazardous materials, where even minute leaks can compromise experimental integrity and safety.
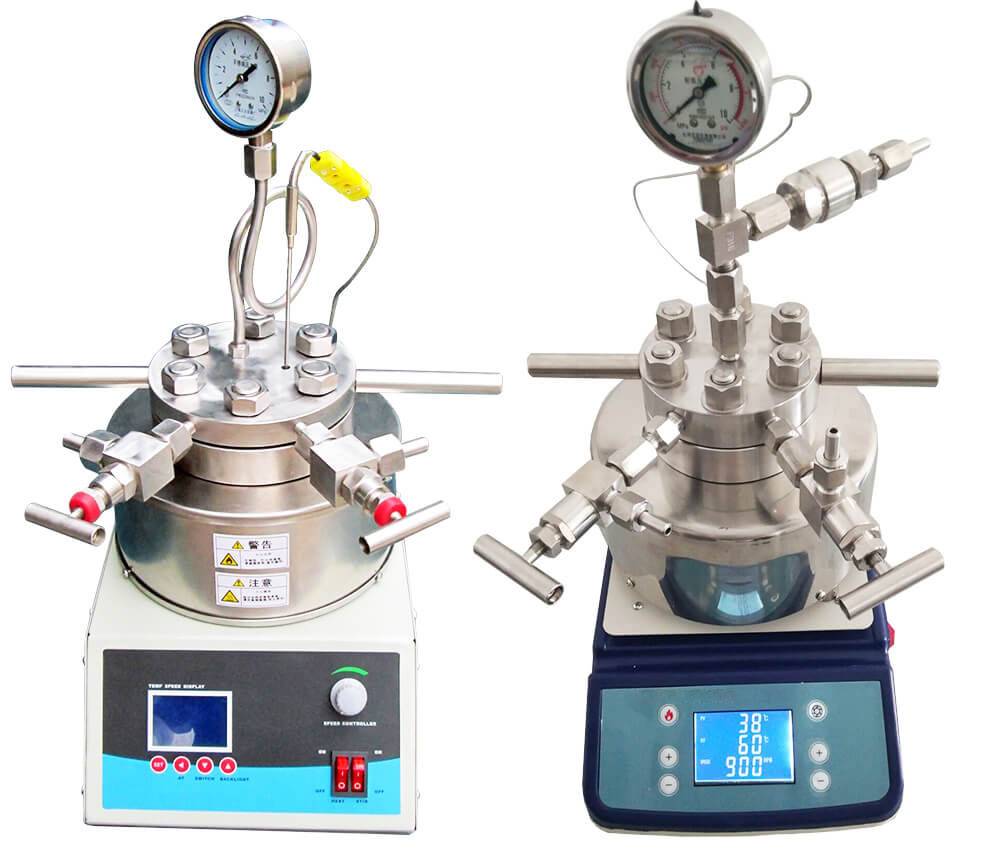
The static sealing mechanism operates on the principle of magnetic fields, which interact with the reactor's internal components to enable smooth operation without the need for mechanical seals. This approach not only enhances the reactor's durability but also simplifies maintenance procedures. By eliminating the need for frequent seal replacements, the overall operational cost is reduced, making magnetic reactors a cost-effective choice for laboratories.
Moreover, the complete sealing ensures that the reaction environment remains pristine, free from external contaminants that could alter the reaction outcomes. This level of environmental control is crucial for experiments requiring precise conditions, such as those involving toxic or explosive media. The magnetic coupler's efficiency in maintaining a sealed environment underscores the reactor's suitability for high-stakes research and development activities.
Microwave Synthesizers
Catalytic Reactions
Microwave synthesizers are instrumental in catalyzing a wide array of reactions across various domains, including organic chemistry, pharmaceuticals, and biochemistry. These synthesizers leverage the unique properties of microwaves to enhance reaction rates and yields, making them indispensable tools in modern laboratories.
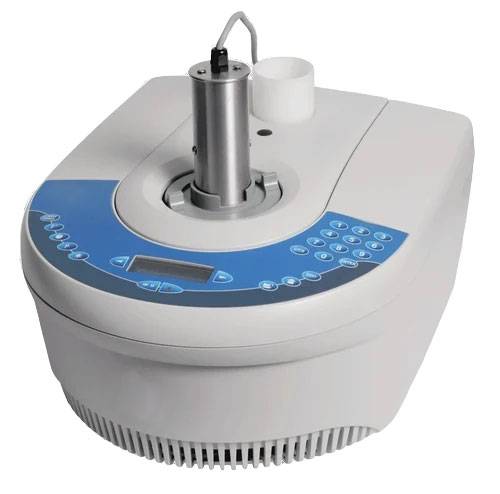
One of the key advantages of microwave synthesizers is their ability to facilitate complex organic reactions. These reactions often require precise control over temperature and pressure, conditions that microwaves can provide efficiently. For instance, the synthesis of pharmaceuticals often involves intricate molecular transformations that benefit from the rapid and uniform heating provided by microwaves.
In the realm of biochemistry, microwave synthesizers are employed to catalyze reactions involving biomolecules. These reactions can be particularly challenging due to the sensitivity of biological materials to heat and other environmental factors. The controlled heating and rapid reaction times offered by microwaves help to minimize degradation and maximize product purity.
Beyond chemical reactions, microwave synthesizers also play a crucial role in physical processes such as solvent extraction. This technique is widely used in the extraction of valuable compounds from complex mixtures, a process that can be significantly accelerated and optimized using microwave energy.
In summary, microwave synthesizers are versatile tools that extend their catalytic capabilities across a spectrum of scientific disciplines, enhancing both the efficiency and effectiveness of laboratory research and development.
Reaction Calorimeters
Measurement
Reaction calorimeters are indispensable tools in the laboratory, designed to measure the heat released or absorbed during chemical reactions or physical processes. This measurement is crucial for gaining insights into the field of thermochemistry and kinetics, which are essential for understanding the energy changes and reaction rates involved in various processes.
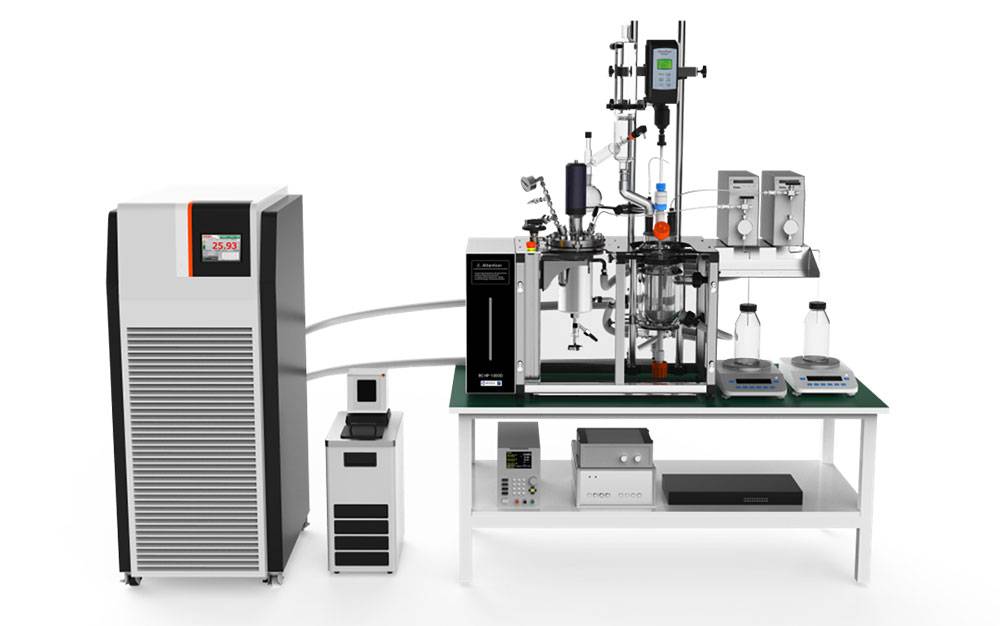
The data collected from reaction calorimeters can be used to analyze the thermodynamic properties of reactions, such as enthalpy and entropy changes, which are fundamental to predicting reaction outcomes and optimizing reaction conditions. Additionally, the kinetic parameters derived from these measurements, such as activation energy and reaction order, provide valuable information for process control and scale-up.
Measurement Parameter | Thermochemistry Insight | Kinetics Insight |
---|---|---|
Heat Release/Absorption | Enthalpy Change | Reaction Rate |
Temperature Change | Entropy Change | Activation Energy |
By monitoring the heat flow, researchers can also identify potential hazards, such as exothermic reactions that could lead to runaway reactions or overheating, thereby ensuring safer laboratory practices. The integration of calorimetric data with other analytical techniques enhances the overall understanding of complex reaction systems, making reaction calorimeters an essential component of modern chemical research and development.
Catalyst Evaluation Devices
Evaluation Principles
Catalyst evaluation devices simulate real-world reaction conditions to assess the efficiency of catalysts. This assessment is primarily based on metrics derived from the reaction products, which are meticulously analyzed to gauge the effectiveness of the catalyst. These evaluation methods are broadly categorized into two types: static and dynamic.
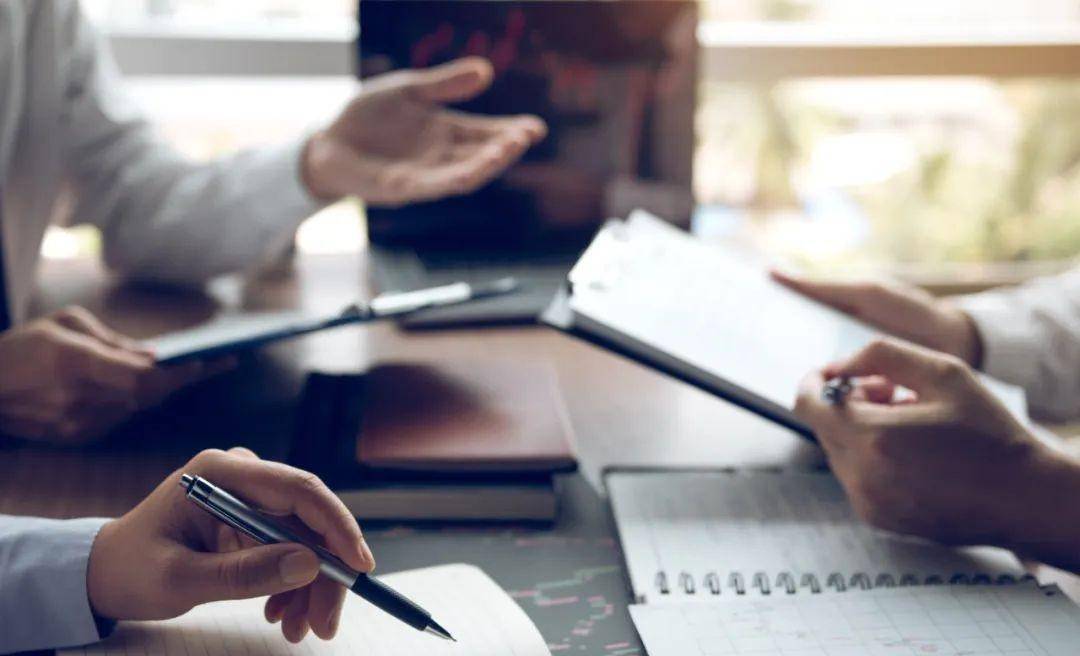
Static Evaluation involves setting up a controlled environment where the reaction conditions remain constant throughout the experiment. This method is particularly useful for studying the initial activity and selectivity of catalysts under stable conditions. Key parameters such as temperature, pressure, and reactant concentrations are fixed, allowing for a detailed analysis of the catalyst's performance without the interference of fluctuating variables.
Dynamic Evaluation, on the other hand, mimics more realistic industrial settings where reaction conditions are subject to change. This approach evaluates how well a catalyst can maintain its efficiency under varying conditions, such as fluctuating temperatures or changing reactant concentrations. Dynamic evaluation is crucial for predicting the long-term performance and stability of catalysts in continuous processes, providing insights that static evaluation alone cannot offer.
Evaluation Type | Key Features | Application |
---|---|---|
Static | Controlled, constant conditions | Initial activity and selectivity studies |
Dynamic | Variable conditions | Long-term performance and stability in continuous processes |
Both static and dynamic evaluation methods are essential for a comprehensive assessment of catalyst efficiency, ensuring that the chosen catalyst is optimized for the specific reaction conditions it will encounter in practical applications.
Synthesis Workstations
Automation
Fully automated synthesis reactors, controlled by advanced computer systems, are revolutionizing the field of compound and drug research. These sophisticated machines handle a myriad of processes with precision and efficiency, including feeding, heating, stirring, and distillation. The automation not only enhances the reproducibility and accuracy of experiments but also reduces the risk of human error, which is particularly crucial in delicate and high-stakes research environments.
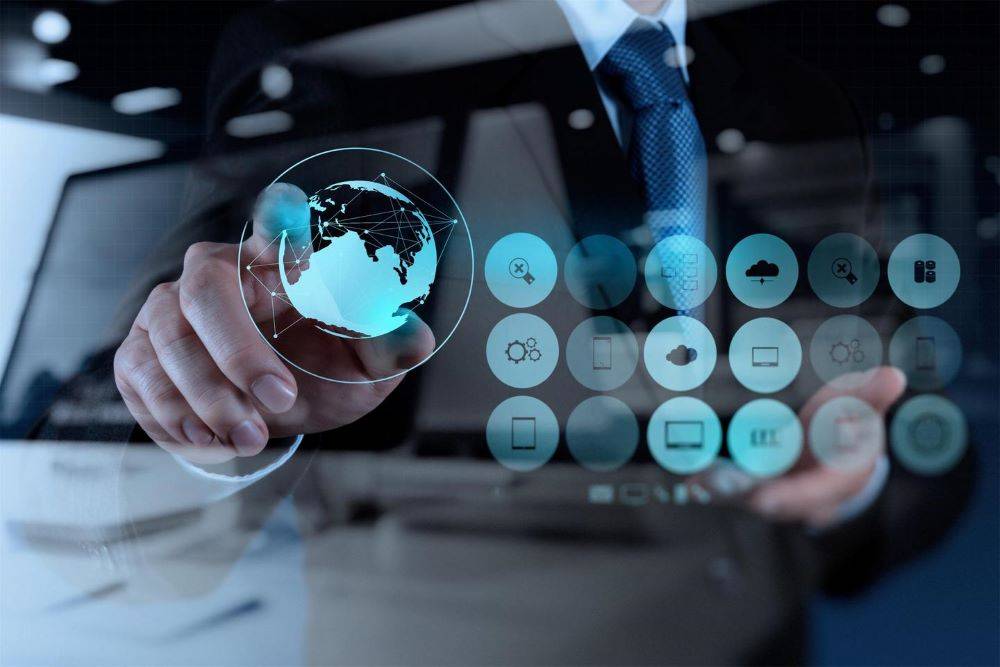
One of the key advantages of these automated systems is their ability to manage complex sequences of operations without manual intervention. This capability is particularly beneficial in synthesizing intricate compounds where the slightest deviation can lead to significant variations in the final product. The computer-controlled systems ensure that each step is executed with the exact parameters predefined by the researchers, thereby maintaining consistency across multiple runs.
Moreover, the automation allows for continuous operation, which can significantly speed up the research process. Researchers can set up experiments to run overnight or over weekends, maximizing the use of laboratory time. This continuous operation is facilitated by the robust design of the reactors, which are built to withstand extended periods of use without compromising on performance.
In addition to their operational benefits, automated synthesis reactors also contribute to safety in the laboratory. By handling hazardous processes like heating and distillation, these systems minimize the exposure of researchers to potentially dangerous chemicals and conditions. This not only protects the health and safety of the research team but also ensures compliance with stringent laboratory safety regulations.
The integration of computer control also enables real-time monitoring and data logging, providing researchers with valuable insights into the reaction dynamics. This data can be used to optimize reaction conditions, identify inefficiencies, and refine the synthesis process. The ability to analyze and adjust in real-time is a significant advancement that can lead to more efficient and effective research outcomes.
In summary, the advent of fully automated synthesis reactors represents a pivotal shift in the way compound and drug research is conducted. By leveraging computer-controlled precision, these systems enhance reproducibility, accelerate research timelines, improve safety, and provide valuable data for process optimization. As the technology continues to evolve, its impact on the field of chemical synthesis is set to grow, paving the way for new discoveries and innovations.
CONTACT US FOR A FREE CONSULTATION
KINTEK LAB SOLUTION's products and services have been recognized by customers around the world. Our staff will be happy to assist with any inquiry you might have. Contact us for a free consultation and talk to a product specialist to find the most suitable solution for your application needs!