Physical Vapor Deposition (PVD) is indeed a versatile technique capable of depositing thin films ranging from nanometer to micrometer thicknesses. This method involves vaporizing a solid material in a vacuum environment and then condensing it onto a substrate to form a thin film. PVD is widely used in various industries, including optics, electronics, and coatings, due to its ability to produce highly durable, corrosion-resistant, and temperature-tolerant films. The process is highly controllable, allowing for precise thicknesses and uniformity, making it suitable for applications requiring nanometer-scale precision as well as micrometer-thick coatings.
Key Points Explained:
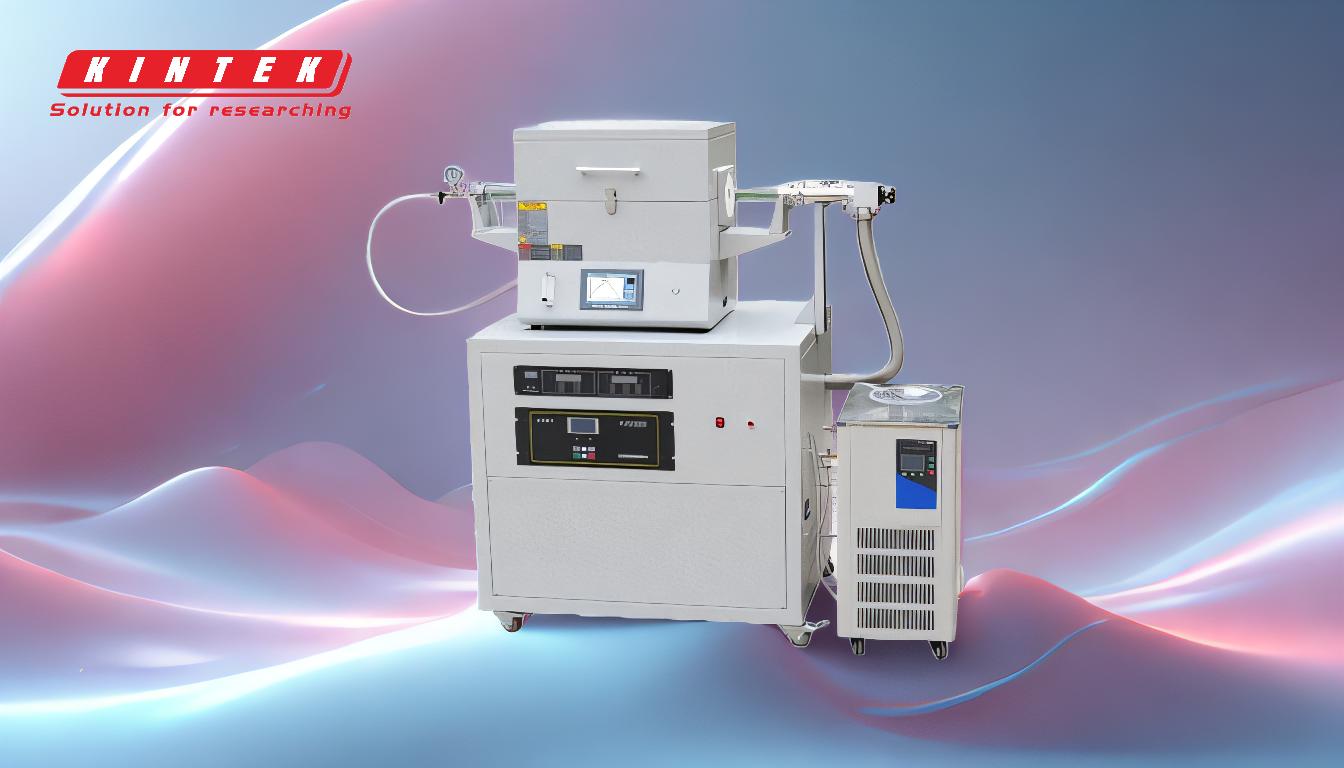
-
PVD Process Overview:
- PVD involves the vaporization of a solid material in a low-pressure chamber, followed by its deposition onto a substrate.
- The process is conducted in a vacuum to ensure a clean and controlled environment, which is crucial for achieving high-quality thin films.
-
Thickness Range:
- PVD can deposit films ranging from a few nanometers to several micrometers in thickness.
- The thickness can be precisely controlled by adjusting parameters such as deposition time, power, and substrate temperature.
-
Applications in Optics:
- In optics, PVD is used to create highly sophisticated mirrors and specially coated glasses.
- Protective, reflective, or absorbing layers can be deposited on glass sheets, lenses, or prisms, which are essential for modern high-tech optics such as laser components and optical instruments.
-
Advantages of PVD:
- Durability: PVD coatings are highly durable and resistant to wear, corrosion, and high temperatures.
- Precision: The process allows for precise control over film thickness and uniformity, making it suitable for applications requiring nanometer-scale precision.
- Versatility: PVD can be used to deposit a wide range of materials, including metals, ceramics, and composites.
-
Comparison with CVD:
- While PVD is a physical process involving vaporization and condensation, Chemical Vapor Deposition (CVD) involves chemical reactions between precursors to form a thin film.
- CVD typically requires higher temperatures compared to PVD, although advanced techniques like microwave plasma chemical vapor deposition can enable deposition at lower temperatures.
-
Industrial Relevance:
- PVD is widely used in industries requiring high-performance coatings, such as aerospace, automotive, and electronics.
- The ability to deposit thin films with precise thicknesses and excellent adhesion makes PVD a preferred choice for many high-tech applications.
In summary, PVD is a highly effective and versatile technique for depositing thin films with thicknesses ranging from nanometers to micrometers. Its ability to produce durable, high-quality coatings with precise control over thickness and uniformity makes it suitable for a wide range of applications, particularly in industries requiring advanced materials and coatings.
Summary Table:
Aspect | Details |
---|---|
Process Overview | Vaporization of solid material in a vacuum, condensing onto a substrate. |
Thickness Range | Nanometer to micrometer scale, with precise control over thickness. |
Applications | Optics, electronics, aerospace, automotive, and coatings. |
Advantages | Durable, corrosion-resistant, temperature-tolerant, and highly precise. |
Comparison with CVD | PVD is a physical process; CVD involves chemical reactions at higher temps. |
Interested in PVD for your applications? Contact us today to learn more!