Yes, titanium can be sintered. Sintering is a viable method for processing titanium, and various sintering techniques can be applied depending on the desired properties and applications. The sintering process involves heating titanium powder to a temperature below its melting point, allowing the particles to bond and form a solid structure. This process is influenced by factors such as temperature, pressure, and the sintering environment, which can significantly impact the final material properties.
Key Points Explained:
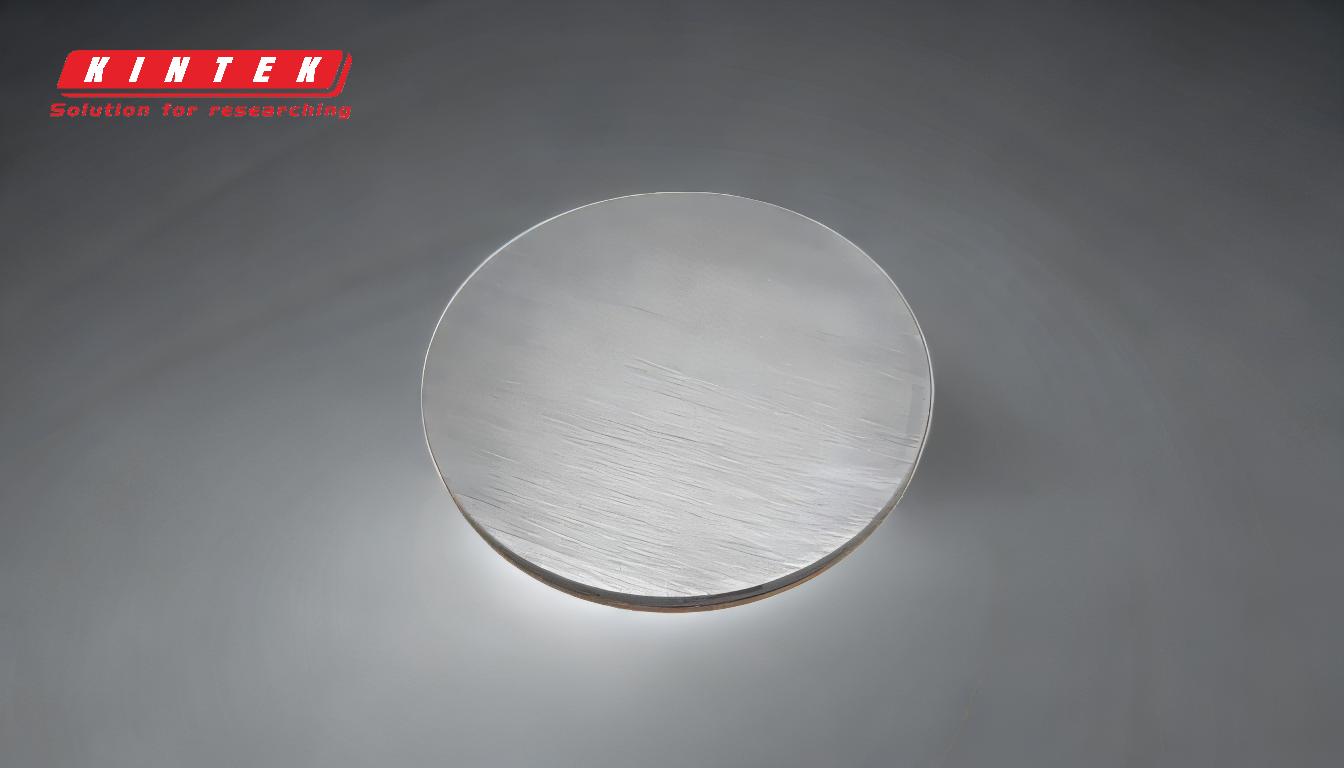
-
Sintering Methods for Titanium:
- Conventional Sintering: This is the most basic form of sintering, where titanium powder is heated in a furnace at high temperatures. The process relies on thermal energy to cause the particles to bond.
- Spark Plasma Sintering (SPS): SPS is an advanced sintering technique that uses pulsed electric currents to rapidly heat the titanium powder. This method allows for faster sintering times and can produce materials with fine microstructures and enhanced mechanical properties.
- Microwave Sintering: This method uses microwave energy to heat the titanium powder. It is known for its rapid heating rates and uniform heating, which can lead to improved material properties.
- Pressure-Assisted Sintering: Techniques such as hot press sintering and hot isostatic pressing (HIP) combine heat with applied pressure to enhance densification and reduce porosity in the sintered titanium.
-
Impact of Sintering on Microstructure and Properties:
- Grain Size and Pore Size: The sintering process directly affects the grain size and pore size in the titanium microstructure. Smaller grain sizes and reduced porosity generally lead to improved mechanical properties such as strength and durability.
- Phase Formation: During sintering, especially in methods like SPS, uncontrolled cooling can lead to the formation of undesirable phases, such as the ω-phase in titanium. This phase can negatively impact the mechanical properties of the material.
-
Specialized Sintering Techniques:
- Selective Laser Sintering (SLS): SLS is an additive manufacturing technique that uses a laser to selectively sinter titanium powder layer by layer. This method is particularly useful for creating complex, three-dimensional titanium components with high precision.
- Electron Beam Sintering (EBS): Similar to SLS, EBS uses an electron beam to sinter titanium powder. This method is also used in additive manufacturing and can produce high-quality titanium parts with complex geometries.
-
Sintering Environments:
- Vacuum Sintering: Sintering titanium in a vacuum environment helps to prevent oxidation and contamination, leading to higher purity and better mechanical properties.
- Atmosphere Sintering: This involves sintering in a controlled atmosphere, such as argon or nitrogen, to protect the titanium from reacting with oxygen or other gases during the sintering process.
-
Applications of Sintered Titanium:
- Medical Implants: Sintered titanium is widely used in medical implants due to its excellent biocompatibility, strength, and corrosion resistance.
- Aerospace Components: The high strength-to-weight ratio and durability of sintered titanium make it ideal for aerospace applications, where lightweight and strong materials are essential.
- Industrial Parts: Sintered titanium is also used in various industrial applications, including automotive components and chemical processing equipment, where its resistance to corrosion and high temperatures is beneficial.
In conclusion, titanium can indeed be sintered using a variety of methods, each offering unique advantages and influencing the final properties of the material. The choice of sintering technique depends on the specific requirements of the application, such as the desired mechanical properties, microstructure, and complexity of the final product.
Summary Table:
Aspect | Details |
---|---|
Sintering Methods | Conventional, Spark Plasma (SPS), Microwave, Pressure-Assisted (HIP, Hot Press) |
Impact on Properties | Grain size, pore size, phase formation (e.g., ω-phase) |
Specialized Techniques | Selective Laser Sintering (SLS), Electron Beam Sintering (EBS) |
Sintering Environments | Vacuum, Controlled Atmosphere (Argon, Nitrogen) |
Applications | Medical implants, aerospace components, industrial parts |
Interested in titanium sintering solutions? Contact our experts today to learn more!