Yes, Diamond-Like Carbon (DLC) can be applied to aluminum and its alloys. DLC coatings are highly versatile and are used to enhance the functional properties of aluminum, such as hardness, wear resistance, and low friction, while maintaining its lightweight and corrosion-resistant characteristics. This makes DLC-coated aluminum suitable for applications in industries like automotive, machinery, and biomedical prostheses. The deposition process, such as RF-PECVD (Radio Frequency Plasma-Enhanced Chemical Vapor Deposition), allows for the coating to be applied at relatively low temperatures, preventing distortion of the aluminum substrate. Below, the key points are explained in detail.
Key Points Explained:
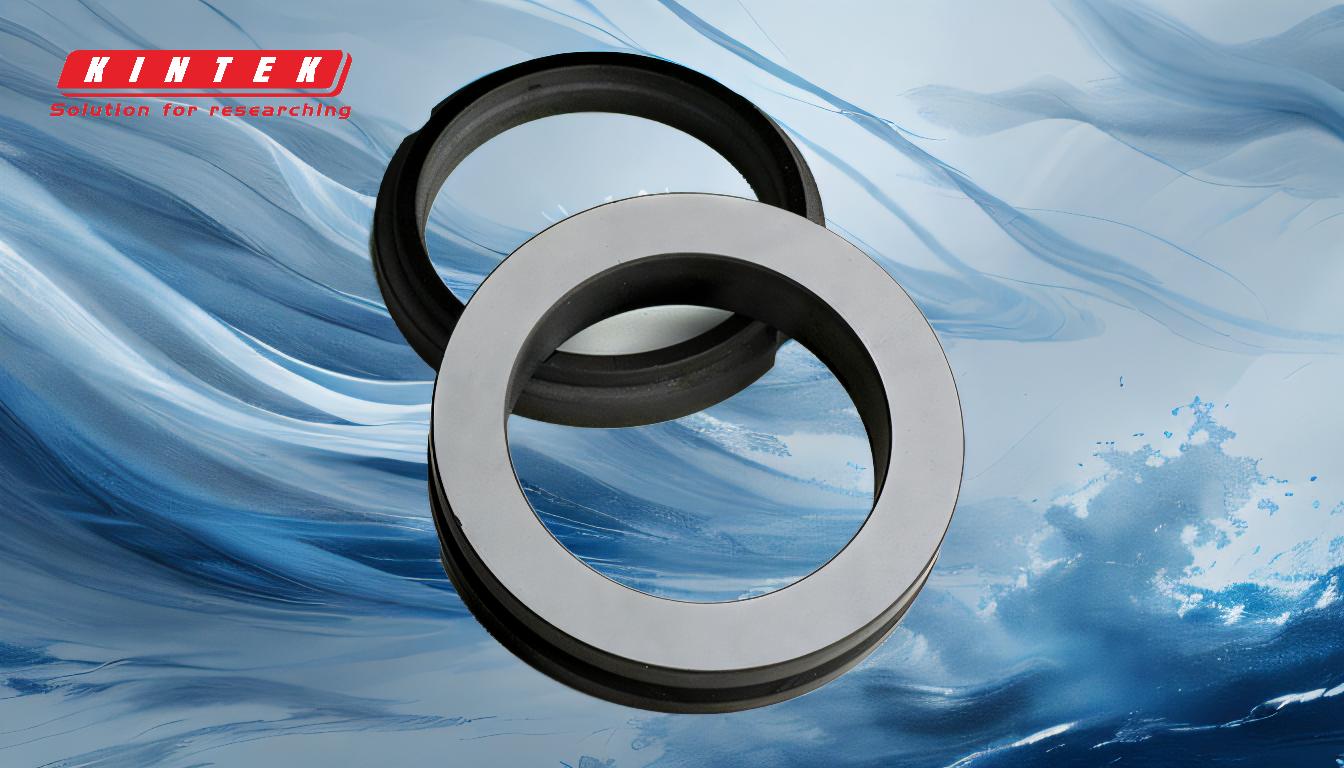
-
What is DLC?
- Diamond-Like Carbon (DLC) is an amorphous carbon coating that combines the hardness of diamond with the lubricity of graphite.
- It is a metastable form of amorphous carbon or hydrogenated amorphous carbon, containing a significant fraction of sp3 bonds, which determine its properties.
- DLC coatings are known for their high hardness (1500–3000 HV), low coefficient of friction, chemical resistance, and biocompatibility.
-
Why Apply DLC to Aluminum?
- Aluminum is lightweight, corrosion-resistant, and widely used in industries like automotive, aerospace, and machinery. However, it has relatively low hardness and wear resistance.
- DLC coatings enhance aluminum's surface properties, making it more durable, scratch-resistant, and suitable for high-performance applications.
- Applications include automobile pistons, bores, VCR heads, copier machine drums, and textile machinery components.
-
Deposition Methods for DLC on Aluminum
-
RF-PECVD (Radio Frequency Plasma-Enhanced Chemical Vapor Deposition):
- This method is commonly used for depositing DLC on aluminum substrates.
- It operates at relatively low temperatures, which is crucial for preventing thermal distortion of aluminum.
- The process is scalable, fast, and produces coatings with good adhesion and uniformity.
- Other methods, such as sputtering or ion beam deposition, can also be used but may require more complex equipment.
-
RF-PECVD (Radio Frequency Plasma-Enhanced Chemical Vapor Deposition):
-
Advantages of DLC on Aluminum
- Enhanced Hardness and Wear Resistance: DLC coatings significantly improve the surface hardness of aluminum, making it suitable for high-wear applications.
- Low Friction: The low coefficient of friction reduces energy losses in moving parts, making DLC-coated aluminum ideal for automotive and machinery components.
- Chemical Resistance: DLC provides a protective barrier against corrosive environments, extending the lifespan of aluminum components.
- Biocompatibility: DLC-coated aluminum is suitable for biomedical applications, such as prostheses and implants.
-
Challenges and Considerations
- Adhesion: Ensuring strong adhesion between DLC and aluminum can be challenging due to differences in thermal expansion coefficients. Pre-treatment processes, such as surface cleaning or intermediate layers, may be required.
- Thickness Control: Precise control of DLC film thickness is necessary for applications like optical sensing or antireflective coatings.
- Cost: The deposition process can be expensive, especially for large-scale industrial applications.
-
Applications of DLC-Coated Aluminum
- Automotive Industry: Used in pistons, bores, camshafts, and bearings to reduce friction and improve fuel efficiency.
- Machinery: Enhances the performance of textile machinery components and copier machine drums.
- Biomedical: Suitable for prostheses and implants due to its biocompatibility and wear resistance.
- Optical and Sensing Applications: DLC-coated aluminum is used in antireflective coatings and optical sensing systems where precise control of thickness and refractive index is required.
-
Future Prospects
- Ongoing research aims to improve the adhesion and scalability of DLC coatings on aluminum.
- Advances in deposition technologies, such as PECVD, are expected to make the process more cost-effective and accessible for industrial applications.
- The combination of aluminum's lightweight properties with DLC's functional enhancements opens up new possibilities for energy-efficient and high-performance components.
In summary, DLC coatings can be successfully applied to aluminum, offering significant improvements in hardness, wear resistance, and friction properties. While challenges like adhesion and cost remain, the benefits make DLC-coated aluminum a promising material for a wide range of industrial and biomedical applications.
Summary Table:
Key Aspect | Details |
---|---|
What is DLC? | Amorphous carbon coating with diamond-like hardness and graphite-like lubricity. |
Why Apply DLC to Aluminum? | Enhances hardness, wear resistance, and friction properties while maintaining lightweight and corrosion resistance. |
Deposition Method | RF-PECVD (low-temperature process) for uniform, scalable coatings. |
Advantages | High hardness, low friction, chemical resistance, and biocompatibility. |
Applications | Automotive, machinery, biomedical prostheses, and optical sensing. |
Challenges | Adhesion, thickness control, and cost. |
Interested in DLC-coated aluminum for your applications? Contact us today to learn more!