Carburizing is a heat treatment process that significantly enhances the hardness of steel by introducing carbon into its surface layer. This process creates a hard, wear-resistant exterior while maintaining a softer, more ductile core, making it ideal for applications requiring both strength and flexibility. The added carbon increases surface hardness, improves abrasion resistance, and enhances fatigue strength, ensuring the steel can withstand demanding mechanical conditions. Below, we explore the key aspects of how carburizing hardens steel and its implications for material performance.
Key Points Explained:
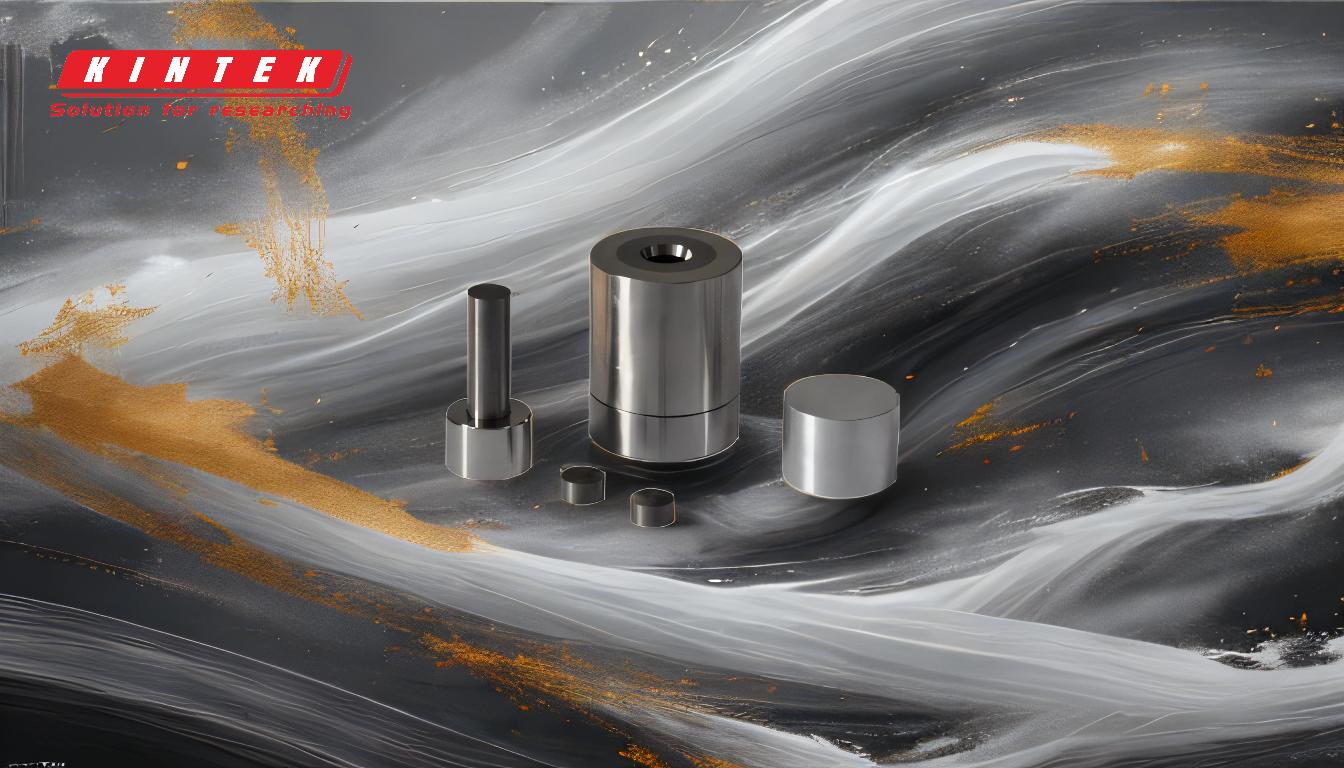
-
What is Carburizing?
- Carburizing is a surface-hardening process that involves diffusing carbon into the surface layer of low-carbon steel.
- The process typically occurs at high temperatures (850°C to 950°C) in a carbon-rich environment, such as an endothermic atmosphere.
- The carbon atoms penetrate the steel's surface, creating a carbon-enriched layer that can be hardened through subsequent heat treatment, such as quenching.
-
How Does Carburizing Harden Steel?
- Carbon Diffusion: During carburizing, carbon atoms migrate into the steel's surface, increasing the carbon concentration in the outer layer.
- Formation of Martensite: After carburizing, the steel is rapidly cooled (quenched), transforming the carbon-rich surface layer into martensite, a hard and brittle microstructure.
- Hardness Gradient: The process creates a hardness gradient, with the surface being significantly harder than the core, which remains soft and ductile.
-
Benefits of Carburized Steel
- Surface Hardness: The carburized layer exhibits high hardness, making it resistant to wear and abrasion.
- Ductile Core: The core retains its original properties, providing toughness and resistance to fracture.
- Improved Fatigue Strength: The hardened surface enhances the steel's ability to withstand cyclic loading, reducing the risk of fatigue failure.
- Enhanced Wear Resistance: The carbon-rich surface layer is highly resistant to wear, making it suitable for components subjected to friction and mechanical stress.
-
Applications of Carburized Steel
- Carburizing is widely used in industries requiring components with high surface hardness and a tough core, such as:
- Automotive: Gears, crankshafts, and camshafts.
- Aerospace: Landing gear components and engine parts.
- Industrial Machinery: Bearings, shafts, and fasteners.
- These applications benefit from the combination of surface hardness and core ductility, ensuring durability and performance under demanding conditions.
- Carburizing is widely used in industries requiring components with high surface hardness and a tough core, such as:
-
Limitations and Considerations
- Depth of Carburizing: The depth of the carburized layer must be carefully controlled to meet specific application requirements.
- Distortion: The high-temperature process can cause dimensional changes or distortion in the steel, requiring post-treatment machining or grinding.
- Material Selection: Carburizing is most effective on low-carbon steels, as high-carbon steels already have sufficient carbon content for hardening.
-
Comparison with Other Hardening Methods
- Unlike through-hardening, which hardens the entire steel component, carburizing selectively hardens the surface, preserving the core's ductility.
- Compared to nitriding, which introduces nitrogen instead of carbon, carburizing provides a deeper hardened layer and is more suitable for high-load applications.
In conclusion, carburizing is a highly effective method for hardening steel by enriching its surface with carbon. This process creates a hard, wear-resistant exterior while maintaining a tough and ductile core, making it ideal for applications requiring both strength and flexibility. By understanding the principles and benefits of carburizing, manufacturers can optimize the performance and longevity of steel components in various industries.
Summary Table:
Aspect | Details |
---|---|
Process | Diffuses carbon into low-carbon steel at 850°C to 950°C in a carbon-rich environment. |
Hardening Mechanism | Forms martensite through quenching, creating a hard surface and ductile core. |
Benefits | High surface hardness, improved wear resistance, and enhanced fatigue strength. |
Applications | Automotive (gears, crankshafts), aerospace (landing gear), and industrial machinery (bearings, shafts). |
Limitations | Requires precise depth control; may cause distortion; effective only on low-carbon steels. |
Discover how carburizing can enhance your steel components—contact our experts today for tailored solutions!