PVD-coated stainless steel is highly resistant to tarnishing due to its durable and protective coating. The PVD (Physical Vapor Deposition) process creates a thin ceramic layer on the stainless steel surface, enhancing its resistance to corrosion, oxidation, and environmental factors. This makes PVD stainless steel ideal for applications requiring both aesthetic appeal and durability, such as jewelry, architectural elements, and industrial components. The coating not only preserves the stainless steel's inherent resistance to staining but also adds a layer of protection against scratches and abrasions, ensuring long-lasting color and finish.
Key Points Explained:
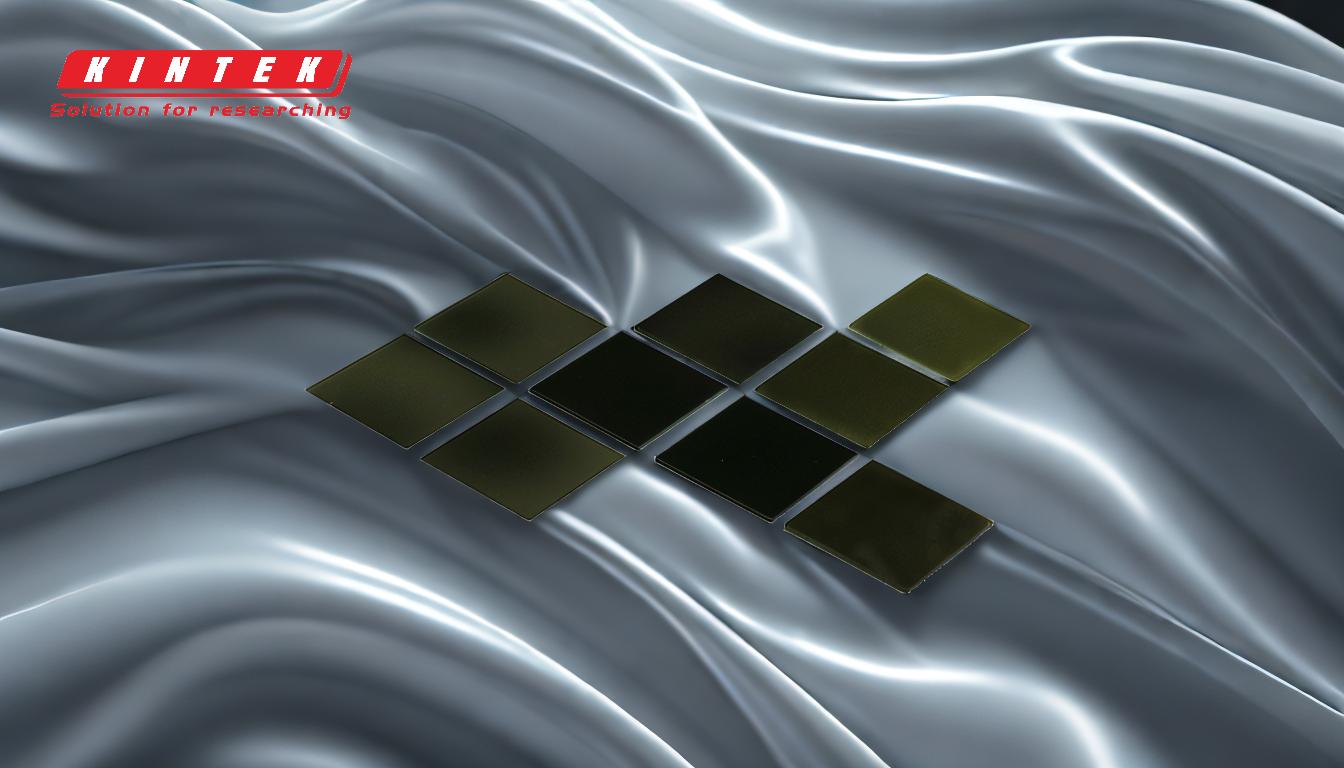
-
What is PVD Coating?
- PVD (Physical Vapor Deposition) is a process that applies a thin ceramic coating to the surface of stainless steel.
- The coating is extremely thin, ranging from 0.5 to 5 microns, and is highly resistant to wear and tear.
- It enhances the stainless steel's properties, such as corrosion resistance, durability, and aesthetic appearance.
-
Why PVD Coating Prevents Tarnishing
- PVD coatings act as a protective barrier against environmental factors like moisture, oxidation, and chemicals, which are common causes of tarnishing.
- The coating is highly resistant to corrosion and oxidation, ensuring the stainless steel retains its appearance over time.
- The thin ceramic layer is difficult to remove, providing long-lasting protection.
-
Enhanced Durability and Scratch Resistance
- PVD coatings improve the stainless steel's resistance to scratches and abrasions, which can expose the underlying material to tarnishing.
- The hardness of the coating, determined by the substrate material, plays a crucial role in its durability.
-
Aesthetic Benefits of PVD Coating
- PVD coatings can replicate the original finish of materials while adding vibrant colors like gold, rose gold, black, and blue.
- These colors are available in polished, satin, or matte finishes, depending on the surface polish of the product.
- The coating ensures the color remains vibrant and resistant to fading or discoloration.
-
Applications of PVD-Coated Stainless Steel
- PVD-coated stainless steel is widely used in jewelry, architectural elements, and industrial components due to its durability and aesthetic appeal.
- In industries like food and beverage, where cleanliness and sanitation are essential, PVD-coated stainless steel is ideal due to its enhanced resistance to staining and corrosion.
-
Comparison with Uncoated Stainless Steel
- While stainless steel itself is resistant to corrosion and staining, PVD coating further enhances these properties, making it even more durable and tarnish-resistant.
- The coating ensures the stainless steel maintains its appearance and functionality in harsh environments.
In conclusion, PVD-coated stainless steel is highly resistant to tarnishing due to the protective and durable nature of the PVD coating. This makes it an excellent choice for applications requiring both aesthetic appeal and long-lasting performance.
Summary Table:
Key Feature | Description |
---|---|
PVD Coating Process | Thin ceramic layer (0.5–5 microns) applied via Physical Vapor Deposition. |
Tarnishing Resistance | Protects against moisture, oxidation, and chemicals, preventing tarnish. |
Durability & Scratch Resistance | Enhances resistance to scratches and abrasions, ensuring long-lasting finish. |
Aesthetic Benefits | Adds vibrant colors (gold, rose gold, black, blue) with polished or matte finishes. |
Applications | Jewelry, architecture, industrial components, and food/beverage industries. |
Discover how PVD-coated stainless steel can elevate your projects—contact us today for expert advice!