Pyrolysis reactors are heated using various methods, depending on the type of reactor and the desired outcomes of the pyrolysis process. The primary methods include direct heat exchange using solid heat carriers or hot gas streams, indirect heat exchange through reactor walls or built-in tubes/plates, and partial combustion within the reactor. These methods are tailored to specific reactor designs, such as fluidized bed, fixed bed, rotary cylinder, and cyclonic reactors, which can operate in batch or continuous systems. The choice of heating method influences the efficiency, temperature control, and product yields of the pyrolysis process.
Key Points Explained:
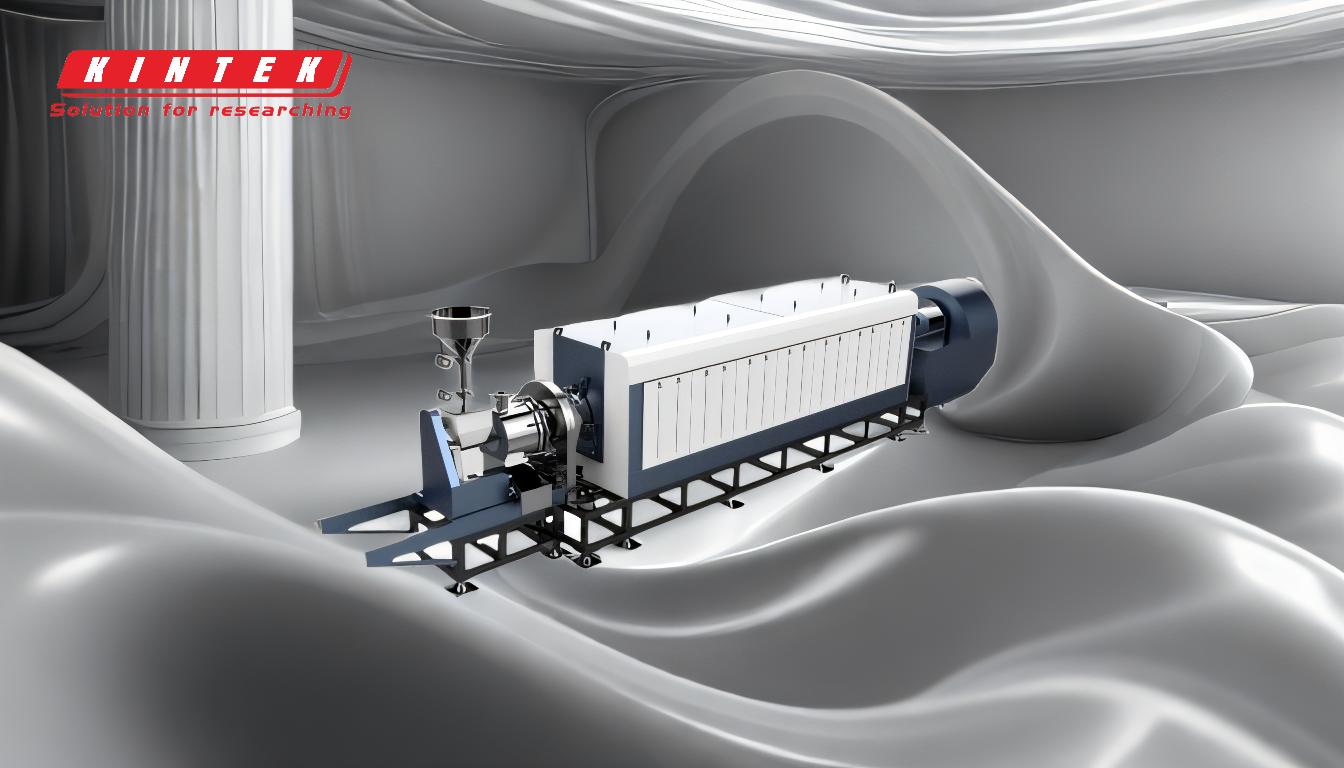
-
Direct Heat Exchange:
- Solid Heat Carriers: In this method, materials like sand or other inert solids are heated externally and then introduced into the reactor to transfer heat directly to the biomass. This is particularly effective in fluidized bed reactors, where the solid particles ensure uniform heat distribution and rapid heating.
- Hot Gas Streams: Hot gases, often inert combustion gases, are circulated through the reactor to provide heat. This method is commonly used in continuous systems, where the gases can be recycled to maintain consistent temperatures.
-
Indirect Heat Exchange:
- Reactor Walls: Heat is supplied through the walls of the reactor, which are heated externally. This method is often used in fixed bed and rotary cylinder reactors, where the heat transfer is controlled to prevent overheating and ensure uniform pyrolysis.
- Built-in Tubes/Plates: Some reactors are equipped with internal tubes or plates that carry hot fluids (such as steam or thermal oil) to provide indirect heating. This method allows for precise temperature control and is suitable for processes requiring specific thermal profiles.
-
Partial Combustion:
- Internal Combustion: Partial combustion of the biomass or other materials within the reactor generates heat directly. This method is used in some batch systems, such as charcoal kilns, where part of the biomass is burned to provide the necessary heat for pyrolysis.
- Oxygen Control: In fluidized bed reactors, the process is often divided into zones with different oxygen concentrations. The bed section operates under low oxygen conditions for pyrolysis, while the free section introduces additional air for combustion, ensuring complete burning of gases.
-
Reactor Types and Heating Methods:
- Fluidized Bed Reactors: These reactors use solid heat carriers or hot gas streams for direct heat exchange. They are highly efficient for fast pyrolysis, where rapid heating and short residence times are required.
- Fixed Bed Reactors: Typically use indirect heating through reactor walls or built-in tubes. These are suitable for slower pyrolysis processes, where controlled heating is necessary.
- Rotary Cylinder and Cyclonic Reactors: These reactors often employ indirect heating methods, such as heated walls or internal tubes, to ensure uniform heat distribution and prevent localized overheating.
-
Batch vs. Continuous Systems:
- Batch Systems: Often rely on partial combustion or external heating methods. These systems are simpler but less efficient than continuous systems.
- Continuous Systems: Utilize direct or indirect heat exchange methods to maintain consistent temperatures and high efficiencies. These systems are more complex but offer better control over the pyrolysis process and higher throughput.
-
Specialized Pyrolysis Techniques:
- Fast Pyrolysis: Requires rapid heating, often achieved through direct heat exchange with solid heat carriers or hot gas streams. This method is used to maximize liquid yields.
- Ablative Pyrolysis: Involves direct contact between the biomass and a heated surface, providing intense localized heating. This technique is used in specialized reactors to achieve high heating rates.
In summary, the heating methods for pyrolysis reactors are diverse and tailored to the specific requirements of the reactor design and the desired pyrolysis outcomes. Direct and indirect heat exchange methods, along with partial combustion, provide the necessary thermal energy to drive the pyrolysis process efficiently. The choice of heating method impacts the reactor's performance, product yields, and overall process efficiency.
Summary Table:
Heating Method | Description | Reactor Type |
---|---|---|
Direct Heat Exchange | Uses solid heat carriers or hot gas streams for rapid, uniform heating. | Fluidized bed reactors |
Indirect Heat Exchange | Heat supplied through reactor walls or built-in tubes/plates for precise control. | Fixed bed, rotary cylinder |
Partial Combustion | Generates heat by burning part of the biomass or materials within the reactor. | Batch systems, charcoal kilns |
Ready to optimize your pyrolysis process? Contact our experts today for tailored solutions!