Thin films are created through a variety of deposition techniques, which can be broadly categorized into physical, chemical, and electrically-based methods. These techniques allow for precise control over the thickness, composition, and properties of the films, making them suitable for a wide range of applications, from semiconductors to flexible electronics. The most common methods include evaporation, sputtering, chemical vapor deposition (CVD), spin coating, drop casting, and plasma sputtering. Each method has its own advantages and is chosen based on the desired film properties and the application requirements.
Key Points Explained:
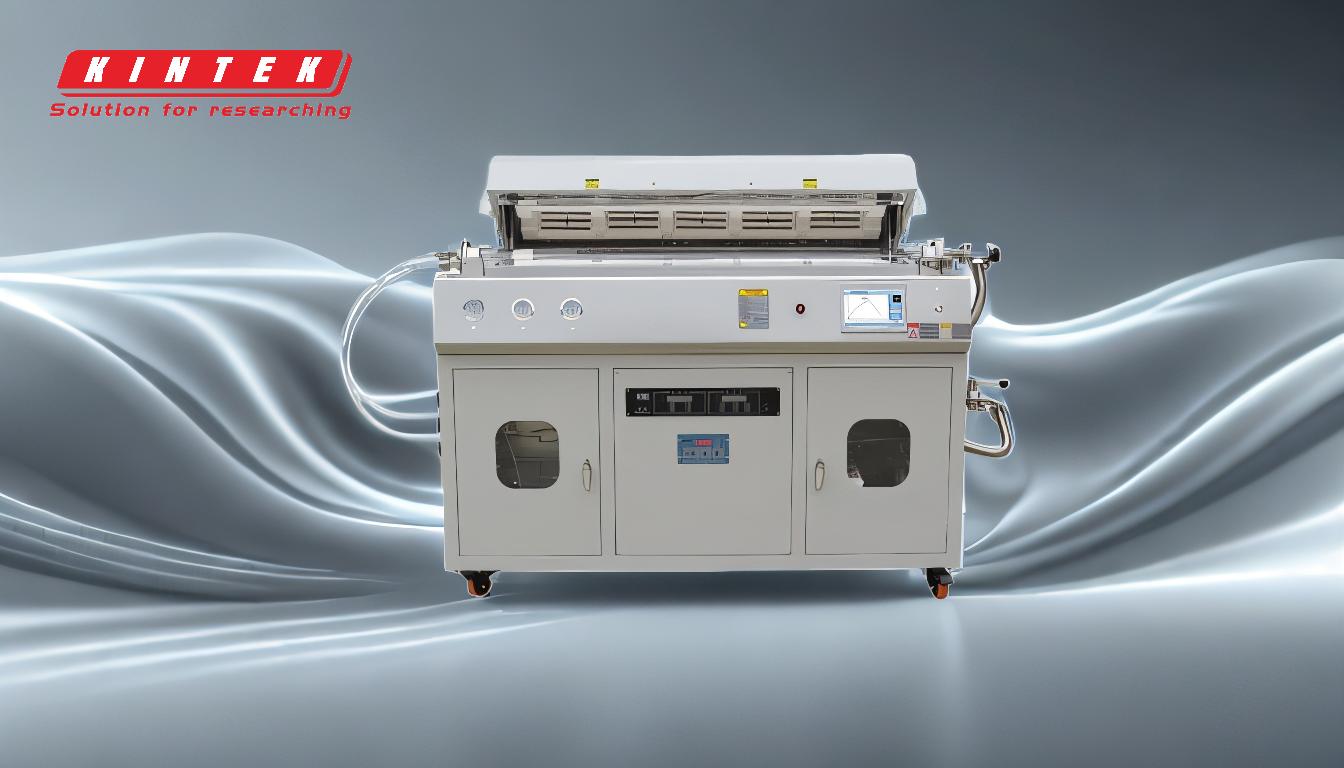
-
Deposition Techniques Overview:
- Physical Methods: These include techniques like evaporation and sputtering, where the material is physically transferred onto a substrate.
- Chemical Methods: Techniques such as chemical vapor deposition (CVD) involve chemical reactions to form the thin film.
- Electrically-Based Methods: These methods, such as plasma sputtering, use electrical energy to deposit materials.
-
Evaporation:
- Process: Material is heated to its evaporation point in a vacuum, and the vapor condenses on a cooler substrate to form a thin film.
- Applications: Commonly used for metals and simple compounds in applications like optical coatings and semiconductor devices.
-
Sputtering:
- Process: A target material is bombarded with high-energy ions, causing atoms to be ejected and deposited onto a substrate.
- Applications: Widely used for depositing metals, alloys, and compounds in microelectronics and decorative coatings.
-
Chemical Vapor Deposition (CVD):
- Process: Chemical precursors are introduced into a reaction chamber, where they react or decompose to form a solid film on the substrate.
- Applications: Essential for producing high-quality, uniform films in semiconductor manufacturing and protective coatings.
-
Spin Coating:
- Process: A liquid precursor is applied to a substrate, which is then spun at high speeds to spread the material into a thin, uniform layer.
- Applications: Commonly used in the production of photoresists, organic electronics, and polymer films.
-
Drop Casting:
- Process: A solution containing the material is dropped onto a substrate and allowed to dry, forming a thin film.
- Applications: Simple and cost-effective method for creating films in research and small-scale applications.
-
Plasma Sputtering:
- Process: Similar to conventional sputtering but uses plasma to enhance the deposition process, allowing for better control over film properties.
- Applications: Used in advanced applications like flexible solar cells and OLEDs.
-
Oil Bathing:
- Process: Involves immersing a substrate in a liquid containing the material, which then forms a thin film upon removal and drying.
- Applications: Less common but used in specialized applications where uniform coatings are required.
-
Control and Precision:
- Thickness Control: All these methods allow for precise control over the thickness of the film, down to the level of single atoms in some cases.
- Composition Control: The composition of the film can be finely tuned by adjusting the deposition parameters, such as temperature, pressure, and precursor concentration.
-
Applications:
- Semiconductors: Early commercial success with silicon-based thin films.
- Flexible Electronics: Newer methods focus on polymer compounds for flexible solar cells and OLEDs.
- Optical Coatings: Used in lenses, mirrors, and other optical components to enhance performance.
By understanding these key points, a purchaser can make informed decisions about which deposition method and material are best suited for their specific application, ensuring optimal performance and cost-effectiveness.
Summary Table:
Method | Process | Applications |
---|---|---|
Evaporation | Material heated to evaporate, condenses on substrate | Optical coatings, semiconductor devices |
Sputtering | High-energy ions bombard target, ejecting atoms onto substrate | Microelectronics, decorative coatings |
CVD | Chemical precursors react/decompose to form solid film | Semiconductor manufacturing, protective coatings |
Spin Coating | Liquid precursor spun at high speed to form uniform layer | Photoresists, organic electronics, polymer films |
Drop Casting | Solution dropped onto substrate, dried to form film | Research, small-scale applications |
Plasma Sputtering | Plasma-enhanced sputtering for better control over film properties | Flexible solar cells, OLEDs |
Oil Bathing | Substrate immersed in liquid, dried to form film | Specialized applications requiring uniform coatings |
Need help choosing the right thin film deposition method for your application? Contact our experts today!