To increase the efficiency of a ball mill, several factors must be optimized, including the grindability of the material, the size and proportion of grinding media, the filling rate of the mill, and operational parameters such as rotation speed and grinding density. By addressing these factors, the grinding process can be made more efficient, leading to better productivity and reduced energy consumption. Key strategies include adjusting the feed size, optimizing the steel ball size and filling rate, maintaining appropriate grinding density, and ensuring proper mill design and operational conditions.
Key Points Explained:
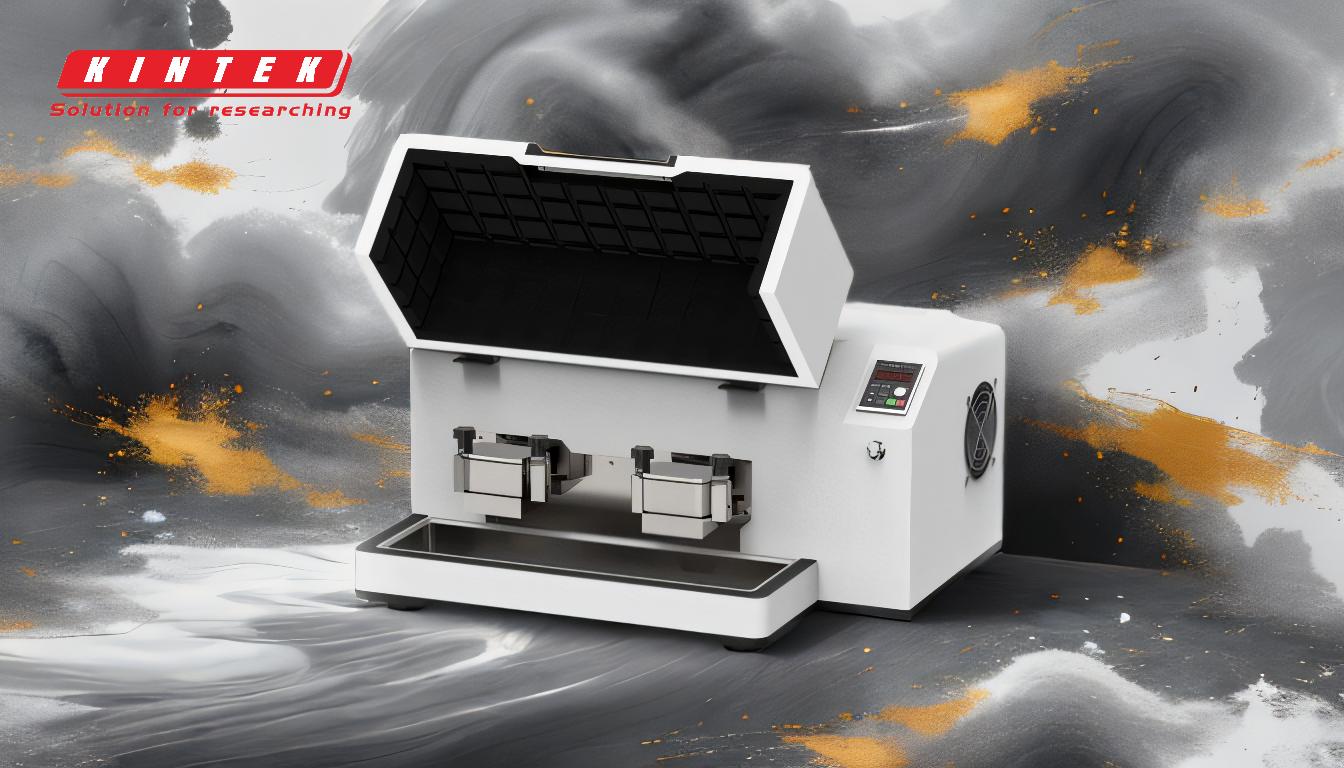
-
Change the Original Grindability
- Grindability refers to how easily a material can be ground. Some materials naturally grind more efficiently than others. By pre-treating or altering the material (e.g., through chemical or thermal processes), its grindability can be improved, leading to more efficient milling.
-
More Crushing and Less Grinding
- Reducing the feed size before it enters the ball mill can significantly improve efficiency. Larger particles require more energy to grind, so pre-crushing the material to a smaller size reduces the workload on the mill and enhances productivity.
-
Reasonable Filling Rate of Steel Balls
- The filling rate of steel balls (the percentage of the mill volume occupied by grinding media) must be optimized. Too few balls reduce grinding efficiency, while too many can lead to excessive energy consumption and wear. A filling rate of around 30-40% is often optimal.
-
Reasonable Size and Proportion of Steel Balls
- The size and proportion of steel balls directly impact grinding efficiency. Larger balls are better for coarse grinding, while smaller balls are more effective for fine grinding. A balanced mix of ball sizes ensures efficient grinding across different particle sizes.
-
Accurate Refilling of Steel Balls
- Over time, steel balls wear down and need to be replaced. Regularly refilling the mill with the correct size and proportion of balls ensures consistent grinding performance and prevents inefficiencies caused by worn or missing balls.
-
Appropriate Grinding Density
- The grinding density (the concentration of solid material in the slurry) affects the efficiency of the grinding process. Too high a density can lead to clogging, while too low a density reduces the impact of the grinding media. Maintaining an optimal density ensures efficient grinding and prevents operational issues.
-
Optimize Mill Design (L:D Ratio)
- The length-to-diameter (L:D) ratio of the mill is critical for efficiency. An optimal L:D ratio (typically 1.56–1.64) ensures proper material flow and grinding action, maximizing productivity.
-
Control Rotation Speed
- The rotation speed of the mill affects the grinding action. Too slow a speed reduces the impact of the grinding media, while too high a speed can cause the balls to centrifuge, reducing grinding efficiency. The critical speed (the speed at which the balls begin to centrifuge) should be carefully managed.
-
Monitor Feed Rate and Level
- The feed rate and level in the mill must be controlled to ensure consistent grinding. Overloading the mill can reduce efficiency, while underloading can lead to uneven grinding and increased wear.
-
Timely Removal of Ground Product
- Ensuring that ground material is removed promptly prevents over-grinding and reduces energy consumption. Efficient discharge mechanisms and proper mill design are essential for maintaining productivity.
By addressing these factors, the efficiency of a ball mill can be significantly improved, leading to better grinding performance, reduced energy consumption, and lower operational costs.
Summary Table:
Key Factor | Optimization Strategy |
---|---|
Grindability | Pre-treat materials to improve grindability through chemical or thermal processes. |
Feed Size | Reduce feed size through pre-crushing to enhance milling efficiency. |
Filling Rate of Steel Balls | Maintain a filling rate of 30-40% for optimal grinding efficiency. |
Steel Ball Size & Proportion | Use a balanced mix of ball sizes for coarse and fine grinding. |
Refilling Steel Balls | Regularly replace worn balls to maintain consistent grinding performance. |
Grinding Density | Maintain optimal slurry density to prevent clogging or reduced grinding impact. |
Mill Design (L:D Ratio) | Optimize length-to-diameter ratio (1.56–1.64) for proper material flow and grinding. |
Rotation Speed | Control speed to avoid centrifuging and ensure effective grinding action. |
Feed Rate & Level | Monitor feed rate to prevent overloading or underloading the mill. |
Ground Product Removal | Remove ground material promptly to prevent over-grinding and energy waste. |
Ready to optimize your ball mill efficiency? Contact our experts today for tailored solutions!