Making XRF (X-ray Fluorescence) pellets is a meticulous process that ensures accurate and reliable analytical results. The process involves grinding the sample to a fine particle size, mixing it with a binder or grinding aid, pressing the mixture into a pellet using a die, and applying high pressure to form a solid, homogeneous pellet. This method improves the signal-to-noise ratio, enhances the detection of lighter elements, and eliminates discrepancies in elemental composition, making it superior to loose powder analysis. The ideal particle size for the sample is less than 50µm, and the use of a binder in a 20%-30% ratio ensures the pellet's integrity and homogeneity.
Key Points Explained:
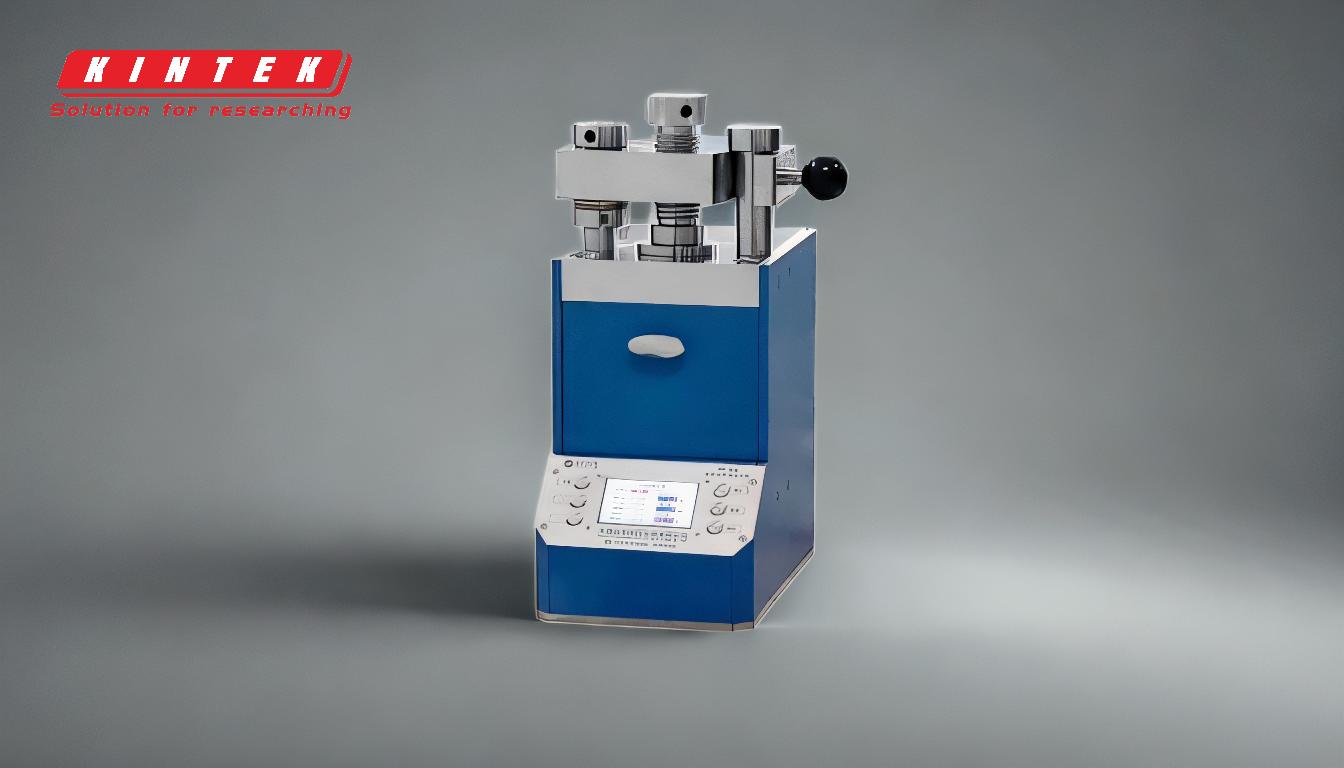
-
Grinding the Sample to a Fine Particle Size:
- The first step in making XRF pellets is grinding the sample to achieve a fine particle size. The ideal particle size is less than 50µm, though less than 75µm is acceptable.
- Fine particle size is crucial because it ensures homogeneity in the pellet, which directly impacts the accuracy of the XRF analysis. Larger particles can lead to inconsistencies in the sample, causing discrepancies in the results.
-
Mixing with a Binder or Grinding Aid:
- After grinding, the sample is mixed with a binder or grinding aid. A common binder used is a cellulose wax mixture.
- The binder is typically added in a ratio of 20%-30% relative to the sample. This helps in binding the particles together during the pressing process, ensuring the pellet maintains its shape and integrity.
- The binder also aids in reducing void spaces within the pellet, which can otherwise lead to inaccuracies in the XRF analysis.
-
Pressing the Mixture in a Die:
- The mixed sample is then poured into a pressing die. The die is designed to shape the sample into a pellet form.
- The pressing process involves applying high pressure, typically between 15 and 35 tons (20-30T is commonly used). This high pressure compacts the sample and binder mixture, forming a solid, dense pellet.
- The pressure applied must be sufficient to ensure the pellet is homogeneous and free from voids, which are critical for accurate XRF analysis.
-
Advantages of Pressed Pellets Over Loose Powder:
- Pressed pellets offer a higher signal-to-noise ratio compared to loose powder, which is particularly beneficial for detecting lighter elements.
- Discrepancies in elemental composition that are often observed with loose powder samples are eliminated when using pressed pellets. This ensures more accurate quantification of elements in the sample.
- The homogeneity and lack of void spaces in pressed pellets contribute to more consistent and reliable analytical results.
-
Importance of Homogeneity and Particle Size:
- Homogeneity in the pellet is essential for accurate XRF analysis. Any inconsistency in the sample can lead to errors in the results.
- The particle size of the sample plays a significant role in achieving homogeneity. Smaller particles (ideally <50µm) ensure that the sample is evenly distributed throughout the pellet, leading to more accurate and reproducible results.
-
Practical Considerations for Equipment and Consumables:
- Grinding Equipment: High-quality grinding mills or mortars are necessary to achieve the desired particle size.
- Binders: The choice of binder is important. Cellulose wax mixtures are commonly used due to their effectiveness in binding and their compatibility with XRF analysis.
- Pressing Dies and Presses: The die must be of appropriate size and material to withstand the high pressure applied during the pressing process. Hydraulic presses capable of delivering 15-35 tons of pressure are typically used.
- Sample Preparation Tools: Tools for measuring and mixing the sample and binder accurately are essential to maintain the correct ratio and ensure consistency.
By following these steps and considerations, you can produce high-quality XRF pellets that provide accurate and reliable analytical results, making them an essential part of XRF sample preparation.
Summary Table:
Step | Details |
---|---|
Grinding | Achieve particle size <50µm (ideally) or <75µm (acceptable). |
Mixing with Binder | Use 20%-30% binder (e.g., cellulose wax) for pellet integrity. |
Pressing in a Die | Apply 15-35 tons of pressure for a dense, homogeneous pellet. |
Advantages | Higher signal-to-noise ratio, better light element detection, no voids. |
Equipment | Grinding mills, hydraulic presses, and precise measurement tools required. |
Need help preparing XRF pellets? Contact our experts today for tailored solutions!