A three-plate mold is a specialized type of injection molding tool designed to separate the runner system (the channels through which molten plastic flows) from the finished part. This separation is achieved through the use of three distinct plates that open in sequence during the molding process. The primary advantage of a three-plate mold is its ability to automatically eject the runner system and the finished part separately, improving efficiency and reducing waste. This design is particularly useful for complex parts or when using materials that require precise control over the flow of molten plastic. Below, the key points of how a three-plate mold works are explained in detail.
Key Points Explained:
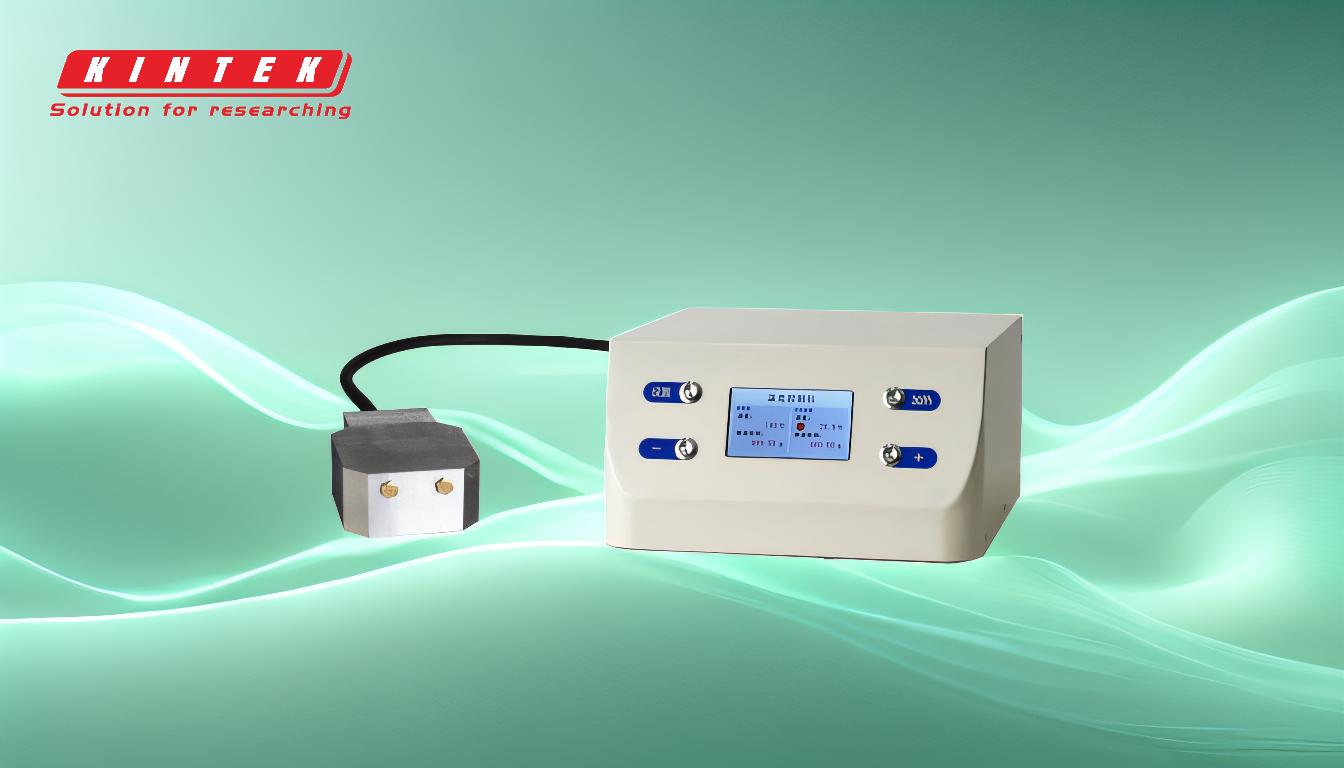
-
Structure of a Three-Plate Mold:
- A three-plate mold consists of three main plates: the stationary plate (closest to the injection unit), the movable plate (connected to the ejection system), and the middle plate (which separates the runner system from the part).
- The runner system is located between the stationary plate and the middle plate, while the cavity for the finished part is between the middle plate and the movable plate.
-
Mold Opening Sequence:
- When the mold opens, it separates into three distinct stages:
- First Stage: The stationary plate and middle plate separate, allowing the runner system to be ejected.
- Second Stage: The middle plate and movable plate separate, enabling the finished part to be ejected.
- This sequential separation ensures that the runner system and the finished part are removed independently.
- When the mold opens, it separates into three distinct stages:
-
Runner System Design:
- The runner system in a three-plate mold is typically a cold runner, meaning it does not remain heated during the molding process.
- The runners are arranged on two planes, with gates (entry points to the cavity) positioned to allow the molten plastic to flow into the part cavity without interference.
-
Ejection Mechanism:
- The runner system is ejected through the first opening between the stationary and middle plates, often using ejector pins or a stripper plate.
- The finished part is ejected through the second opening between the middle and movable plates, typically using ejector pins or air blasts.
-
Advantages of a Three-Plate Mold:
- Automatic Runner Separation: The runner system and finished part are ejected separately, reducing manual handling and improving efficiency.
- Flexibility in Gate Placement: Gates can be positioned at optimal locations on the part, allowing for better control over plastic flow and reducing visible gate marks.
- Suitability for Complex Parts: The design is ideal for parts with intricate geometries or multiple cavities.
-
Applications:
- Three-plate molds are commonly used for producing small, intricate parts, such as electronic components, medical devices, and consumer products.
- They are also preferred for materials that require precise control over the injection process, such as high-performance plastics.
-
Challenges:
- Complexity: The design and operation of a three-plate mold are more complex than a two-plate mold, requiring precise alignment and maintenance.
- Cost: The additional plate and ejection mechanisms increase the cost of the mold.
- Cycle Time: The sequential opening and ejection process can slightly increase the overall cycle time compared to simpler mold designs.
By understanding these key points, equipment and consumable purchasers can better evaluate whether a three-plate mold is the right choice for their specific production needs, balancing the benefits of automation and precision against the higher cost and complexity.
Summary Table:
Aspect | Details |
---|---|
Structure | Three plates: stationary, middle, and movable. Runner system and part cavity separated. |
Opening Sequence | Two stages: runner ejection first, followed by part ejection. |
Runner System | Cold runner design with gates on two planes for optimal plastic flow. |
Ejection Mechanism | Runner ejected via first opening; part ejected via second opening. |
Advantages | Automatic runner separation, flexible gate placement, ideal for complex parts. |
Applications | Small, intricate parts (electronics, medical devices, consumer products). |
Challenges | Higher complexity, increased cost, slightly longer cycle time. |
Ready to optimize your injection molding process? Contact us today to explore how a three-plate mold can meet your production needs!