Catalytic pyrolysis is a thermochemical process that decomposes organic materials, such as biomass or plastic waste, into smaller molecules in the absence of oxygen, using a catalyst to enhance specific chemical reactions. This process involves heating the material above its decomposition temperature, breaking chemical bonds, and producing valuable byproducts like pyrolysis oil (bio-oil), combustible gases, and bio-char. Catalytic pyrolysis can be performed in two ways: in-situ, where the catalyst and feedstock are mixed in a single reactor, and ex-situ, where they are separated in a dual-bed reactor. The catalyst, often a modified natural zeolite, promotes reactions like cracking, depolymerization, and recombination, improving the quality and yield of the desired products. This method is particularly effective for converting plastic waste into liquid oil and other value-added products, making it a sustainable solution for waste management and resource recovery.
Key Points Explained:
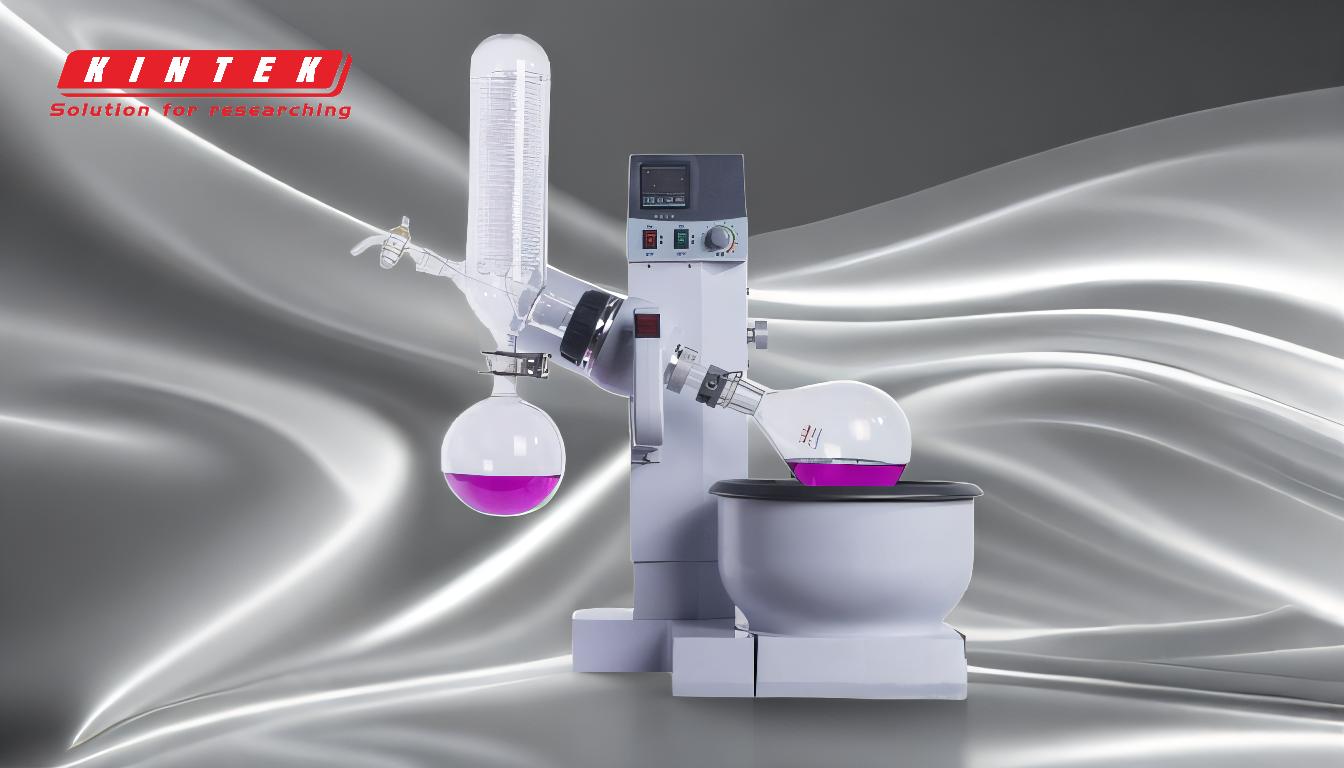
-
Definition and Purpose of Catalytic Pyrolysis:
- Catalytic pyrolysis is a thermochemical decomposition process that breaks down organic materials like biomass or plastic waste into smaller molecules in the absence of oxygen.
- The primary goal is to produce valuable byproducts such as pyrolysis oil (bio-oil), combustible gases, and bio-char.
- The process is enhanced by the use of a catalyst, which promotes specific chemical reactions, improving the efficiency and quality of the end products.
-
Mechanisms of Pyrolysis:
- Primary Mechanism: Involves the release of volatile compounds and the breaking of chemical bonds within the polymers during heating. This results in smaller molecules or residues with larger molecular mass.
- Secondary Mechanism: Includes additional reactions of unstable volatile compounds, such as cracking, recombination, and the formation of secondary char. These reactions are influenced by the presence of a catalyst.
-
Role of the Catalyst:
- The catalyst, often a modified natural zeolite, plays a crucial role in promoting specific types of chemical reactions, such as cracking and depolymerization.
- It helps in converting plastic waste into liquid oil and other value-added products, making the process more efficient and sustainable.
- The catalyst also aids in reducing the formation of unwanted byproducts and improving the quality of the pyrolysis oil.
-
Types of Catalytic Pyrolysis:
- In-Situ Catalytic Pyrolysis: The biomass or plastic waste and the catalyst are mixed together in a single reactor. This method allows for direct interaction between the feedstock and the catalyst, enhancing the reaction efficiency.
- Ex-Situ Catalytic Pyrolysis: The biomass or plastic waste and the catalyst are placed in separate beds within a dual-bed reactor. This method allows for more control over the reaction conditions and can lead to a higher quality of the end products.
-
Process Conditions:
- The process involves heating the material above its decomposition temperature, typically in the range of 400-600°C, in the absence of oxygen.
- The process can be conducted in a vacuum or inert atmosphere to avoid side reactions like combustion or hydrolysis, which can degrade the quality of the byproducts.
- The choice of process conditions, including temperature, heating rate, and catalyst type, significantly affects the yield and composition of the pyrolysis products.
-
Applications and Benefits:
- Catalytic pyrolysis is particularly effective for converting plastic waste into liquid oil, providing a sustainable solution for waste management.
- The process also produces combustible gases and bio-char, which can be used as energy sources or soil amendments, respectively.
- By utilizing a catalyst, the process becomes more efficient, reducing the energy requirements and improving the overall sustainability of the pyrolysis process.
-
Challenges and Considerations:
- The selection of an appropriate catalyst is critical, as it must be effective in promoting the desired reactions while being cost-effective and durable.
- The process conditions must be carefully controlled to maximize the yield and quality of the pyrolysis products.
- There is a need for further research and development to optimize the process and scale it up for industrial applications.
In summary, catalytic pyrolysis is a promising technology for converting organic waste into valuable products, with the catalyst playing a key role in enhancing the efficiency and quality of the process. By understanding the mechanisms, types, and conditions of catalytic pyrolysis, it is possible to optimize the process for various applications, contributing to sustainable waste management and resource recovery.
Summary Table:
Aspect | Details |
---|---|
Process | Thermochemical decomposition of organic materials in the absence of oxygen. |
Key Products | Pyrolysis oil (bio-oil), combustible gases, and bio-char. |
Catalyst Role | Promotes reactions like cracking, depolymerization, and recombination. |
Types | In-situ (single reactor) and ex-situ (dual-bed reactor). |
Temperature Range | 400-600°C in an inert or vacuum atmosphere. |
Applications | Converts plastic waste into liquid oil, produces energy sources, and soil amendments. |
Benefits | Sustainable waste management, improved product quality, and reduced energy requirements. |
Learn how catalytic pyrolysis can transform your waste management strategy—contact us today!