DC sputtering is a widely used physical vapor deposition (PVD) technique for creating thin films on substrates. It operates by applying a direct current (DC) voltage to a metal target in a low-pressure inert gas environment, typically argon. This process ionizes the gas, creating a plasma that bombards the target, ejecting (sputtering) atoms from the target material. These ejected atoms then travel through the vacuum chamber and deposit onto a substrate, forming a thin film. DC sputtering is cost-effective, versatile, and widely used in industries such as semiconductors, optics, and jewelry. Below, the process is broken down into key steps and explained in detail.
Key Points Explained:
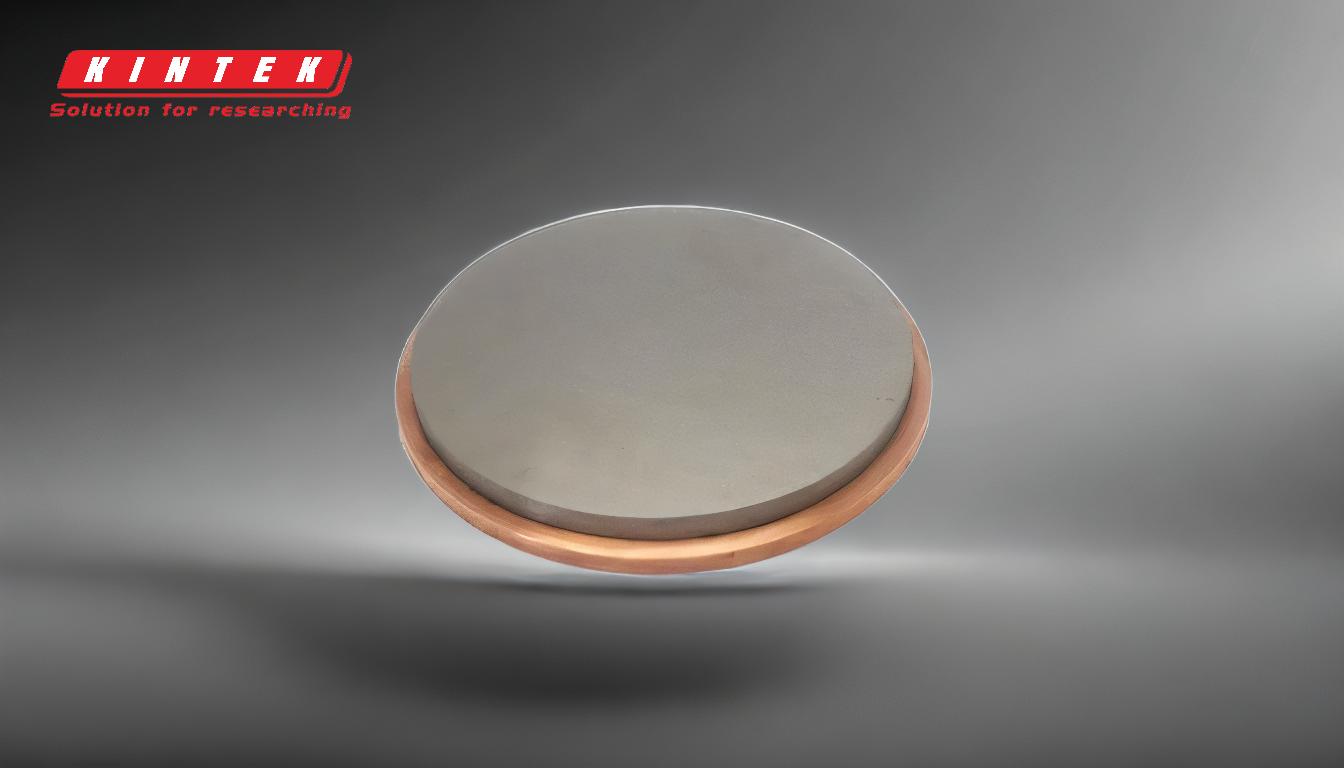
-
Vacuum Chamber Setup:
- The process begins by creating a vacuum in the chamber to eliminate air and other unwanted gases. This ensures precise control over the deposition process and prevents contamination.
- A vacuum environment also allows for uniform deposition of the thin film on the substrate.
-
Introduction of Inert Gas:
- An inert gas, typically argon, is introduced into the vacuum chamber at low pressure.
- Argon is chosen because it is chemically inert, meaning it does not react with the target material or the substrate, ensuring a clean deposition process.
-
Plasma Generation:
- A DC voltage is applied between the target (cathode) and the substrate (anode), creating an electric field.
- This electric field ionizes the argon gas, forming a plasma. In this plasma, argon atoms lose electrons and become positively charged ions.
-
Sputtering of the Target Material:
- The positively charged argon ions are accelerated toward the negatively charged target due to the electric field.
- When these high-energy ions collide with the target surface, they transfer their kinetic energy to the target atoms, causing them to be ejected (sputtered) from the target.
-
Deposition on the Substrate:
- The sputtered target atoms travel through the vacuum chamber and deposit onto the substrate.
- These atoms condense and form a thin, uniform film on the substrate surface. The substrate can be made of various materials, including heat-sensitive ones like plastics, as the sputtered particles have relatively low kinetic energy and do not generate significant heat.
-
Advantages of DC Sputtering:
- Cost-Effective: DC sputtering is one of the most economical PVD techniques, making it accessible for various applications.
- Versatility: It can deposit a wide range of materials, including metals, alloys, and some conductive compounds.
- Low-Temperature Process: The low energy of the sputtered particles allows for coating heat-sensitive substrates without damage.
- Uniformity and Control: The vacuum environment and precise control over gas pressure and voltage enable consistent and high-quality thin films.
-
Applications:
- Semiconductors: Used for depositing conductive layers in integrated circuits.
- Optical Components: Applied in anti-reflective coatings and mirrors.
- Jewelry: Used for decorative coatings, such as gold or silver finishes.
- Other Industries: Includes applications in solar panels, medical devices, and more.
-
Limitations:
- Conductive Targets Only: DC sputtering is limited to conductive materials, as non-conductive targets cannot sustain the electric field required for the process.
- Lower Deposition Rates: Compared to other PVD techniques like magnetron sputtering, DC sputtering may have slower deposition rates.
In summary, DC sputtering is a straightforward and effective method for depositing thin films, particularly for conductive materials. Its simplicity, cost-effectiveness, and ability to work with heat-sensitive substrates make it a popular choice across various industries. However, its limitations, such as the requirement for conductive targets, must be considered when selecting a deposition technique for specific applications.
Summary Table:
Key Aspect | Details |
---|---|
Process | Uses DC voltage to sputter target material in a vacuum chamber. |
Gas Used | Inert gas (typically argon) for plasma generation. |
Advantages | Cost-effective, versatile, low-temperature, and uniform film deposition. |
Applications | Semiconductors, optical components, jewelry, solar panels, medical devices. |
Limitations | Limited to conductive targets; slower deposition rates compared to others. |
Discover how DC sputtering can enhance your thin film processes—contact our experts today!