Electron beam processing is a versatile technology that uses a focused beam of electrons to induce changes in material properties, such as crosslinking polymers or creating thin films. The process occurs in a vacuum, where electrons are manipulated by electric and magnetic fields to form a precise beam. When this beam interacts with materials, it transfers energy, causing physical or chemical changes. Applications range from industrial processes like heat-shrinkable plastics and semiconductor enhancement to food processing and thin-film deposition. The technology offers precision, efficiency, and environmental benefits, making it a valuable tool in various industries.
Key Points Explained:
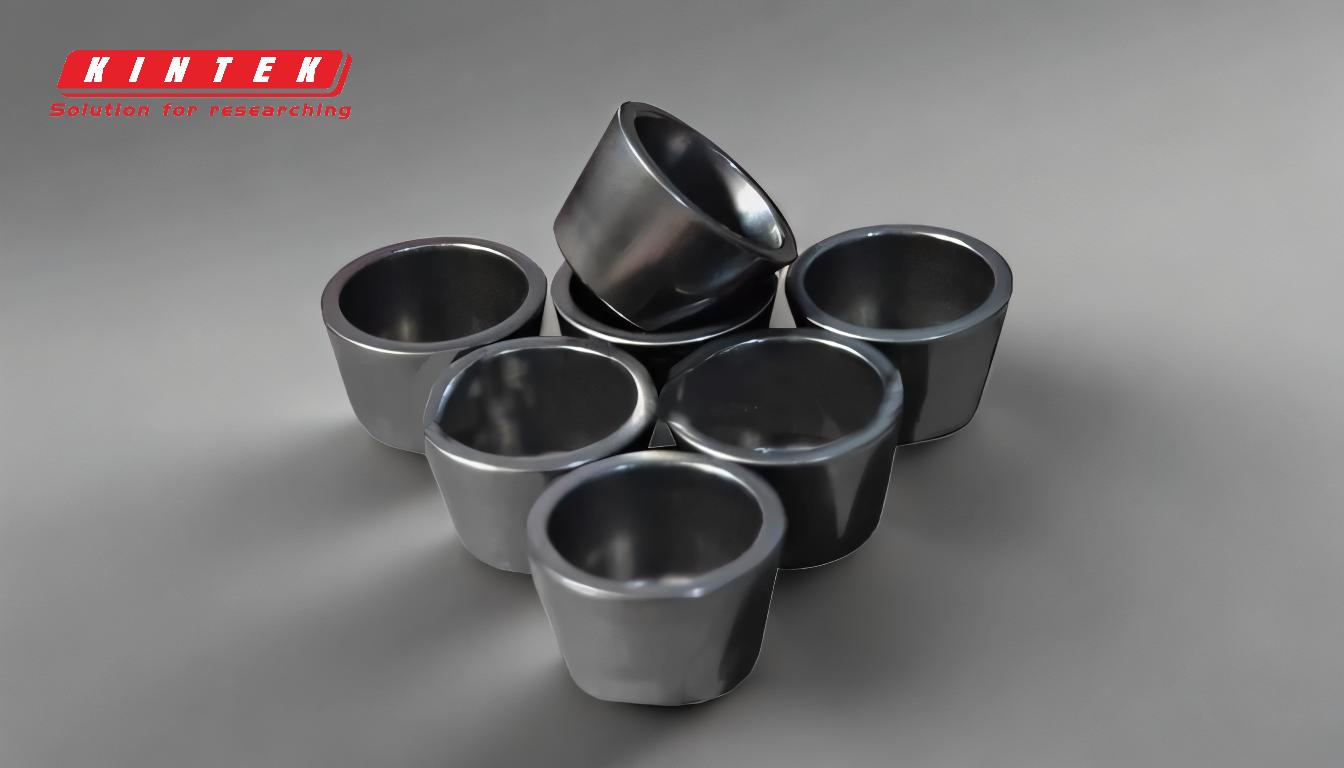
-
Fundamentals of Electron Beam Processing:
- Electron beam processing involves generating a focused beam of electrons in a vacuum environment.
- The electrons are manipulated using electric and magnetic fields to create a fine, controlled beam.
- When the electron beam interacts with solid-state matter, the energy is transferred as heat or kinetic energy, leading to changes in material properties.
-
Energy Transfer and Material Interaction:
- The concentrated energy from the electron beam can induce physical or chemical changes in materials.
- For example, in polymers, the energy can cause crosslinking (strengthening the material) or chain scissioning (breaking molecular bonds).
- This precise energy transfer allows for controlled modifications, making the process highly efficient and adaptable.
-
Applications in Industry:
- Heat-Shrinkable Plastics: Electron beams are used to modify polymers, enabling them to shrink when heated, which is useful in packaging and insulation.
- Thermoset Composite Curing: The technology accelerates the curing process of composites, improving their strength and durability.
- Semiconductor Enhancement: Electron beams are used to modify semiconductor materials, enhancing their electrical properties.
- Food Processing: The beams can sterilize food by eliminating pathogens without the need for chemicals or excessive heat.
- Thin-Film Deposition: Electron beam evaporation is used to deposit thin films of materials onto substrates, crucial in electronics and optics.
-
Electron Beam Coating and Deposition:
- Electron beam coating involves using the beam to heat a material in a vacuum, causing it to evaporate and form a thin film on a substrate.
- This process, known as E-beam evaporation, is a form of physical vapor deposition (PVD) and is widely used in creating coatings for semiconductors, optics, and other advanced materials.
- The precision of the electron beam ensures uniform and high-quality coatings.
-
Advantages of Electron Beam Processing:
- Precision: The ability to control the electron beam allows for highly accurate modifications to materials.
- Efficiency: The process is fast and can be automated, reducing production time and costs.
- Environmental Benefits: Electron beam processing often eliminates the need for chemicals or high temperatures, reducing waste and energy consumption.
- Versatility: The technology can be applied to a wide range of materials and industries, making it a flexible solution for various challenges.
-
Vacuum Environment:
- Electron beam processing requires a vacuum to prevent interference from air molecules, ensuring the beam remains focused and effective.
- The vacuum also prevents contamination of the materials being processed, which is critical for applications like semiconductor manufacturing and thin-film deposition.
-
Economic and Environmental Impact:
- The technology reduces reliance on chemical processes, lowering environmental impact.
- Its efficiency and precision contribute to cost savings in manufacturing and processing.
- By enabling new material properties and applications, electron beam processing drives innovation across industries.
Electron beam processing is a transformative technology that leverages the unique properties of electrons to modify materials in precise and efficient ways. Its applications span multiple industries, offering both economic and environmental advantages. Whether used for crosslinking polymers, curing composites, or depositing thin films, this technology continues to play a critical role in advancing material science and industrial processes.
Summary Table:
Aspect | Details |
---|---|
Fundamentals | Focused electron beam in a vacuum, controlled by electric/magnetic fields. |
Energy Transfer | Induces physical/chemical changes like crosslinking or chain scissioning. |
Applications | Heat-shrinkable plastics, semiconductor enhancement, food sterilization. |
Advantages | Precision, efficiency, environmental benefits, versatility. |
Vacuum Environment | Ensures beam focus and prevents contamination. |
Economic & Environmental | Reduces chemical use, lowers costs, and drives innovation. |
Unlock the potential of electron beam processing for your industry—contact our experts today!