Film thickness is a critical factor in determining the adhesion of thin films to substrates. While the references provided do not explicitly address film thickness, its impact on adhesion can be inferred through first principles and general material science knowledge. Adhesion is influenced by mechanical interlocking, chemical bonding, and interfacial energy, all of which can be affected by film thickness. Thicker films may introduce stresses or defects, while thinner films might lack sufficient material for strong bonding. Below, the relationship between film thickness and adhesion is explored in detail.
Key Points Explained:
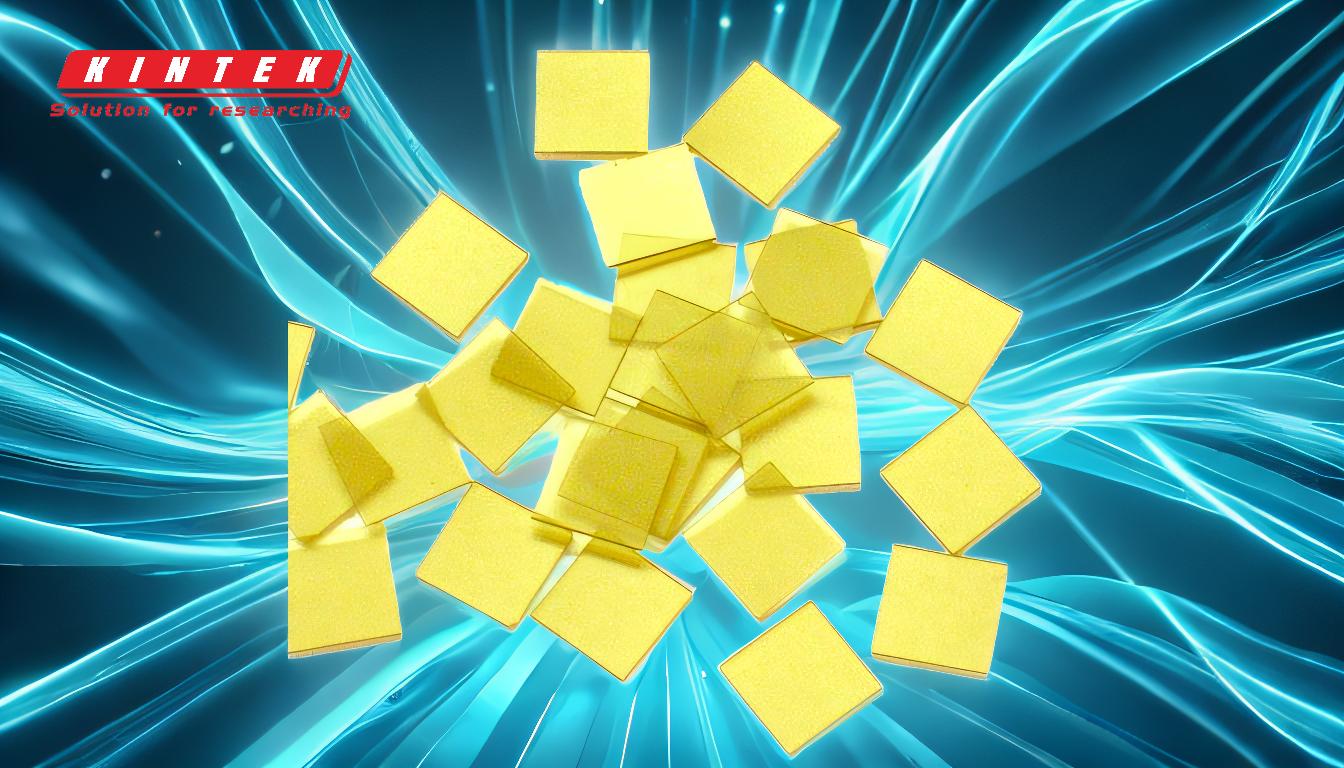
-
Mechanical Interlocking and Film Thickness:
- Explanation: Mechanical interlocking occurs when the film material penetrates surface irregularities or pores on the substrate. Thicker films have more material to fill these irregularities, potentially enhancing adhesion. However, excessively thick films may introduce internal stresses due to uneven cooling or curing, which can weaken adhesion.
- Impact: Optimal film thickness ensures sufficient material for interlocking without introducing stress-related defects.
-
Chemical Bonding and Film Thickness:
- Explanation: Chemical bonding between the film and substrate relies on the availability of reactive sites. Thinner films may not provide enough material to form strong chemical bonds, while thicker films might limit the diffusion of reactive species to the interface, reducing bond strength.
- Impact: A moderate film thickness balances the availability of reactive material and the diffusion of bonding species, maximizing adhesion.
-
Interfacial Energy and Film Thickness:
- Explanation: Interfacial energy is influenced by the contact area between the film and substrate. Thicker films can alter the surface energy distribution, potentially reducing adhesion if the film's properties (e.g., thermal expansion coefficient) differ significantly from the substrate's.
- Impact: Matching film thickness to the substrate's properties minimizes interfacial energy mismatches, improving adhesion.
-
Stress Development in Thicker Films:
- Explanation: Thicker films are more prone to developing internal stresses during deposition or curing due to factors like thermal expansion mismatch or shrinkage. These stresses can lead to delamination or cracking, compromising adhesion.
- Impact: Controlling film thickness to minimize stress development is essential for maintaining strong adhesion.
-
Defects and Film Thickness:
- Explanation: Thicker films are more likely to contain defects such as voids, cracks, or impurities, which can act as weak points in the adhesion interface. Thinner films, while less prone to defects, may lack the structural integrity needed for robust adhesion.
- Impact: A balanced film thickness reduces the likelihood of defects while ensuring sufficient material for adhesion.
-
Deposition Technique and Film Thickness:
- Explanation: The method used to deposit the film (e.g., sputtering, evaporation, or chemical vapor deposition) can influence how film thickness affects adhesion. For example, some techniques may produce more uniform films at specific thicknesses, enhancing adhesion.
- Impact: Selecting a deposition technique compatible with the desired film thickness can optimize adhesion.
-
Substrate Preparation and Film Thickness:
- Explanation: The substrate's surface condition (e.g., roughness, cleanliness) interacts with film thickness to determine adhesion. A thicker film may better accommodate a rough substrate, but poor substrate preparation can negate this advantage.
- Impact: Proper substrate preparation ensures that film thickness contributes positively to adhesion.
-
Interfacial Treatments and Film Thickness:
- Explanation: Treatments like plasma cleaning or adhesion promoters can enhance bonding at the interface. The effectiveness of these treatments may vary with film thickness, as thicker films might dilute the treatment's impact.
- Impact: Tailoring interfacial treatments to the film thickness ensures optimal adhesion.
In summary, film thickness affects adhesion through its influence on mechanical interlocking, chemical bonding, interfacial energy, stress development, defects, deposition techniques, substrate preparation, and interfacial treatments. An optimal film thickness balances these factors to achieve strong and durable adhesion. For equipment and consumable purchasers, understanding this relationship is crucial for selecting the right materials and processes to meet specific adhesion requirements.
Summary Table:
Factor | Impact on Adhesion |
---|---|
Mechanical Interlocking | Thicker films fill irregularities better but may introduce stress-related defects. |
Chemical Bonding | Moderate thickness balances reactive material availability and bonding diffusion. |
Interfacial Energy | Matching thickness to substrate properties minimizes energy mismatches. |
Stress Development | Thicker films are prone to internal stresses, which can weaken adhesion. |
Defects | Thicker films may have more defects, while thinner films lack structural integrity. |
Deposition Technique | Technique choice affects uniformity and adhesion at specific thicknesses. |
Substrate Preparation | Proper preparation ensures thickness contributes positively to adhesion. |
Interfacial Treatments | Treatments must be tailored to film thickness for optimal bonding. |
Need help optimizing film thickness for your adhesion requirements? Contact our experts today!