The speed of a ball mill plays a critical role in determining the efficiency of size reduction. At low speeds, the balls tend to slide or roll over each other, resulting in minimal grinding. At high speeds, centrifugal force throws the balls against the cylinder wall, preventing effective grinding. However, at an optimal or "normal" speed, the balls are lifted to the top of the mill and then cascade down, creating a combination of impact and friction forces that maximize size reduction. The interplay between these forces is essential for achieving the desired particle size, and factors such as ball size, material hardness, and mill filling ratio also influence the process.
Key Points Explained:
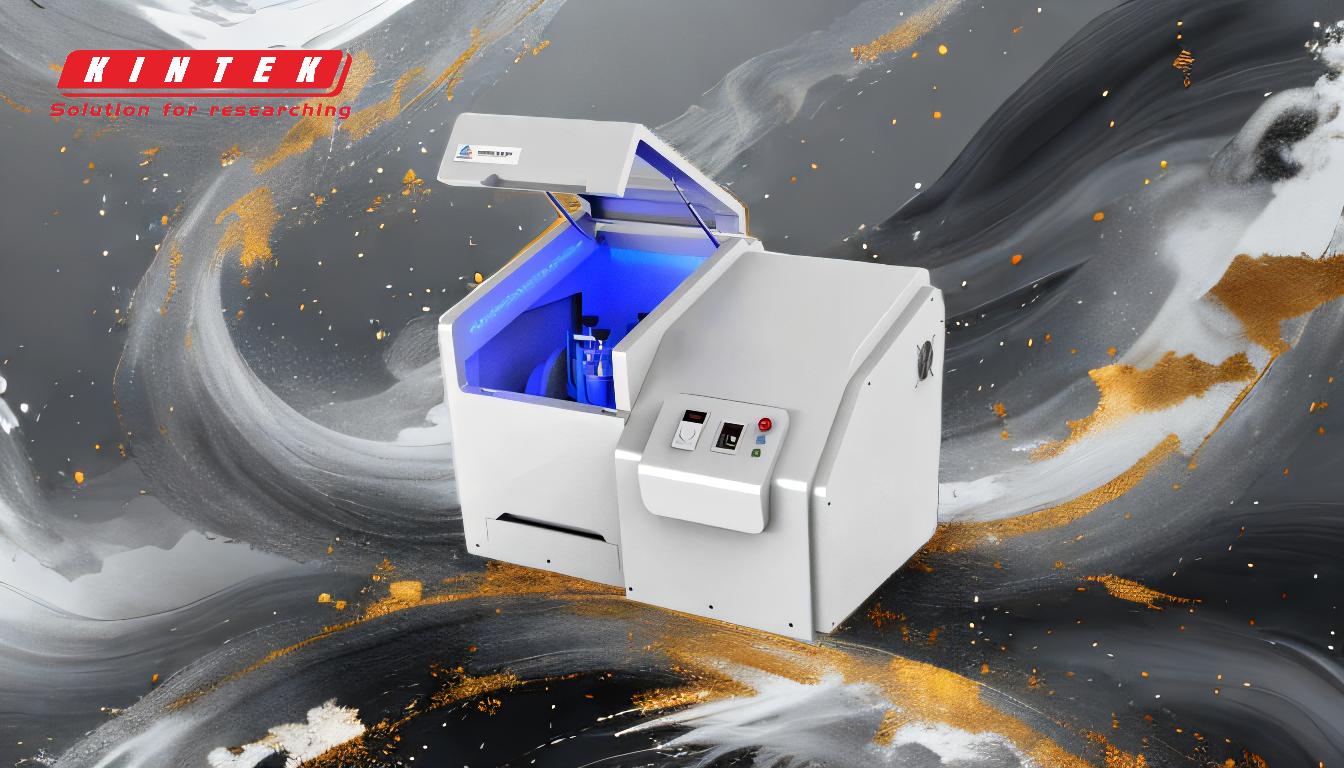
-
Impact of Ball Mill Speed on Size Reduction:
- Low Speed: At low rotational speeds, the balls in the mill slide or roll over each other. This motion generates minimal impact and friction forces, leading to inefficient size reduction. The material is not subjected to sufficient grinding action, resulting in larger particle sizes.
- High Speed: When the mill operates at very high speeds, centrifugal force becomes dominant. The balls are thrown against the cylinder wall and do not cascade back onto the material. This prevents effective grinding, as the balls are unable to impact the material effectively.
- Optimal Speed: At the correct or "normal" speed, the balls are lifted to a certain height before cascading down. This motion creates a combination of impact and friction forces, which are highly effective for size reduction. The cascading action ensures that the material is continuously exposed to grinding forces, leading to maximum particle size reduction.
-
Interplay of Forces in Size Reduction:
- The efficiency of a ball mill depends on the balance between impact forces (from the balls hitting the material) and friction forces (from the balls rubbing against the material and each other). At optimal speed, these forces work together to break down particles effectively.
- The centrifugal force at high speeds disrupts this balance by preventing the balls from cascading, while low speeds fail to generate sufficient force for grinding.
-
Factors Influencing Grinding Efficiency:
- Rotation Speed: As discussed, the speed of the mill directly affects the grinding action. Operating at the optimal speed ensures maximum size reduction.
- Ball Size and Density: Smaller balls and longer grinding times are often required to achieve finer particle sizes. The size and density of the balls determine the energy transferred to the material during impact.
- Material Hardness: Harder materials require more energy to grind, which can be achieved by adjusting the speed and ball size.
- Mill Filling Ratio: The percentage of the mill volume filled with grinding medium (balls) affects the grinding efficiency. Overfilling or underfilling can reduce the effectiveness of the grinding process.
- Residence Time: The amount of time the material spends in the mill chamber influences the degree of size reduction. Longer residence times generally result in finer particles.
-
Practical Considerations for Equipment Purchasers:
- When selecting a ball mill, it is crucial to consider the operational speed range and ensure it aligns with the desired particle size and material properties.
- The type and size of grinding balls should be chosen based on the material being processed and the required particle size.
- Mill capacity and filling ratio should be optimized to balance grinding efficiency and energy consumption.
- Control systems that allow precise adjustment of rotation speed and monitoring of grinding progress can enhance the overall efficiency of the milling process.
-
Conclusion:
- The speed of a ball mill is a critical parameter that directly influences the size reduction process. Operating at the optimal speed ensures a balance between impact and friction forces, leading to efficient grinding. Other factors, such as ball size, material hardness, and mill filling ratio, also play significant roles in determining the final particle size. Equipment purchasers should carefully evaluate these factors to select a ball mill that meets their specific grinding requirements.
Summary Table:
Parameter | Low Speed | High Speed | Optimal Speed |
---|---|---|---|
Ball Motion | Sliding or rolling | Thrown against cylinder wall | Cascading |
Grinding Efficiency | Minimal size reduction | Ineffective grinding | Maximum size reduction |
Forces | Insufficient impact and friction | Dominant centrifugal force | Balanced impact and friction |
Particle Size | Larger particles | Inconsistent particle size | Desired fine particles |
Optimize your grinding process with the right ball mill—contact our experts today for tailored solutions!