Tire pyrolysis is a thermochemical process that decomposes used tires into useful products like fuel oil, carbon black, and steel wire in the absence of oxygen. This process involves heating tires at high temperatures (typically between 300°C to 900°C) in a reactor, breaking down their complex hydrocarbon structure into smaller molecules. The absence of oxygen prevents combustion, ensuring that the tires decompose rather than burn. The resulting products can be refined and reused in various industries, making tire pyrolysis an effective method for recycling and reducing environmental waste. This process is energy-efficient and environmentally friendly, as it minimizes harmful emissions and transforms waste into valuable resources.
Key Points Explained:
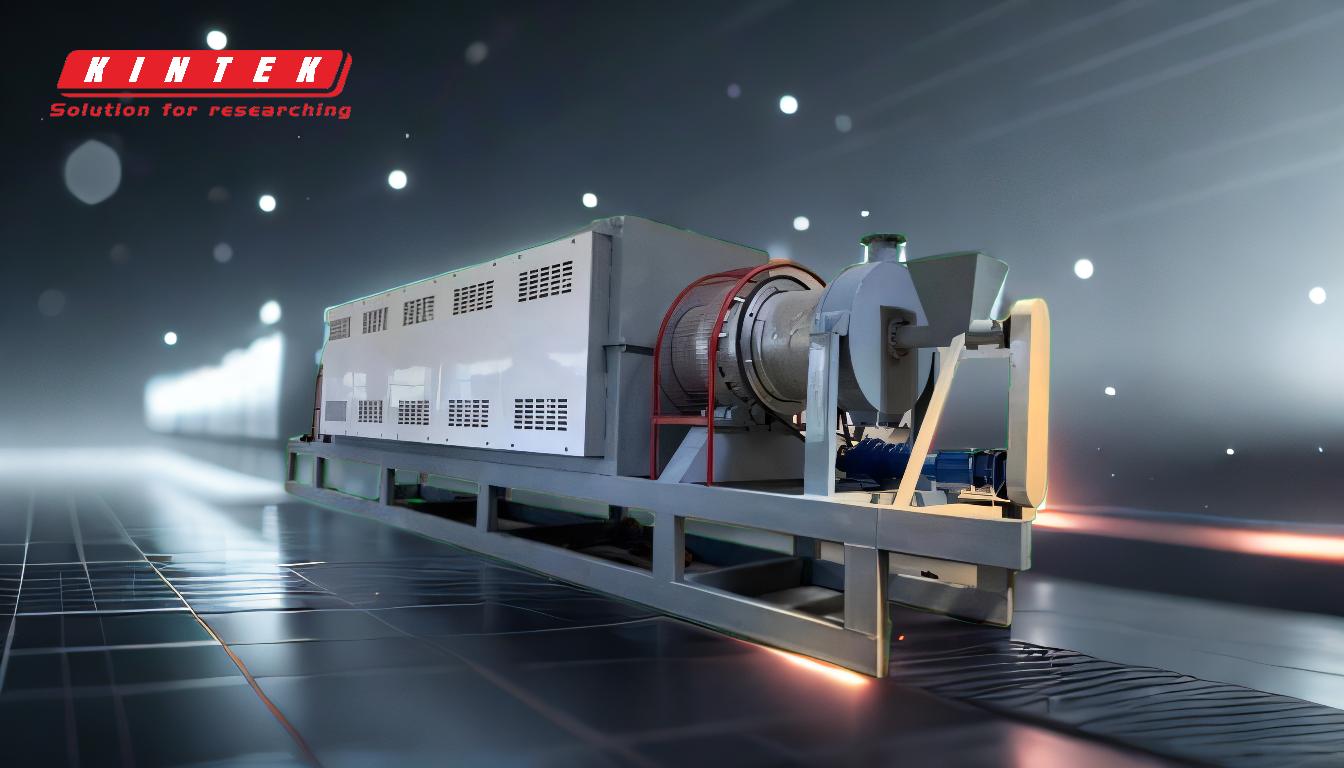
-
What is Tire Pyrolysis?
- Tire pyrolysis is a process that thermally decomposes rubber tires in an oxygen-free environment. This method breaks down the complex polymers in tires into smaller, reusable components such as oil, gas, carbon black, and steel. The process is distinct from incineration, as it does not involve burning, which reduces the release of harmful pollutants.
-
The Pyrolysis Process Steps:
- Feeding: Used tires are shredded and fed into a pyrolysis reactor.
- Heating: The reactor heats the tires to high temperatures (300°C to 900°C) in the absence of oxygen.
- Decomposition: The heat breaks the long-chain hydrocarbons in the tires into smaller molecules, producing gas, oil, and solid residues.
- Cooling and Separation: The resulting gases are condensed into liquid oil, while the solid residues (carbon black and steel) are separated and collected.
-
Products of Tire Pyrolysis:
- Pyrolysis Oil: A liquid fuel that can be used in industrial boilers or further refined into diesel.
- Carbon Black: A fine powder used as a reinforcing agent in rubber products or as a pigment.
- Steel Wire: Recovered from the tires and recycled in the steel industry.
- Syngas: A combustible gas that can be used to power the pyrolysis process or generate electricity.
-
Advantages of Tire Pyrolysis:
- Environmental Benefits: Reduces tire waste in landfills and minimizes pollution by converting waste into useful products.
- Energy Efficiency: The process generates its own energy through syngas, making it self-sustaining.
- Economic Value: The end products (oil, carbon black, and steel) have commercial value, making the process economically viable.
-
Challenges and Considerations:
- High Initial Investment: Setting up a pyrolysis plant requires significant capital for equipment and technology.
- Emission Control: While pyrolysis produces fewer emissions than incineration, proper gas treatment systems are needed to handle any residual pollutants.
- Feedstock Quality: The quality of the input tires can affect the efficiency and output of the process.
-
Applications of Pyrolysis Products:
- Pyrolysis Oil: Used as an alternative fuel in industries or refined for transportation.
- Carbon Black: Utilized in tire manufacturing, plastics, and ink production.
- Steel Wire: Recycled for use in construction and manufacturing.
Tire pyrolysis is a sustainable solution for managing tire waste, offering both environmental and economic benefits. By converting waste tires into valuable resources, this process contributes to a circular economy and reduces reliance on fossil fuels.
Summary Table:
Aspect | Details |
---|---|
Process | Thermal decomposition of tires in an oxygen-free environment. |
Temperature Range | 300°C to 900°C. |
Key Products | Pyrolysis oil, carbon black, steel wire, and syngas. |
Advantages | Reduces landfill waste, energy-efficient, and generates valuable products. |
Challenges | High initial investment and emission control requirements. |
Applications | Fuel, rubber manufacturing, construction, and more. |
Discover how tire pyrolysis can benefit your business—contact us today for expert guidance!