Plastic pyrolysis is a promising technology for converting waste plastic into valuable products such as fuel, gas, and chemicals. Its effectiveness depends on several factors, including the quality and type of plastic feedstock, the pyrolysis technology used, and the operating conditions such as temperature, residence time, and pressure. When optimized, plastic pyrolysis can achieve high yields of useful products, but challenges such as feedstock contamination and reactor efficiency must be addressed. This process is particularly effective for pure, dry, and clean plastics, but its overall efficiency varies based on the specific setup and operational parameters.
Key Points Explained:
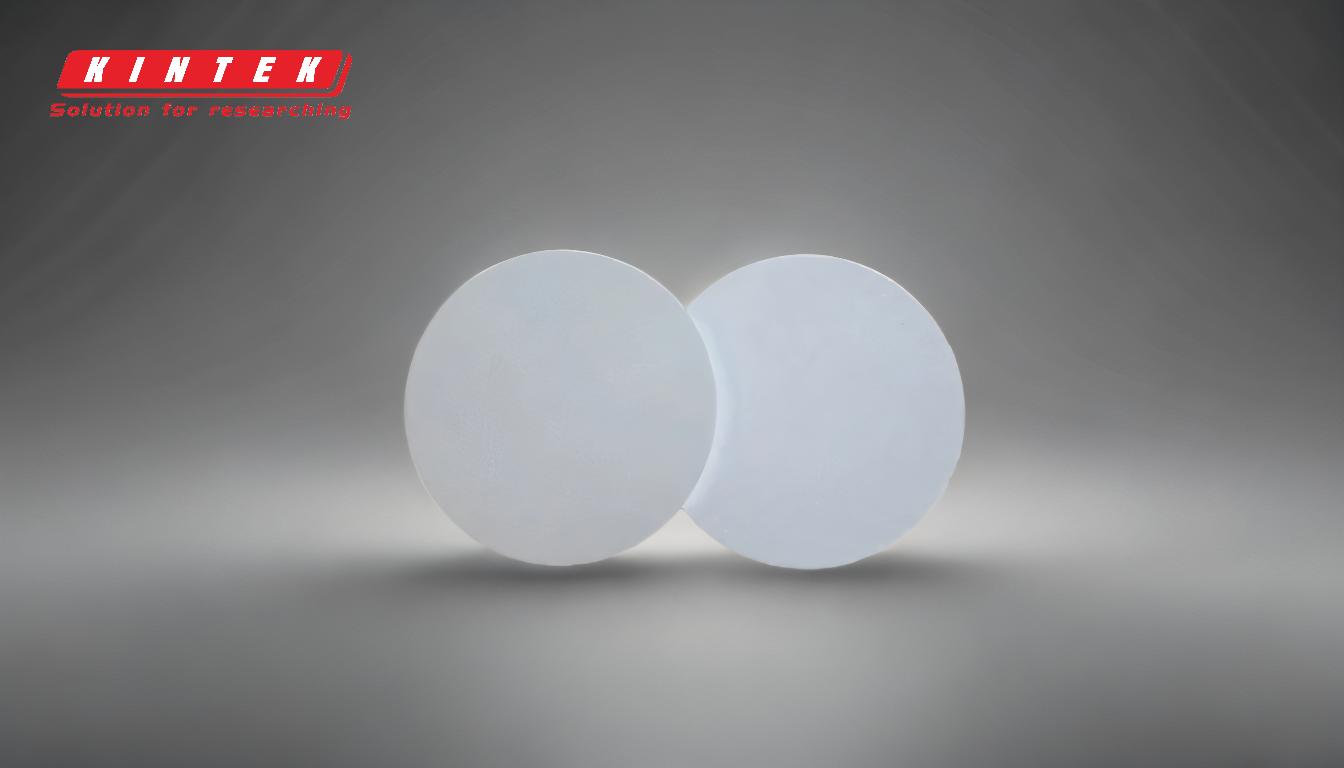
-
Factors Influencing Plastic Pyrolysis Efficiency:
- Feedstock Quality: The type, cleanliness, and moisture content of the waste plastic significantly impact the yield and quality of pyrolysis products. Pure, dry, and clean plastics generally yield better results.
- Pyrolysis Technology: Different reactor designs (e.g., rotary-kiln, tubular) have varying efficiencies. For instance, rotary-kiln reactors depend on heat supply and rotation speed, while tubular reactors rely on flow velocity and heat supply.
-
Operating Conditions: Key parameters include:
- Temperature: Higher temperatures typically increase the conversion rate but must be optimized to avoid excessive gas production.
- Residence Time: Longer residence times allow for more complete degradation of plastics but may reduce throughput.
- Pressure: Controlled pressure settings can influence the distribution of pyrolysis products (gas, liquid, or solid).
-
Product Yield and Quality:
- The yield of pyrolysis products (oil, gas, and char) depends on the feedstock and process conditions. For example:
- Polyethylene and polypropylene tend to produce higher yields of liquid fuels.
- Contaminated or mixed plastics may result in lower-quality outputs or require pre-treatment.
- Proper control of operating conditions ensures a higher proportion of desired products (e.g., liquid fuels) and minimizes unwanted by-products.
- The yield of pyrolysis products (oil, gas, and char) depends on the feedstock and process conditions. For example:
-
Challenges and Limitations:
- Feedstock Variability: Mixed or contaminated plastics can reduce efficiency and require additional sorting or cleaning steps.
- Energy Consumption: Pyrolysis is energy-intensive, and the heat supply must be carefully managed to maintain efficiency.
- Reactor Design: The choice of reactor (e.g., rotary-kiln, tubular) affects heat transfer, residence time, and overall efficiency. Proper design and maintenance are critical for optimal performance.
-
Environmental and Economic Considerations:
- Plastic pyrolysis offers a sustainable solution for managing plastic waste and reducing reliance on fossil fuels. However, its economic viability depends on factors such as:
- Feedstock availability and cost.
- Market demand for pyrolysis products (e.g., fuel oil, syngas).
- Capital and operational costs of pyrolysis plants.
- Environmental benefits include reducing plastic pollution and greenhouse gas emissions, but emissions from the pyrolysis process itself must be controlled.
- Plastic pyrolysis offers a sustainable solution for managing plastic waste and reducing reliance on fossil fuels. However, its economic viability depends on factors such as:
-
Comparison with Other Waste Management Methods:
- Compared to incineration, pyrolysis produces fewer harmful emissions and recovers valuable resources.
- Unlike mechanical recycling, pyrolysis can handle mixed or contaminated plastics, making it a complementary technology in waste management systems.
In conclusion, plastic pyrolysis is an effective method for converting waste plastic into valuable resources, but its success depends on careful optimization of feedstock, technology, and operating conditions. While challenges remain, advancements in reactor design and process control are improving its efficiency and scalability.
Summary Table:
Key Aspect | Details |
---|---|
Feedstock Quality | Pure, dry, and clean plastics yield better results. |
Pyrolysis Technology | Reactor designs (e.g., rotary-kiln, tubular) affect efficiency. |
Operating Conditions | Temperature, residence time, and pressure influence product distribution. |
Product Yield | Polyethylene and polypropylene produce higher liquid fuel yields. |
Challenges | Feedstock contamination, energy consumption, and reactor design limitations. |
Environmental Benefits | Reduces plastic pollution and greenhouse gas emissions. |
Economic Viability | Depends on feedstock cost, market demand, and plant operational costs. |
Ready to explore how plastic pyrolysis can transform your waste management strategy? Contact us today for expert guidance!